The Lean Post / Articles / Lean Management Case Studies Library
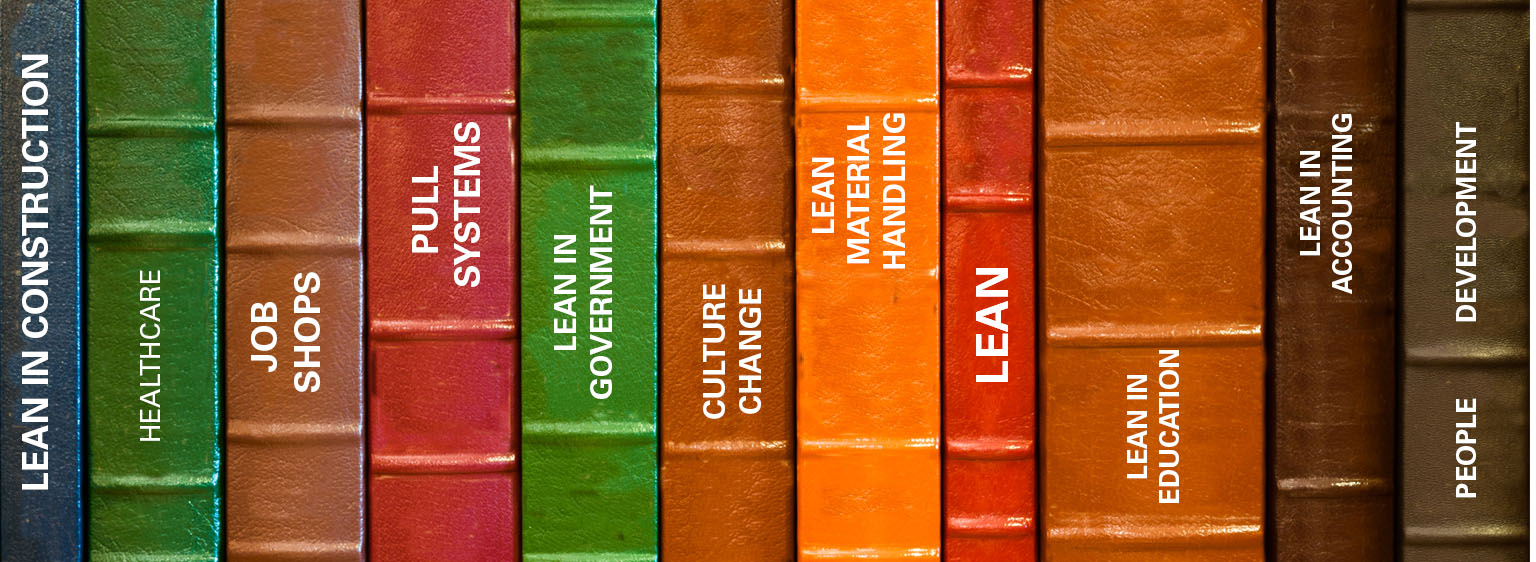

Lean Management Case Studies Library
By Chet Marchwinski
May 16, 2014
Learn how a variety of businesses and organizations used lean management principles to solve real business problems. We’ve arranged the examples in 16 categories to help you find the ones right for your environment.
Lean Management Examples from a Variety of Businesses
The following case studies of lean management principles in action show you how a variety of real businesses solved real business problems under diverse conditions.
We’ve arranged the stories in 16 categories to help you find the examples you need. There is some overlap. For instance, a “Lean Manufacturing” case study may also appear with “Privately Held Companies.”
Lean Manufacturing
- Logistics, Supply Chain, and Warehousing
- Lean Material Handling
- Job Shops (Low-volume, High-mix Manufacturing); Tool and Die
- Lean in Government
- Lean Healthcare
- Lean Accounting
- Lean Construction
- Lean in Office and Service Processes
- Lean in Education
Problem Solving
Pull Systems
Culture Change
People Development
Privately Held Companies
Maintenance
Many of the executives who took part in these transformations are interviewed in LEI’s Senior Executive Series on Lean Leadership . After reading the case studies, be sure to get their personal perspectives on leading change. (Feel free to link to this page, but please respect the copyrights of LEI and journalists by not copying the articles.)
Are you doing something new or notable in the practice of lean management? Let us share what you learned with the lean community. For more information, contact LEI’s Director of Communications Chet Marchwinski at cmarchwinski at lean dot org
Thrustmaster Turns Around
Learn how Thrustmaster of Texas successfully adopted lean thinking and practices to make sustainable improvements in a short period of time, and how other manufacturers of highly engineered, low-volume products can follow their lead using the Lean Transformation Framework.
Lean + Circular Principals = a New True North for Manufacturer
SunPower’s lean journey resembled most others until it defined a new mission, a new True North by combining lean principals with those of the “circular economy” to launch what it is calling a CLean Transformation.
Sustain Your Lean Business System with a “Golden Triangle” After a medical device maker took a hit to margins to fight off global competition, it rebuilt them by lifting its lean operating system to a higher level and keeping it there with a “golden triangle” of sustainability.
Followup Story:
Manufacturing Balancing Act: Pull Versus ERP
In this follow-up to “Sustain Your Lean Business System with a ‘Golden Triangle,’” a case study about Phase 2 Medical Manufacturing, the company needs warehouse space to keep pace with sales growth spurred by the lean transformation. Instead, it expands a pull system by connecting the plan-for-every-part database that underpins one-piece flow production with ERP, typically associated with big batch production.
Cultivating a Lean Problem-Solving Culture at O.C. Tanner If you are in the “appreciation business”, you have to live it in your own workplace. For O.C. Tanner that meant a lean transformation had to show the company appreciated and wanted people’s problem-solving ideas. Here’s a report on that effort, including what worked and what didn’t.
Lean Partnership with Dealer Network Helps Vermeer Reduce End-to-End Inventory on Top Sellers
A lean transformation had taken heavy-equipment manufacturer Vermeer away from batch manufacturing, but batch ordering by dealers was delaying how quickly they got equipment like brush chippers. Learn how it began converting its domestic industrial-line distribution network to lean replenishment, improving service to end customers and improving cash flow for Vermeer and its dealers.
Herman Miller’s Experiment in Excellence At Herman Miller, the lean management effort helps it build problem solvers as well as world-class office furniture. And as this case study shows, lean practices also helped it weather a brutal recession.
Build Your “House” of Production on a Stable Foundation Rigorous problem solving creates basic stability in a machining intensive facility.
A Journey to Value Streams: Reorganizing Into Five Groups Drives Lean Improvements and Customer Responsiveness An approach to creating a value -stream culture centered on autonomy, entrepreneurialism, and lean principles.
Change in Implementation Approach Opens the Door at EMCO to Greater Gains in Less Time A relatively quick, intensive project accelerates the rate of improvement and creates a showcase facility for spreading lean concepts.
Creating the Course and Tools for a Lean Accounting System A lean accounting implementation fills the frustrating disconnect between shop-floor improvements and financial statements.
For Athletic Shoe Company, the Soul of Lean Management Is Problem Solving After taking a lean tools approach to change, management re-organized the transformation around problem solving and process improvement to create a culture that engaged people while boosting performance.
Knife Company Hones Competitiveness by Bucking the Status Quo An iconic family-owned company turns to lean manufacturing to reduce costs by at least 30% to keep its U.S. operations open.
Lean Transformation Lives and Dies with Tools and Dies After a failed first try at just-in-time production , a company transforms tool maintenance, design, and fabrication to create a solid foundation for a second attempt.
Seasoned Lean Effort Avoids “Flavor-of-the-Month” Pitfall A look at how one company’s approach to what new tools it introduced, in what order, and how it prevented each new technique from being viewed as a “flavor of the month” fad.
Shifting to Value-Stream Managers: a Shop-Floor Revolution Leads to a Revolution in Plant Organization
Two years into a lean transformation, the low-hanging fruit has been plucked and progress has started to slow. Read how a Thomas & Betts plant recharged the transformation and reached higher levels of performance by using value-stream managers to span functional walls.
Using Plan-Do-Check-Act as a Strategy and Tactic for Helping Suppliers Improve
At Medtronic’s Neuromodulation business unit, the plan-do-check-act cycle is used on a strategic level to guide overall strategy for selecting and developing key suppliers as well as on a tactical level for guiding lean transformations at supplier facilities.
back to top
Logistics, Supply Chain, and Warehousing How a Retailer’s Distribution Center Exemplifies the Lean Precept “Respect for People,” and Reaps the Benefits
To make sure training engaged and resonated with people after previous attempts at a lean transformation faltered, LifeWay matched lean management tools and principles to its Bible-based culture and language.
Lean management case study series: Lean in Distribution: Go to Where the Action Is!
Starting with daily management walkabouts and standard work , this distributor had laid the groundwork for steady gains for years to come, just two years after its first kaizen workshop .
Putting Lean Principles in the Warehouse
Executives at Menlo Worldwide Logistics saw an opportunity to leapfrog the competition by embracing lean in its outsourced warehousing and receiving operations.
Lean Thinking Therapy Spreads Beyond the Shop
A company expands the lean transformation from the shop floor to international distribution, domestic shipping, and product development.
Sell One, Buy One, Make One: Transforming from Conventional to Lean Distribution
Large inventories to cover fluctuations in demand once characterized Toyota’s service parts distribution system — but no more. Here’s how one DC made the switch.
Material Handling
Following Four Steps to a Lean Material-Handling System Leads to a Leap in Performance
Creating the critical Plan for Every Part was one step in a methodical four-step implementation process to replace a traditional material-handling system.
Low-volume, High-mix Manufacturing; Tool and Die
The Backbone of Lean in the Back Shops
Sikorsky managers apply the lean concept of “every part, every interval” (EPEI) to level the mix in demand and create flow through a key manufacturing cell .
Landscape Forms Cultivates Lean to Fuel Growth Goals
With single-item orders 80% of the time, a low-volume, high-mix manufacturer decided single-piece flow cells were the best way decided the best way to add new products without having to constantly reconfigure production.
Lean Transformation Lives and Dies with Tools and Dies
After a failed first try at just-in-time production, a company transforms tool maintenance, design, and fabrication to create a solid foundation for a second attempt.
Canada Post Puts Its Stamp on a Lean Transformation
The “ inventory ” of mail already is paid for, so moving it faster doesn’t improve cash flow as in lean manufacturing. But Canada Post discovered that traditional batch-and-queue postal operations could benefit from lean principles.
Lean Thinking in Government: The State of Iowa
This story examines a kaizen event at a veterans home and more broadly at the lean effort in Iowa government.
Lean Thinking Helps City of Chula Vista with Budget Crunch
Goodrich Aerostructures’ Chula Vista plant introduces city government to lean thinking and practices so in order to maintain municipal services without resorting to further cuts in the workforce.
Using Lean Thinking to Reinvent City Government
Grand Rapids, MI, turns to lean principles to consolidate operations, eliminate wasted time and effort, and streamline to improve productivity while providing the quality of service that residents want.
Transforming Healthcare: What Matters Most? How the Cleveland Clinic Is Cultivating a Problem-Solving Mindset and Building a Culture of Improvement
The Cleveland Clinic reinvents its continuous improvement program to instill a problem-solving mindset and the skillset to solve everyday problems among the clinic’s thousands of caregivers.
View from the Hospital Floor: How to Build a Culture of Improvement One Unit at a Time
In order to do more and improve faster, the Cleveland Clinic is rolling out a methodology for building a “culture of improvement” across the 48,000-employee hospital system as this followup to the above story shows. Here’s how it works according to the people making the changes.
Dentist Drills Down to the Root Causes of Office Waste
Dentistry is a job shop that Dr. Sami Bahri is out to improve fundamentally for the benefit of patients through the application of lean principles.
Lean management case study series: Pediatric Hospital in Tough Market Pegs Growth to Lean Process Improvement
Lean improvement projects at Akron Children’s Hospital have saved millions of dollars, increased utilization of expensive assets, and reduced wait times for patients and their families.
Lean Design and Construction Project an Extension of Lean Commitment at Akron Children’s Hospital
Input from nurses, doctors, therapists, technicians, and patient parents heavily influenced design decisions..
“Pulling” Lean Through a Hospital
A thoughtful rollout of lean principles in the ER and eye-opening results created a “pull” for lean from other departments.
Best in Healthcare Getting Better with Lean
Mayo Clinic, Rochester, MN, stresses to doctors that the lean effort is aimed not at changing the moment of care, the touch moment between doctor and patient, but the 95% of the time when the patient is not in the doctor’s office
Fighting Cancer with Linear Accelerators and Accelerated Processes
Cross-functional team design and implement a lean process to dramatically increase the number of patients with brain and bone metastases receiving consultation, simulation, and first treatment on the same day without workarounds or expediting.
Massachusetts General Looks to Lean
A proton therapy treatment center, for many adults and children the best hope of beating cancer, applies lean principles to increase capacity.
New Facility, New Flow, and New Levels of Patient Care: The wait is over for patients at the Clearview Cancer Institute in Alabama
Physicians and staff have tirelessly reengineer processes and patient flow to eliminate as much waiting and waste as possible.
The Anatomy of Innovation
At a hospital in Pittsburgh, the emerging vision for the “hospital of the future” is described as giving the right patient, the right care, at the right time, in the right way, all the time.
Creating the Course and Tools for a Lean Accounting System
A lean accounting implementation fills the frustrating disconnect between shop-floor improvements and the financial statement.
Knife Company Hones Competitiveness by Bucking the Status Quo
An iconic family-owned company turns to lean manufacturing to reduce costs by at least 30% to keep its U.S. operations open.
Office and Service Processes
The “inventory” of mail already is paid for, so moving it faster doesn’t improve cash flow as in lean manufacturing. But Canada Post discovered that traditional batch-and-queue postal operations could benefit from lean principles.
Lean Landscapers
At an Atlanta landscaping company, lean practices are making inroads into a service industry in unusual yet fundamental ways.
LSG Sky Chefs Caters to New Market Realities
Business at airline caterer LSG Sky Chefs dropped 30% when airlines cut flights after the terrorist attacks on September 11, 2001. Sky Chefs responded with a rapid launch of a lean initiative.
leveraging Lean to Get the Oil Out
Aera Energy LLC, a California oil and gas company, relies on lean principles to improve key processes, including drilling new wells, repairing existing ones, and maximizing the number of barrels of crude pumped each day.
Columbus Public Schools Use Process Thinking to Improve Academic Achievement.
Columbus, OH, public schools, experiment with lean tools and process thinking to remove wasteful activities that don’t help them help students learn.
Lean Inroads into Alabama Academia
How the University of Alabama in Huntsville integrated lean concepts throughout its industrial engineering curriculum.
Linking Lean Thinking to the Classroom
Value-stream mapping is one of many activities included in the Ford Partnership for Advanced Studies (Ford PAS), an academic program designed to link high-school classroom learning to the skills needed in college and business.
Build Your “House” of Production on a Stable Foundation
Rigorous problem solving creates basic stability in a machining intensive facility.
For Athletic Shoe Company, the Soul of Lean Management Is Problem Solving
After talking a lean tools approach to change, management re-organized the transformation around problem solving and process improvement to create a culture that engaged people while boosting performance.
Toothbrush Plant Reverses Decay in Competitiveness
The rapid introduction of a lean system, beginning with just-in-time production and pull, helps a highly automated Midwest plant fight off overseas competition by reducing lead times and inventory while augmenting the plant’s advantage in service.
A Journey to Value Streams: Reorganizing Into Five Groups Drives Lean Improvements and Customer Responsiveness
An approach to creating a value-stream culture centered on autonomy, entrepreneurialism, and lean principles.
Making Lean Leaders — Ariens internship program develops lean and leadership skills
Besides making snow-blowers, mowers, and string trimmers, Ariens Co., of Brillion, WI, makes lean leaders.
Starting with daily management walkabouts and standard work, this 84-year-old, family-owned distributor laid the groundwork for steady gains for years to come, just two years after its first kaizen workshop.
Sustain Your Lean Business System with a “Golden Triangle”
After a medical device maker took a hit to margins to fight off global competition, it rebuilt them by lifting its lean operating system to a higher level and keeping it there with a “golden triangle” of sustainability. You’ll recognize two elements of the triangle right away: visual control and standardized work . The third, accountability management or a kamishibai system, is probably less well known but just as critical.
Cultivating a Lean Problem-Solving Culture at O.C. Tanner
If you are in the “appreciation business”, you have to live it in your own workplace. For O.C. Tanner that meant a lean transformation had to show the company appreciated and wanted people’s problem-solving ideas. Here’s a report on that effort, including what worked and what didn’t.
Lean Thinking in Aircraft Repair and Maintenance Takes Wing at FedEx Express
A major check that used to take 32,715 man-hours was cut to 21,535 hours in six months. That translated into a $2 million savings, which dovetailed with the company’s emphasis on reducing costs during the recession.
Construction
Input from nurses, doctors, therapists, technicians, and patient parents heavily influenced design decisions—from incorporating emergency room hallways that protect the privacy of abused children to the number of electrical outlets in each neonatal intensive care room.
Virtual Lean Learning Experience (VLX)
A continuing education service offering the latest in lean leadership and management.
Written by:
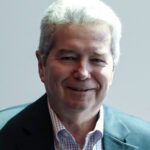
About Chet Marchwinski
Chet has been a humble, unwashed scribe of the lean continuous improvement movement since books by Taiichi Ohno and Shigeo Shingo first hit North America in the 1980s. At LEI, he contributes to content creation, marketing, public relations, and social media. Previously, he also wrote case studies on lean management implementations in…
Leave a Comment Cancel reply
Your email address will not be published. Required fields are marked *
Save my name, email, and website in this browser for the next time I comment.
Be the first to learn of new learning opportunities and the latest practical, actionable information. Subscribe to an LEI newsletter.
Join us on social, privacy overview.
- Our Courses
- About DCM Learning
- Inhouse Training
- Training Resources

Lean Six Sigma Project Examples | 17 Full Case Studies
Ready to begin your first Lean Six Sigma project? Looking for examples for inspiration or reference to get you started? Here are some project storyboards from different industries and from home. Remember, Lean Six Sigma can help you with more than just work!
- Reducing Underwriting Resubmits by Over 20%
Governments
- A Call to Change: Pioneering Lean Six Sigma at Los Angeles County
- Can Lean Six Sigma Be Applied in County Government?
- How the City of San Antonio Increased Payments for Street Maintenance Using Lean Six Sigma
- Reducing Bid Tab Creation Cycle Time by 22%
- Reducing Cycle Time for Natural Disaster Response by 50%
Manufacturing
- Increasing First Run Parts From 60% to 90% With Lean Six Sigma
- Reducing Bent/Scratched/Damaged (BSD) Scrap for Building Envelopes
- Reducing Lead Time in Customer Replacement Part Orders by 41%
- Reducing Learning Curve Ramp for Temp Employees by 2 Weeks
- Reducing Purchase Order Lead Time by 33% Using Lean Six Sigma
- Herding Cats Using Lean Six Sigma: How to Plan for and Manage the Chaos of Parallel Processes
- Lean Six Sigma Increases Daily Meat Production by 25%
- Lean Six Sigma Helps Feed People In Need 45% Faster
- Accelerating Lean Productivity With Immersive Collaboration
- Reducing Incorrect Router Installations by 60% for Call One
- Reducing Software Bug Fix Lead Time From 25 to 15 Days
Lean Reviews: Stories from Our Customers
Over the past 2 years, over 2,000 learners (2,197 to be exact) have come to DCM to learn more about lean and get certified. Read (and watch) their reviews to see how our courses have helped them achieve their career goals.
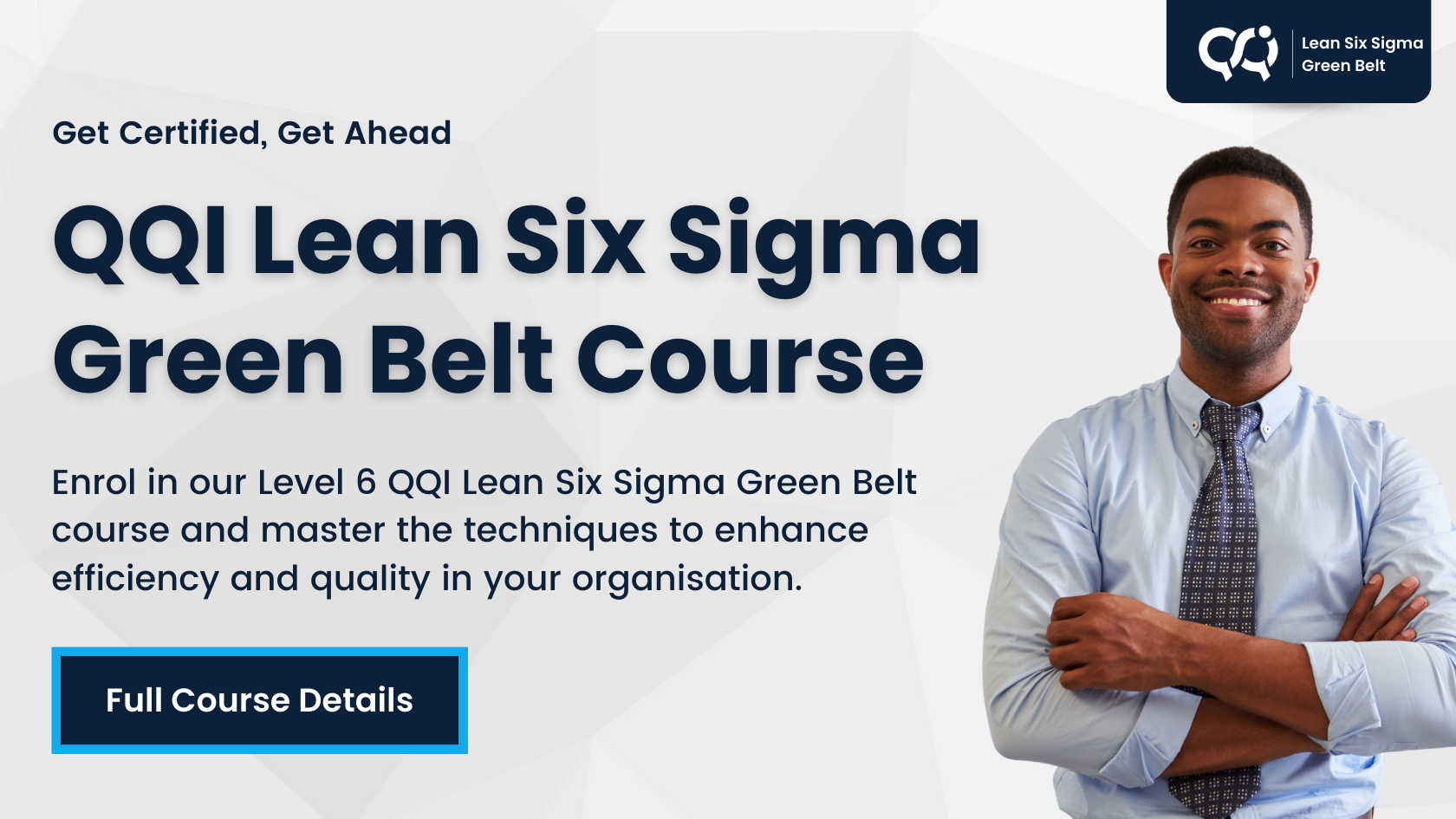
Inhouse Tailored Training for Your Team
We provide training programs that are developed by industry, for industry. Our range of programs can be delivered in a way that suits the needs of your business to offer your employees learning that is accessible and flexible.
We add value to your business by providing specialised, flexible and scalable training that meets your training needs. As your workforce grows and evolves, our globally certified and industry-validated learning solutions can assess, train and qualify your employees. For more information on how we can help please visit the in-house training page .
Membership, Stay Connected. Stay Relevant.
Completing a program is a point-in-time exercise that delivers huge value, but there is a next step to maintaining the currency of your skills in the ever-evolving professional world.
Membership is the next step .
A unique platform, membership is designed to ensure that you are in tune and up-to-date with the latest tools, trends and developments. Being a member provides just-in-time training and continuous professional development, and an exclusive and evolving content library informed by subject matter experts and industry leaders.
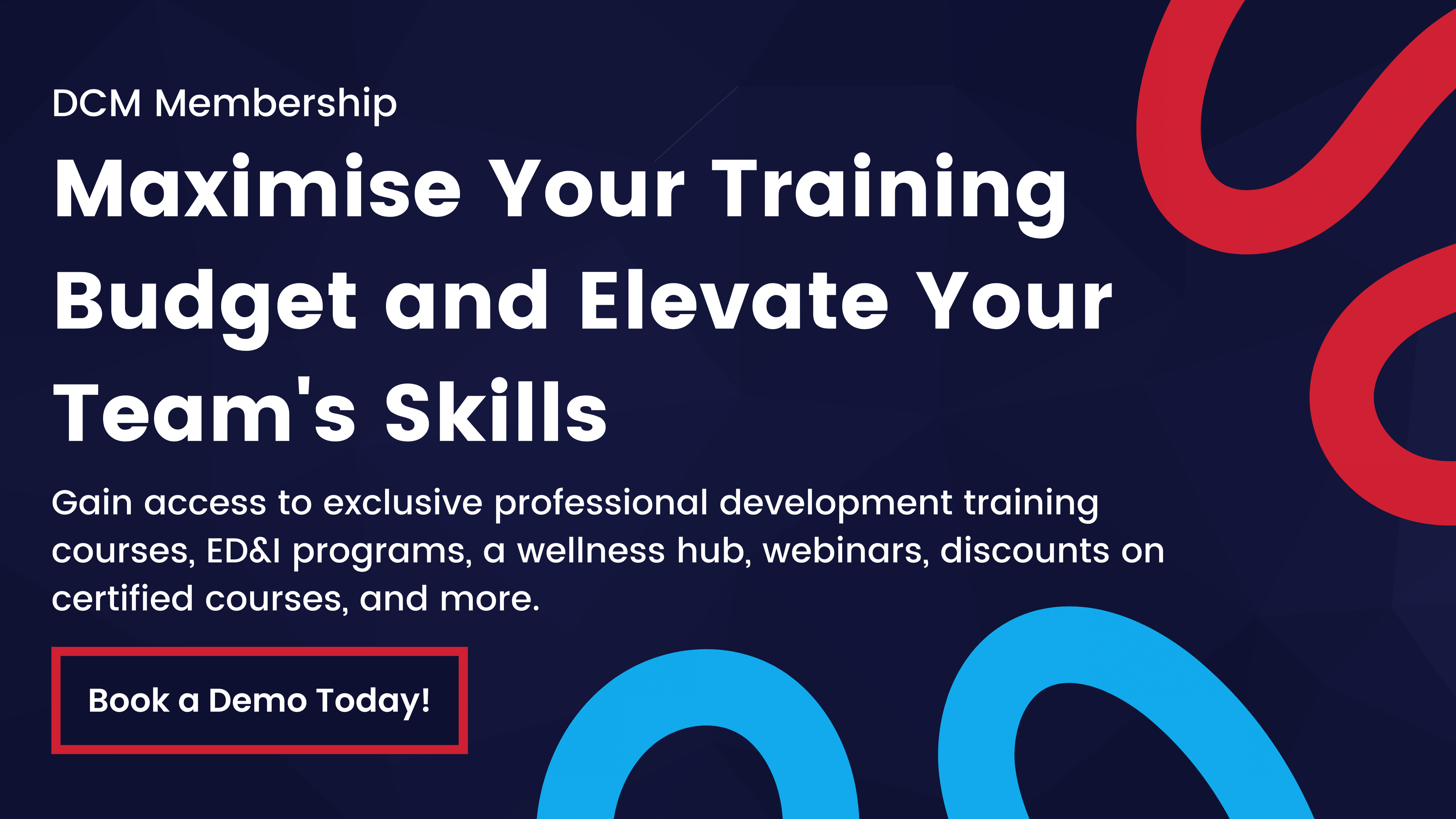
Our expert team is ready to support you from start to finish and answer any questions you have. Submit your email and we'll be in touch shortly to assist you.
Thanks for signing up. Here are some training courses for you to explore.
By clicking “Start Learning”, you agree to our terms and privacy policy .
Free Bitesize Courses
We have over 100 free courses available to explore, all created by expert trainers, packed full of practical exercises and real-world examples.
Make sure you Safeguard Your Training Investment . DCM offer courses accredited by:
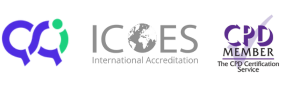
Course Categories

*Add your email and we will send you the full course directory to review at a time that suits you.
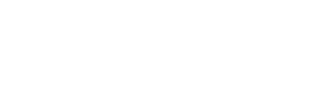
Open Your Brochure
Just to let you know, we are offering €200 credit for the course when you become a member with DCM.
We are very proud of our advisory team in DCM Learning. If you have any questions at all please feel free to ask our team. They will be more than happy to help.
We value your privacy and we will only get in touch about upcoming courses or events that are available to members.
It's so simple... We'll send you the €200 credit and access to the exclusive members area with a full list of the free courses.
By clicking “Get Your Voucher”, you agree to our terms and privacy policy .
The Definitive Guide to Lean Project Management
By Kate Eby | June 23, 2017
- Share on Facebook
- Share on LinkedIn
Link copied
Lean is an often-used adjective in business these days, but there’s some confusion over its exact definition. In essence, the goal of Lean is to maximize value while minimizing waste. In other words, creating more value for the customer with fewer resources. Lean was born on the factory floor, so many people think of it as a manufacturing technique. However, that’s a misconception because every process, whether in production or services, can benefit from a Lean approach. Today, Lean is finding a home in every industry from finance to healthcare. In this article, we will demystify Lean – where it came from, how to apply it in project management today, and the management methodologies it gave birth to including Six Sigma, the Deming Cycle, and Kanban. You’ll find useful templates, worksheets, and checklists along with case studies and project examples to help guide you through your implementation of Lean.
The Origins of Lean Project Management
The story of Lean begins in post-World War II. Japan’s devastation during the war led to scarce equipment and resources, and manufacturers had to invent ways to thrive in a new economic environment. The United States sent consultants to Japan to help the country’s manufacturers rebuild their production capabilities. One of these experts was W. Edwards Deming, a management consultant whose ideas about quality control found more receptive audiences in Japan than they had in the United States. It was from these consultants, as well as from visits to Ford and American supermarket chains, that Japanese manufacturers, and Toyota in particular, refined the concept of Just in Time (JIT) . This technique aims to increase efficiency and decrease the amount of stocked inventory by moving materials into position just before they are needed for the next stage of the production process. JIT is not used solely in manufacturing - the technique applies in any situation where a supplier delivers materials using a timeline determined by customer demand. The success of JIT depends on the ability to synchronize and coordinate steps of the manufacturing process so that materials and products are where they need to be, when they need to be there. In the 1950s, JIT, in combination with the Japanese manufacturing method of Jidoka or autonomation (automation with a human touch on an exceptions basis), would become the twin foundations of the Toyota Production System (TPS). Many consider Toyota engineer Taiichi Ohno the father of TPS and Lean. TPS was geared towards meeting the needs of the Japanese markets at the time, which called for smaller numbers of several different vehicle types. Its core principle was the systematic removal of waste in an ongoing effort to improve efficiency. A couple of decades later, after the 1973 Arab oil embargo caused energy crises in the United States, Japan, Canada, UK, and the Netherlands, other Japanese companies began to study and imitate TPS. By now, the benefits of TPS were clear. It brought:
- Reduced lead times
- Lower inventories
- Decreased costs
- Improved productivity
- Higher profit margins
- Increased product quality
- Greater customer satisfaction
The concepts of Muda, Muri, and Mura (three types of waste that are known as the 3M) are central to the idea of eliminating waste. Muda refers to activities that consume resources without increasing the end value delivered to the customer. Muri refers to practices that involve overusing equipment or overworking employees beyond reasonable or practical limits - both of which increase costs and decrease efficiency and productivity in the long run. Mura describes operational “unevenness,” which can be thought of as the irregular performance of work that increases costs and possibly decreases efficiency over time.
Project Management Guide
Your one-stop shop for everything project management
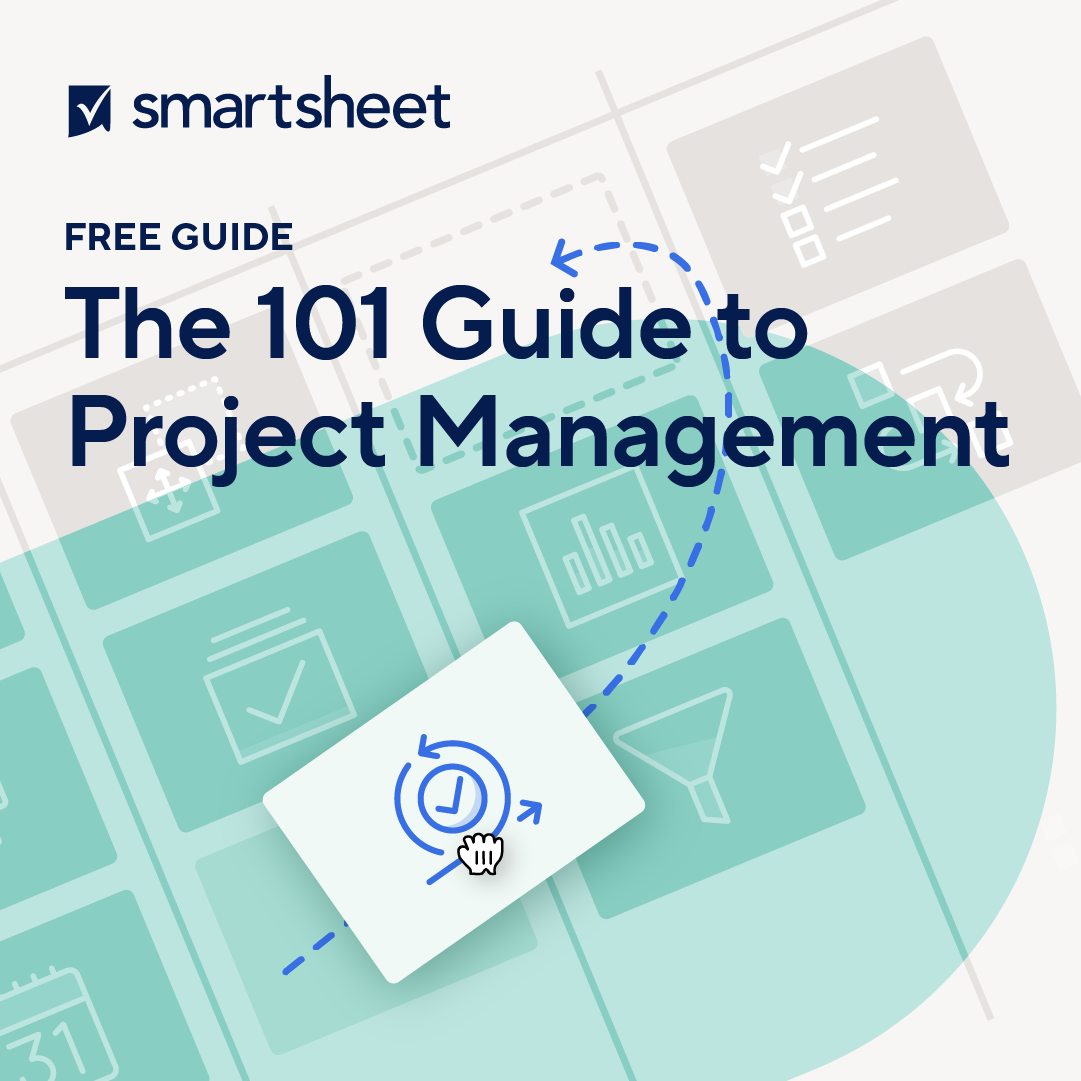
Ready to get more out of your project management efforts? Visit our comprehensive project management guide for tips, best practices, and free resources to manage your work more effectively.
View the guide
Lean Migrates From Japan to the West
In the 1980s, Western manufacturers discovered that Japanese companies were outperforming them. They tried emulating TPS, employing it under such names as World Class Manufacturing, Stockless Production, and Continuous Flow Manufacturing. Manufacturers also began to implement some of the Lean manufacturing techniques, though in isolation from the overarching business management philosophy. In 1988, a quality-engineer-turned-MBA-student named John Krafcik wrote an article that began a paradigm shift in American manufacturing. Krafcik, who had worked at New United Motor Manufacturing, Inc. (NUMMI), a car manufacturing company jointly owned by GM and Toyota, published Triumph of the Lean Production System based on his Master’s thesis at MIT. Scholars at MIT’s International Motor Vehicle Program continued his research into Lean production. In 1990, three scholars, James P. Womack, Daniel T. Jones, and Daniel Roos, released an international bestseller, The Machine that Changed the World , that played a hugely important role in disseminating the concept of Lean manufacturing in the West. In that book and Lean Thinking , the principles of Lean were introduced in a way that allowed Western manufacturers to understand the full extent of its benefits.
Lean Thinking: The Spread of Lean’s Influence
The principles of Lean manufacturing, now more broadly referred to as Lean thinking , have since been adopted outside of traditional manufacturing in fields like construction, healthcare, financial services, government, project management, and knowledge work. Using Lean for knowledge work has been met with some doubt and resistance by people who argue that because the field is essentially non-replicable and non-repetitive, it is not suited to standardization. Bradley Staats and David M. Upton argue in Harvard Business Review , however, that all companies specializing in knowledge work will perform non-knowledge-based activities that are suited to waste reduction efforts. Furthermore, you can even streamline sequences of core knowledge-based activities to achieve greater efficiencies. For example, take Kanban , a Toyota practice that uses visual aids (such as signs, cards, or sticky notes) to match inventory with demand throughout the production life cycle. This makes process inefficiencies, bottlenecks, and other types of waste apparent. Kanban has been successfully used in software development, by visualizing the software development process as a production chain, identifying positions and situations that cause inefficiency in the production chain, and implementing solutions to increase the overall efficiency of the production chain. Lean has had widespread influence. For example, the Lean Aerospace Initiative was a 1992 US Air Force-funded pilot project at MIT that examined the use of Lean techniques in manufacturing aerospace products. The project was renamed the Lean Advancement Initiative until it disbanded in 2012. Healthcare, financial services, education, retail, construction, and other fields currently incorporate the principles of Lean based on the TPS. Because Lean is a paradigm that governs everything an organization does, rather than a single tactic or initiative aimed at a narrow outcome, it can be applied to a range of industry and organization-types.
Ultimately, Lean transformations today focus on shifting an organization’s thinking so that it optimizes its purpose (providing greater value to the customer), process (maximizing workflow productivity) and people (how the team can best engage in continual improvement).
Applying Lean to Project Management
A Project Management Institute conference paper by Aziz Moujib describes Lean project management as the application of Lean manufacturing principles to the project management process. This is in an effort to achieve the same goal: maximizing value while minimizing waste. It draws from a set of five core principles identified in the book Lean Thinking: Banish Waste and Create Wealth in Your Corporation , which was written by two of the three MIT authors who wrote The M achine that Changed the World . The concept of the value stream is central to Lean project management. This is the sequence of activities involved in delivering a project with an agreed-upon value (both the inputs and outputs). Value stream mapping, sometimes called business process mapping , an effort to understand how value and waste are created during the project lifecycle with the goal of optimizing the value stream. In doing so, Lean project management can help achieve a number of goals including:
- Improving the quality of the final product
- Completing the project on time, and reducing the time to completion
- Completing the project on budget and meeting project performance requirements
- Eliminating waste
- Reducing costs
- Adding value
Standardization is another critical aspect of Lean project management. Since most projects are novel (to some extent), standardizing tasks can both improve project performance in the short term and help improve efficiencies for projects with similar tasks in the long term. Improvement of tasks in the project lifecycle tends to be incremental, leading to gradual progress towards goals.
The Five Core Principles of Lean Thinking
The adoption of Lean thinking owes much to how it was presented to James P. Womack and Daniel T. Jones, the authors of The Machine that Changed the World and Lean Thinking . Womack and Jones defined five core principles of Lean thinking: Understand Value: The first principle stresses understanding a product’s (or service’s) value in the eyes of the customer. The amount a customer is willing to pay for a product or service is directly related to how much they value it, so understanding the value of a product is the first step towards effective pricing and Lean management. Toyota, for example, adopted a top-down pricing approach defined by how much customers were willing to pay for a product with a certain value, and then focused on eliminating waste from their manufacturing processes in order to meet this price. Map the Value Stream: The value stream is the complete sequence of activities involved in delivering an end-product with an agreed-upon value, and mapping the value stream means using visualization techniques such as Kanban , flowcharts, or spaghetti diagrams to represent this flow. Toyota pioneered the technique of value stream mapping, which allows business managers and strategists to identify parts of the value stream where waste occurs, and optimize the value stream to reduce waste. A spaghetti diagram is a great starting point because it visually documents the actual flow of product, paper, and people in a workplace or project workflow. Use the template for a spaghetti diagram below to make your own.
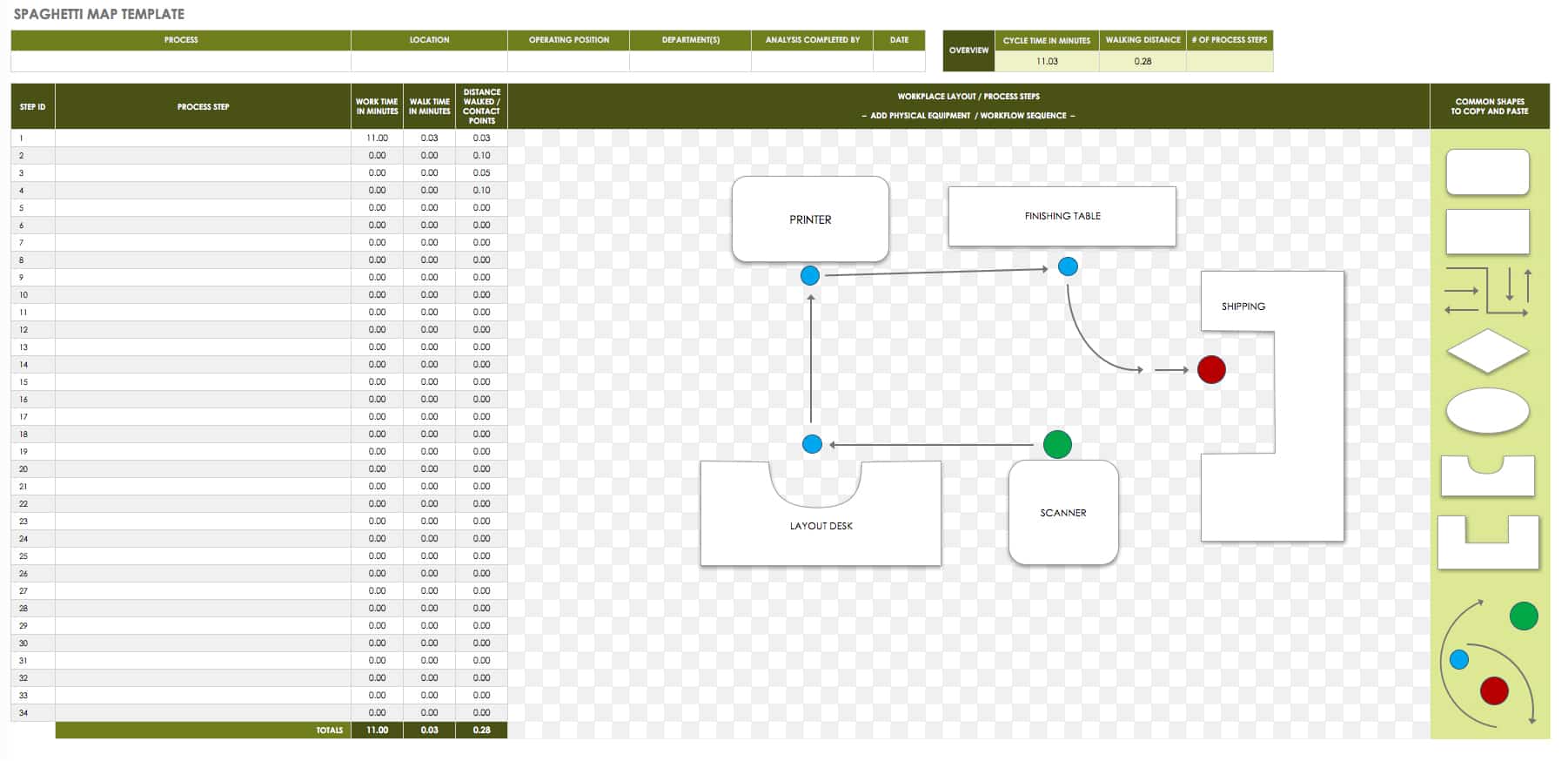
Download Spaghetti Map Template
Excel | PDF
Experts recommend creating a value stream map with pencil and paper and documenting all the process steps that your product goes through, from supplier to your organization and finally to the customer.
Ensure that the Value Stream Flows: The ultimate goal of value stream mapping is the preservation and optimization of flow — the rate and “evenness” with which items and information proceed through the value stream. This is the principle of JIT manufacturing in action: because excess, early, or unexpected inventory creates waste, synchronization is the key to optimizing flow. Identifying and eliminating work that adds no value (either directly or indirectly) can also improve the flow of a value stream. Employ a Pull Approach: Traditional manufacturing employed a push approach, where production targets are set based on an internally-determined schedule and production quota. This approach not very responsive to customer demand, and commonly led to production exceeding or failing to meet demand. In the first case, you would have to store the surplus product; in the second, you would have to increase the rate of production, possibly beyond optimum efficiency levels, to meet the demand. Either way, this approach creates a lot of unnecessary waste. By contrast, a pull approach allows customer demand to determine production, so that nothing is created unless a customer asks for it. Done correctly, this eliminates waste caused by inventory costs and overwork. A pull approach is, however, difficult to implement effectively because it relies on accurate, effective assessment of the market and the ability to vary production quickly and on demand. Delivery must be speedy to ensure that customer demand still exists by the time the end-product is ready. Finally, a pull approach also requires highly effective coordination of information throughout the value stream, so that everyone is aware of production requirements and inefficiencies don’t arise because of confusion and mismatched expectations. Pursue Continuous Improvement: At its heart, Lean management is an ongoing, incremental process. A waste-free system may be practically unattainable, but as a goal, it drives a need for constant improvement. The Japanese word Kaizen is often used to describe this practice in Lean. With Kaizen, the value stream is continually optimized, and defective processes are consistently improved or replaced in an effort to improve quality. Other key principles in Lean software development include amplifying learning, deciding as late as possible, delivering as fast as possible, and empowering the team.
Lean Thinkers Obsess About Waste
As we’ve discussed, eliminating waste is the central focus of Lean. Waste in manufacturing or construction is easy to visualize: unused resources, unnecessary effort, perhaps refuse or byproducts. For work that doesn’t involve a physical end-product, however, waste can be a little harder to visualize. What sort of waste would you imagine from, say, a software development project? As it turns out, the waste concept in Lean thinking stretches far beyond physical waste. Lean product development expert Ron Mascitelli describes waste as “anything the customer would not agree to pay for,” and Lean software developers Mary and Tom Poppendieck say waste is “anything that does not add customer value.” TPS and traditional manufacturing identify seven types of waste (or muda in Japanese). Though these waste types were created with physical end-product manufacturing in mind, they translate well to non-physical projects, too. Let’s look at the seven types of waste, and show how they can be interpreted outside of traditional manufacturing.
Seven Areas of Waste in Lean
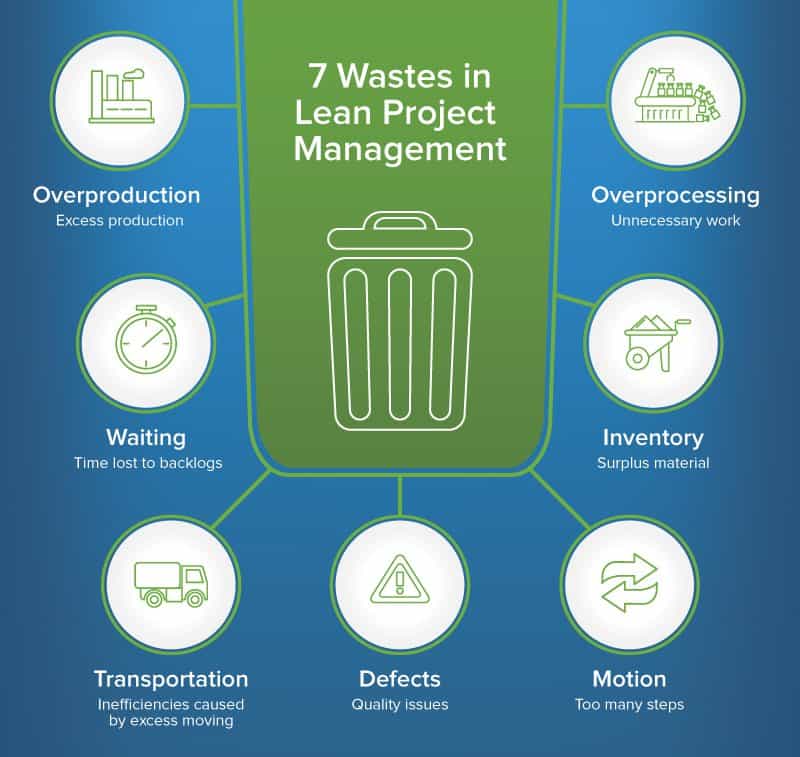
Overproduction: Used traditionally to refer to waste created by push manufacturing, this category covers surplus production and large inventories. Overproduction in software projects also refers to creating a product before establishing the demand for it. Overproduction may also refer to the mistake of providing functions, features, or services that the customer is not willing to pay for, which means that some of the work done on the project is unnecessary or redundant. Waiting: This term traditionally referred to the time between a product being ready to move to the next stage in a production cycle and the product actually being moved to the next stage. In manufacturing, waiting occurs because of bottlenecked processes; in soft project management you can extend that definition to include the time that information required to proceed to the next stage is unavailable. Transportation: This refers to the cost incurred and time spent physically moving a product from one place to another, especially as it is being produced. The potential costs of transportation extend beyond the time and money expended in the transportation itself, as transportation also raises the risks of damaging products. Inefficiency increases when production processes require goods to unnecessarily travel more around factories. Transportation waste is less of a problem in service projects, where communication is mostly digital and instantaneous. But inefficient paper trails and communication failures such as power outages or IT downtime are still problematic. Over-processing: In manufacturing, over-processing refers to doing work that is not needed. This could be painting areas that won’t be seen or tolerances that are tighter than required. This imposes costs related to labor, materials, and equipment wear. In service projects, over-processing takes the form of convoluted, redundant hierarchies and levels of approval, as well as the software development scenario of creating more iterations of a software product than actually needed to realize the value of the product. Inventory: In manufacturing, a push approach may result in excess inventory, which raises transportation-related waste and can consume usable space. Inventory can also prevent the identification of problems with the workflow. For service projects, inventory costs tend to be mitigated, but the excessive stockpiling of information and difficulty in retrieving information when needed are analogous. Motion: Motion-related wastes occur - in manufacturing, hard projects, and soft projects - when workers have to move too much to perform their tasks economically. Again, this is less of a problem with knowledge work, when you can quickly pull the required digital resources. Non-digital resources, however, can constitute a substantial proportion of resources used even in soft projects, and inaccessibility causes wasted motion. Defects: The problem of defects is similar for all types of work, and entails reworking and using more resources than should have been necessary. The difference lies in how defects originate. In manufacturing, defects are typically caused by faulty equipment or operator errors, while in knowledge work they stem from poor design or from inaccurate estimation. The Lean Six Sigma methodology also refers to an eighth waste : underutilized skills or brainpower. This type of waste is primarily associated with knowledge work and refers to the waste that occurs when not tapping into a worker’s full mental potential. This can occur when companies hire overqualified employees or place workers in positions where they can’t fully exercise their abilities.
How Lean Can Prevent Fatal Project Mistakes
Lean principles and the recognition of waste can help project managers avoid, mitigate, or control situations that might otherwise lead to project failure. Here’s a list of common project pitfalls that Lean thinking can help avoid: Failing to Establish Customer Value: Not understanding what a customer values in your project can cause you to misprice the project, and waste work and resources. When you understand the value your undertaking offers customers, you can more clearly establish project requirements, price the project according to what a customer is willing to pay, and revise work streams to meet this target price. Scope Creep: Scope creep occurs when the value of a project is increased (usually due to customer requests), but corresponding changes in budgeting and pricing don’t account for the increased value. You can avoid this problem by understanding and reevaluating value to the customer when scope changes occur, and ensuring that increased value is accompanied by a change in pricing. Failing to Define the Value Stream: Value stream mapping is an excellent way to see how project activities create value, and is vital for trimming activities that don’t create value for the project. If you do not map or define the value stream with an eye to optimizing it, non-value-creating activities may continue to strain the project budget and extend the project schedule. Lack of Stakeholder Commitment: In a perfect world, projects would always finish on time and never exceed planned cost. In reality, most projects suffer due to cost and schedule overruns, so having the stakeholder’s full backing is vital. A stakeholder who is not fully committed to the project may be less likely to extend support when a project needs to dip into its contingency reserves or request emergency funds, thus drastically exacerbating the waste creation problem. Learn more about securing and maintaining support from stakeholders in The Definitive Guide to Stakeholder Management . Lack of a Communication Plan: An effective communication plan streamlines the flow of information between a project’s stakeholders. Without effective, timely communication, projects run the risk of wasting time and resources on time-consuming approvals, delayed progress, and value mismatches.
Three Popular Lean Project Methodologies
Now that we understand the principles of Lean thinking, we can look at how three of the main Lean methodologies—the Deming Cycle, Six Sigma, and Kanban—approach project management. They all follow a disciplined approach to project management, stress optimization of the value stream, and map the value stream in its current state. After identifying inefficiencies and waste and making modifications, a map of the value stream’s future state lays out the reengineered, optimized value stream with an improved flow. The future state can be thought of as an interim stage between the value stream as it currently exists and a hypothetical, ideal value stream. As such, value stream mapping is an ongoing process, and new measures to improve the value stream are regularly designed and implemented. At a more granular level, each of the processes that constitute the value stream are made up of a sequence of steps; you use metrics to assess the performance of these sequences. Applying Lean management principles within value stream processes can improve performance on these metrics on a micro scale and reduce waste on a macro scale. Remember that, whichever methodology you use, successful Lean projects will all seek to continually improve flow through the value stream. To do this, they streamline the flow of information, examine the value stream and its constituent processes for redundancies, and aim to simplify and standardize to reduce waste. For development projects, they may adopt a lifecycle model that uses concurrent processing in an effort to mitigate waste caused by bottlenecks. A Lean project will also adopt a pull (rather than a push) approach. This means that the customer recognizes the demand for the project before the project gets underway, and the project is completed in response to this demand. Since Lean thinking is such an overarching concept, an organization that embraces Lean management principles will usually have been successful building a culture of Lean thinking among its employees. Moreover, Lean management allocates decision-making responsibilities throughout the company hierarchy to minimize waste caused by unnecessary lengthy approvals and bureaucracy. Often, this means trusting lower-level employees and empowering them to make decisions for which they are qualified, without engaging in a wasteful review-and-approval process.
The Deming Cycle: A Method for Ongoing Quality Improvement
The Deming Cycle, also known as A3 problem solving because it was traditionally done on sheets of A3 paper , takes its name from W. Edwards Deming, the management consultant who helped Japan rebuild their manufacturing capabilities after World War II. Deming, who is sometimes referred to as “the father of quality control,” created the Deming Cycle to facilitate the constant improvement of business processes. The Deming Cycle is also known as the PDCA Cycle or PDSA Cycle (for Plan, Do, Check or Study, and Act). Planning entails conceptualizing and designing a plan to improve a process. Doing is enacting the plan and testing its results using performance metrics. Checking or Studying involves determining whether the improvement plan was successful, and Acting is the permanent implementation of the plan to improve the business process. There’s some debate among quality gurus about whether PDCA and PDSA are the same thing, but generally any distinction is considered too minor for the average practitioner to worry about. The Deming Cycle methodology is geared towards addressing process-related problems with a single — or at least a primary — underlying cause. This cause is called the root cause, and the team in charge of improving the process will design one or more possible solutions to address this root cause. You can use this template to conduct your own root cause analysis.
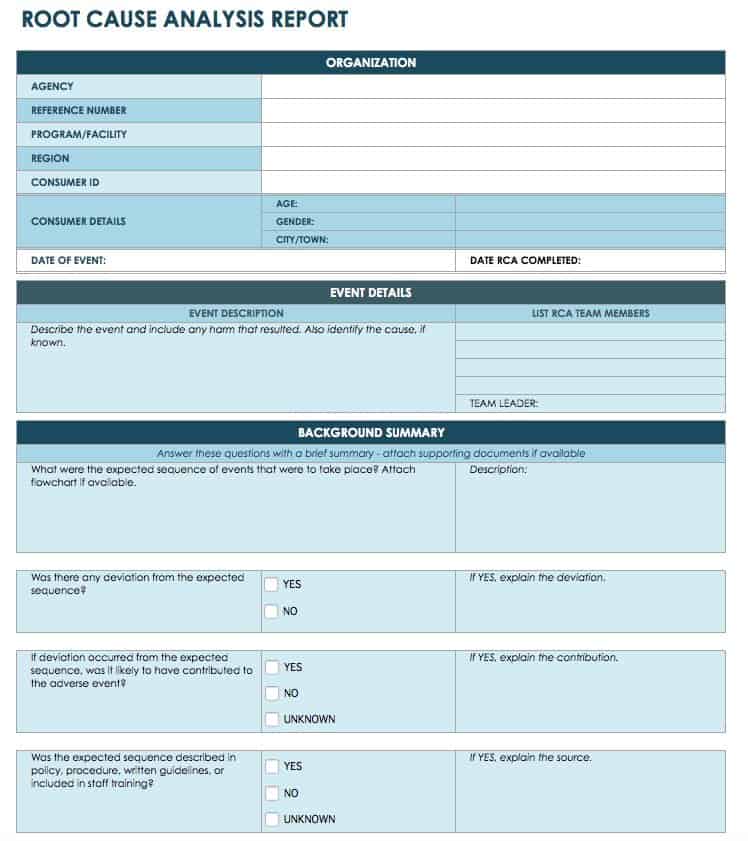
Download Root Cause Analysis Template
Excel | Word | PDF
Practitioners also identify the current situation, or current state of the process, to determine how to best address the root cause and to identify how to change the process to target the root cause. Once you identify and target the root cause, the team will prepare a problem statement that lays out what they are trying to achieve, and establishes the metric to measure the solutions. These solutions are evaluated during the Doing and Checking phases. After conducting a cost benefit analysis to determine the optimum solution, the team recommends a plan of action to the decision-maker. To conduct your own A3 analysis, use this report template.
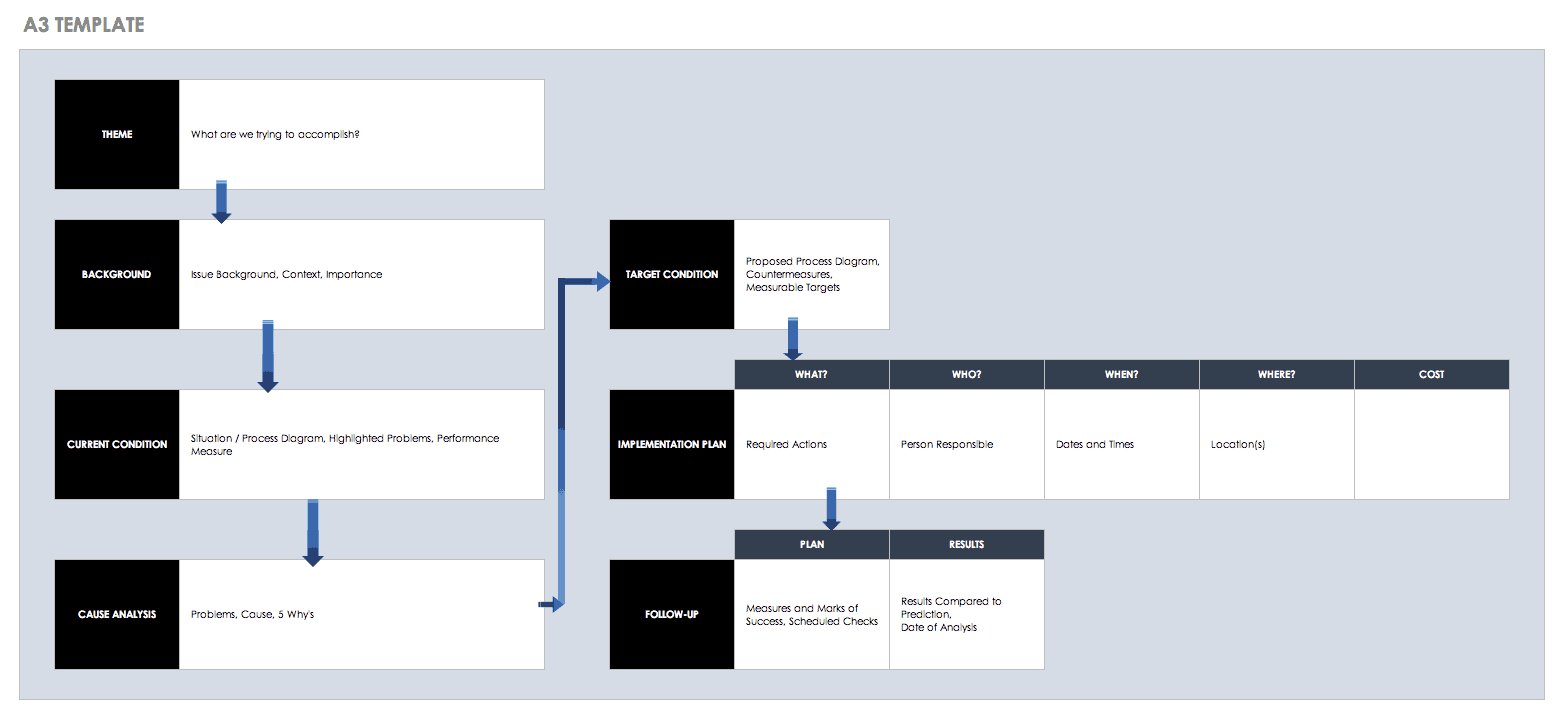
Download A3 Report Template
Excel | Word | PDF
The Deming Cycle: Project Example in Education
The American Society for Quality cites as a Deming Cycle project example the Pearl River NY school district , which uses the technique for curriculum and instruction design. The school district’s planning involves the analysis of student needs to identify gaps or areas for improvement in instruction. Doing is a two-step process that involves first building a curriculum that both adheres to state and national standards and to the students’ own needs, and then actually providing the instruction. Checking involves the use of school assessments to evaluate student performance with the new mode of instruction. Finally, Acting is the implementation of curricula and instructional methods that successfully serve the students’ needs. “Throughout the school year, if assessments show students are not learning as expected, mid-course corrections are made such as re-instruction, changing teaching methods and more direct teacher mentoring. Assessment data become input for the next step in the cycle,” the case study notes.
Six Sigma: Data-Driven Method for Eliminating Defects
Six Sigma is a process improvement methodology that focuses on eliminating defects and minimizing variation in process outcome. It’s heavily data-driven. The name Six Sigma is a statistical reference to having six standard deviations fall between the process mean and the nearest specification limit, which effectively results in an error rate of 3.4 defects per million products or process outcomes. As such, Six Sigma’s primary goal is optimizing the consistency and precision of a process. You can read a complete guide to Six Sigma here . Six Sigma was developed by engineers at Motorola in the mid-1980s, and Motorola later trademarked the name. The technique became a cornerstone of General Electric CEO Jack Welch’s approach in the 1990s. It’s important to note that while Six Sigma and Lean are not the same, the management philosophy and the methodology complement each other very well. Lean alters processes to remove waste, and Six Sigma alters processes to improve the quality and consistency of output. As such, they both play important roles in process reengineering. The Six Sigma methodology pursues process improvement through Six Sigma improvement projects, which adopt one of the Sig Sigma sub-methodologies. We’ll discuss two of these sub-methodologies: DMAIC and DMEDI. DMAIC: This acronym (Define, Measure, Analyze, Improve, Control) is used in Six Sigma projects that aim to revamp or improve an existing business process. The define phase involves defining the scope of the problem to be examined, establishing customer requirements, and setting goals for the project. Measurement is the evaluation of the process’s current state through data collection. Analysis is the process of examining the data collected to identify the root cause. Improvement involves the use of process-improvement techniques to optimize the process, thus moving it to its future state. Finally, control involves monitoring the new, future-state process to ensure quality of output. You may repeat DMAIC until your reach the desired level of quality consistency.
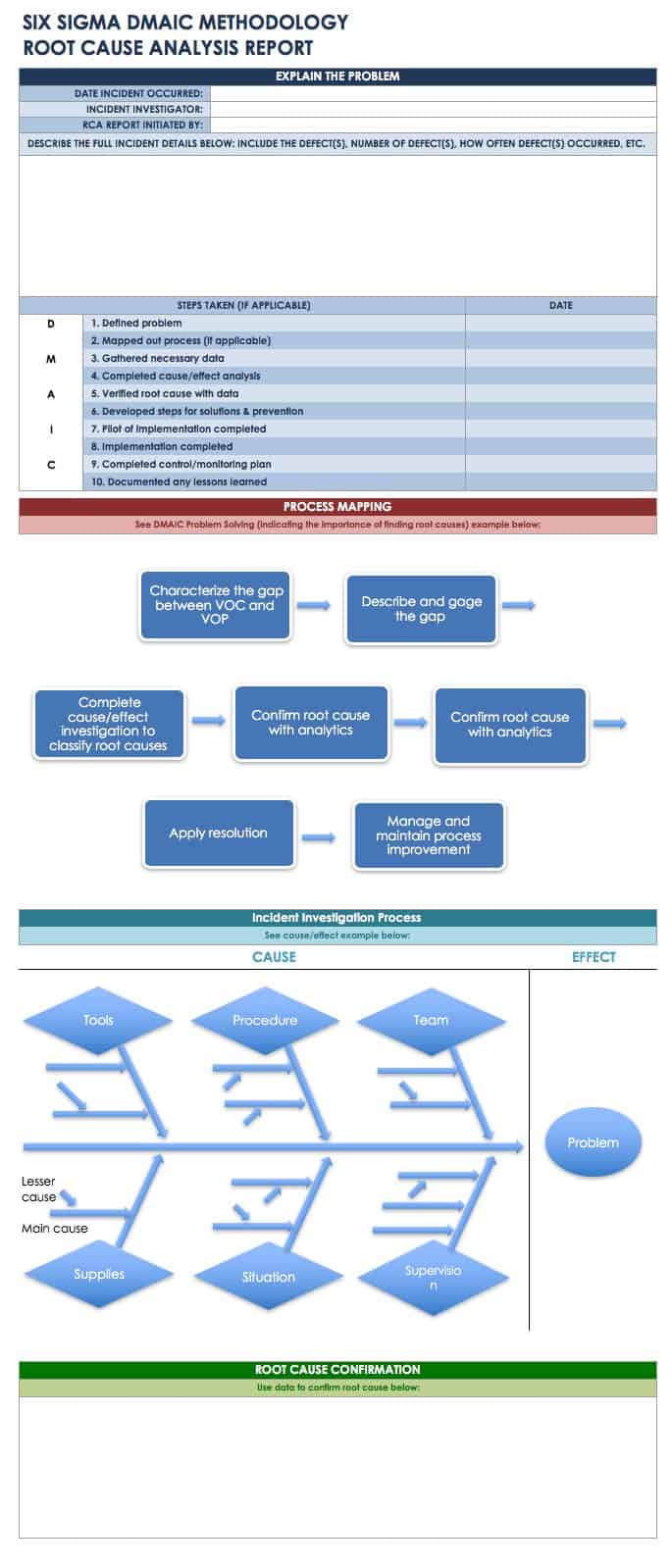
Download Six Sigma DMAIC Root Cause Analysis Template
Excel | Word | PDF
DMEDI: This acronym for (Define, Measure, Explore, Develop, Implement) is used in Six Sigma projects that aim to design a new process. It’s less data-driven and more creative than DMAIC. The define phase in DMEDI is similar to that in DMAIC: defining the process to be designed and the goals for the new process. Measurement is the identification of customers and their requirements. Exploration is the process of examining alternative process designs to evaluate which will best serve customer requirements. Development is the actual production of the design that is considered optimum for meeting consumer requirements. And lastly, implementation involves pilot-testing the new process to ensure that its output does indeed meet customer requirements. Deciding whether to use DMAIC or DMEDI really depends on evaluating the state of a process, if it exists at all. Conventional thinking says that DMAIC is used to improve an existing process, and DMEDI to establish a new process. In some cases, however, an existing process might be so full of problems and root causes that it’s easier to design a new process than to try and improve the existing one. If this is the case, DMEDI may be a better choice than DMAIC. Six Sigma uses a martial-art-style belt system to indicate levels of certification. The belts, in order of increasing expertise, are: White Belt, Yellow Belt, Green Belt, Black Belt, and Master Black Belt. Black Belts and Master Black Belts lead Six Sigma problem-solving projects and train others seeking Six Sigma certification . Learn more on Six Sigma certification here.
Lean Six Sigma: Combining Focuses on Waste, Quality
Lean Six Sigma is a process-improvement methodology that marries the waste-reduction principles of Lean with the quality-improvement efforts of Six Sigma. Performance management practitioner Arun Hariharan explains that you can classify Lean Six Sigma projects into three broad categories:
- Quality improvement projects rely primarily on Six Sigma methods to improve the quality of a process output.
- Revenue enhancing projects rely equally on Six Sigma and Lean to improve quality, reduce waste (thus increasing speed), and thus to increase company revenues.
- Cost savings projects rely primarily on Lean principles to cut waste from a project, making it faster, more efficient, and thus cheaper.
Six Sigma: Project Example from Medical Manufacturing
Perhaps the most iconic Six Sigma project is one conducted at Motorola in the late 1980s, when Motorola engineers who wanted increased granularity in quality measurement switched from measuring defects per thousand opportunities to defects per million opportunities. This change in how to discuss and perceive quality would eventually lead to more than $16 billion in savings for the company via increased precision and conformance to quality requirements. Since then, Six Sigma and Lean Six Sigma methods have been implemented at thousands of organizations in the U.S., including Ford, General Electric, and the U.S. Army. Another example of the benefits of Six Sigma is Orchid, a manufacturer of artificial joints used in hip and knee replacements among other products. Their process involves lost wax casting of molds that are used to form the artificial joint from cobalt. The company found that six percent of its molds would crack, wasting the cobalt. A Six Sigma team including a plant receptionist began investigating the issue around 2010. They identified 200 variables in the manufacturing process that they speculated could contribute to the cracked molds. The receptionist noticed that there were two kinds of wax employed in the casting, virgin wax for the parts that would be in contact with surfaces implanted in the patient, and reclaimed wax for non-contact parts. Testing by the Six Sigma team found that the waxes melted at different temperatures, which could account for the cracking. They sought to verify this with 100 castings using only virgin wax. In that test, not a single mold cracked. Sixteen years earlier, the company had started using the reclaimed wax to save 60 cents a pound over virgin wax, but the decision was causing waste of cobalt that cost $7.50 to $15 a pound. The move to all-virgin wax, a variable identified through Six Sigma methods, saved Orchid an estimated $2.1 million a year.
Kanban: Limit Work In Progress to Speed Completion
Kanban is another Lean method that originated at Toyota. This methodology focuses on eliminating backlogs of work in progress and keeping work flowing smoothly. To read how both manufacturing and software companies use Kanban, check out this reference . In an ideal factory, work would proceed at a consistent pace — sometimes termed continuous flow — and would never be bottlenecked. In reality, however, some processes are slower than others, and if these processes are downstream of faster processes, they cause backlogs. Backlogs occupy space and cost money to store, and they can conceal problems such as quality defects. Read more about Kanban in inventory management here . Toyota fixed this problem by implementing a system of visual cues — cards called Kanban cards — to indicate when a process was available to take on new work. As such, the pace of work is set by the slowest link in the production chain, which would “pull” production by using card signals to indicate when it was available to process work. As discussed earlier, the “pull” approach limits backlogging and controls bottlenecking to decrease waste. Kanban also limits the number of items being processed at any one time. The classic Kanban system is a board divided up into sections, with a number of movable cards. Each section depicts a particular process, and individual cards represent work items that move through these processes. Visual cues makes it easy to spot inefficiencies and backlogs, so Kanban can be a great way to identify processes for improvement. Given how easy and effective it is to use, Kanban is widely adopted by organizations and teams of all sizes that run multi-process production lines. Kanban is also ideal for knowledge work such as content publishing, which involves multiple processes (writing, editing, proofreading, and typesetting and printing). By using cards to symbolize individual pieces of content, you can track progress through the editorial and design chain, and allocate human resources to backlogs when they develop. You display the cards are on a Kanban board - this was traditionally a physical bulletin board but today is often created online.
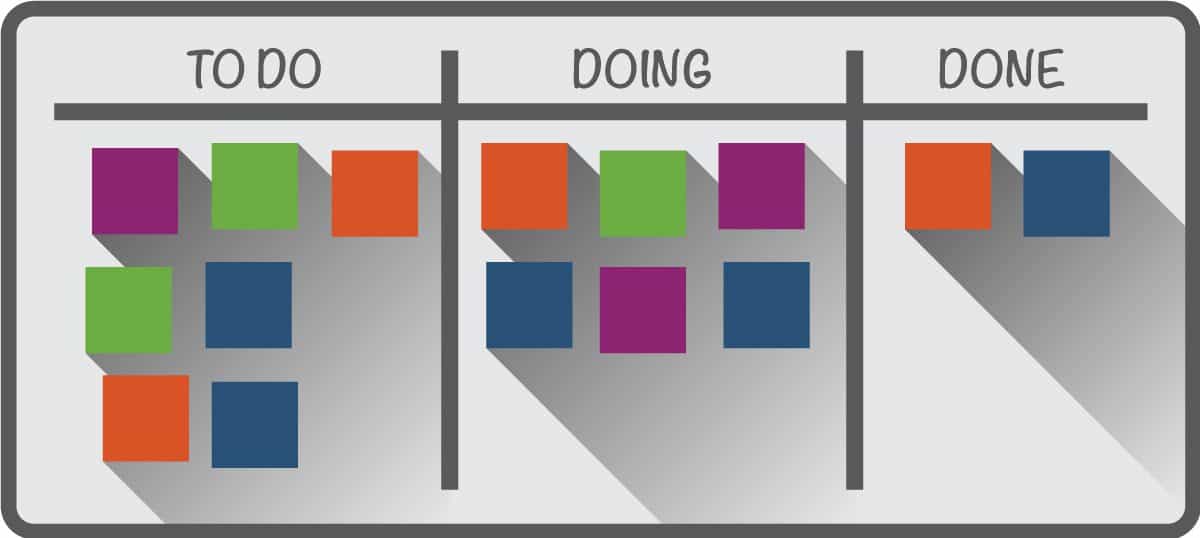
Kanban has become popular in services and knowledge work. When applied to these projects, the main principles are:
- Visualize work
- Limit work in progress
- Teams pull work when they have completed existing tasks
- No sprints (time-based work intervals)
Kanban Project Example: Website Reaps Efficiencies
An impressive example of Kanban’s success comes from Moneysupermarket.com, a top U.K. comparison-shopping website that serves more than 120 million users a year. The development team was suffering from high demand, constantly shifting priorities, poor morale, and low throughput. The use of the Kanban board highlighted obvious bottlenecks and blockers, and made it clear where the team needed to focus to address problems. After implementing Kanban, the team’s lead time dropped from 120 days to 25 days, and throughput soared. Developers cleared the backlog of 469 jobs in five months.
Implementing Lean: Tips for Making Lean Work for You
When implementing Lean, the most important thing to remember is that it is best employed as a long-term philosophy, rather than a quick fix to waste-related problems. Waste reduction is an ongoing process, and developing a philosophy of Lean thinking and consistent performance measurement ensures greater, sustained benefits over time. It also makes the application of Lean principles easier, as workers learn to recognize waste through practice. One of the ultimate goals of Lean is creating and maintaining a continuous flow of processes — where work moves through sub-processes without stopping and creating waste. To do this, organizations will implement “pull” approaches, thus drastically reducing the costs of inventory, storage, and maintenance by producing end-products on demand. In the long term, this “pull” approach leads to a more even distribution of work, which can mitigate the problems associated with overwork — for both machines and people. Of course, Lean also recognizes that flow may be interrupted not only by production processes, but also by the flow of information. Fostering a culture of strong, rapid communication is vital to the success of Lean management. Implementing tools that facilitate communication, such as Kanban, is often a necessary supplement to streamlining and improving workflows. To incorporate principles of Lean management, start with small, well-defined projects delivered to short deadlines. This is helpful for a number of reasons. For one, it teaches people to recognize waste and decide what to do about it. Additionally, it has the potential to provide quick gains through waste reduction. Since these tend to be more immediate for short projects, this can do wonders for project managers trying to develop a culture of Lean thinking in a project team. Project managers should also champion the core Lean principle of continuous improvement (Kaizen) with regard to their people and teams. Encourage continued training and learning, and project managers can obtain certifications in Lean project management, such as those offered by Villanova University and the Management and Strategy Institute .
The Best Tools for Lean Project Managers
Lean project managers have developed some tools to aid in project management and organizational transformation. Some of these tools are conceptual or process frameworks, while others exist as software and systems. Value Stream Mapping: As we’ve discussed, value stream mapping plots the flow of materials and information involved in the creation of a product. Use a value stream map to analyze the current state of a value stream and to design improved future states that remove waste and create value according to customer demands. Value stream mapping was traditionally done on paper, but online tools are now available, too. Work Cells: In manufacturing, a work cell is a strategic arrangement of resources designed to improve the flow of a process and decrease waste. You may create work cell arrangements using either physical equipment or human resources, and often a combination of both. A cross-functional team is an example of a work cell based primarily on human resources, while manufacturing workspaces are an example of work cells centered on physical equipment. One-piece Flow: One-piece flow is the practice of moving work items through a work cell one piece at a time (instead of in batches), and is done mainly to decrease work in progress. Processing one work item at a time is quicker than having each worker produce batches of work before moving them to the next step (as batches take longer than single items to process, and work cannot move downstream until the entire batch is complete). Kaizen: Named for a Japanese word that roughly translates to “good change,” Kaizen is an approach to work that emphasizes incremental improvements in processes and work streams. The end goals of Kaizen are improved efficiency and higher quality. The concept encourages an organization to welcome small, easily implemented improvements that, taken together, provide major benefits in the long term. A popular way of implementing Kaizen is to start with a Kaizen Event, a short-term project (around one week) with a single, specific improvement goal. A common plan for a Kaizen Event (also sometimes called a Kaizen Blitz) assigns a function for each day such as current state documentation, current state evaluation, characterizing future state, implementing future state, and operationalizing future state. To run your own Kaizen Event, use this template to keep track of your work.
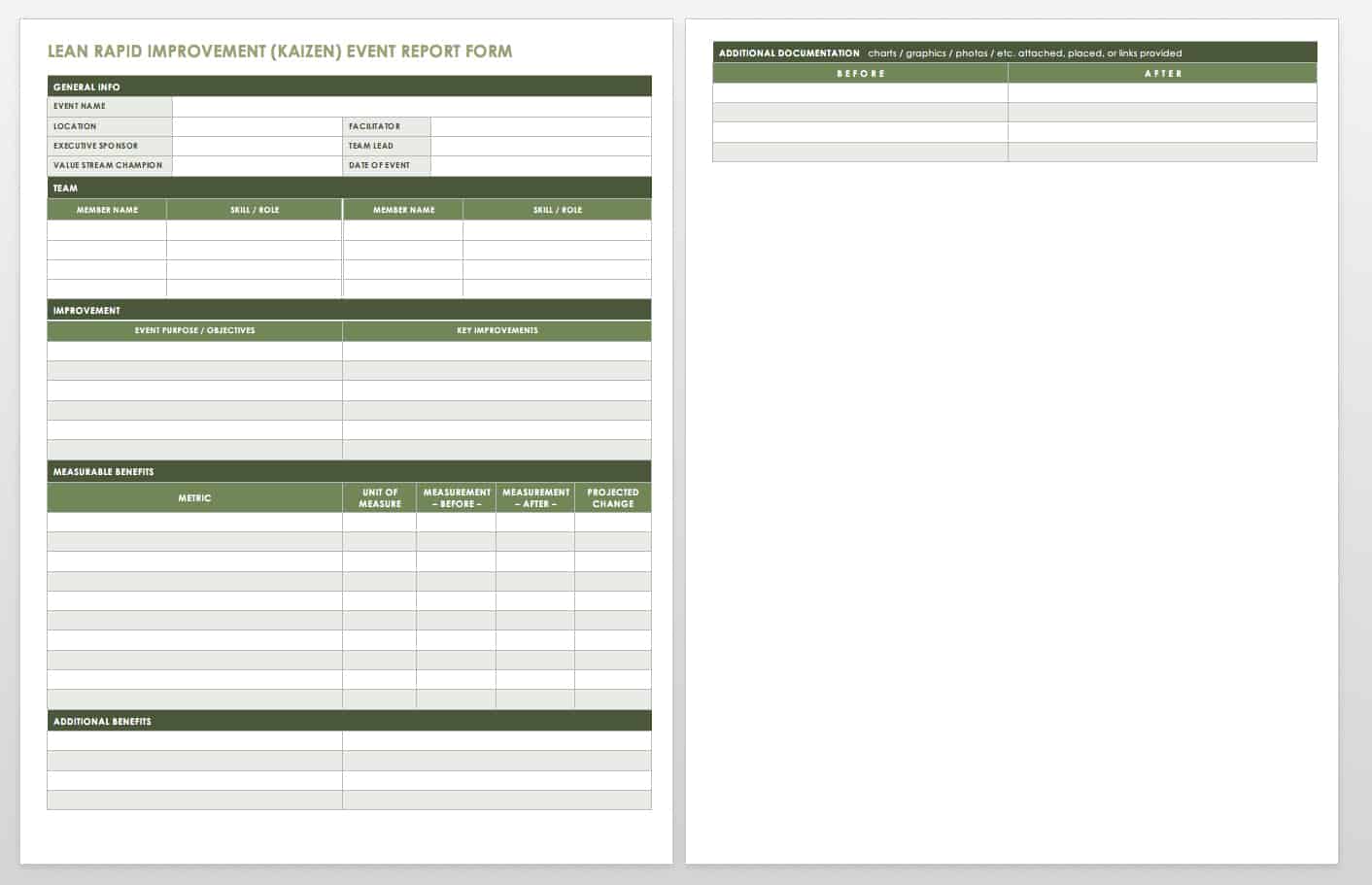
Download Lean Rapid Improvement (Kaizen) Event Results Template
Word | PDF
5S: A workspace organization method that organizes work-related resources in a manner that facilitates efficient, effective work. The name 5S comes from five Japanese words which, translated to English, mean sort, set in order, shine, standardize, and sustain . 5S is commonly used in Lean Six Sigma as a methodology to organize workplaces and use visual cues to achieve more consistent results. The steps involved are remove items not needed for current operations, label and arrange items so they are easy to use, keep everything tidy every day, standardize a system for keeping things in order, and avoid backsliding. While this system started in factories, it is equally relevant to offices. Try this 5S checklist in your workplace.
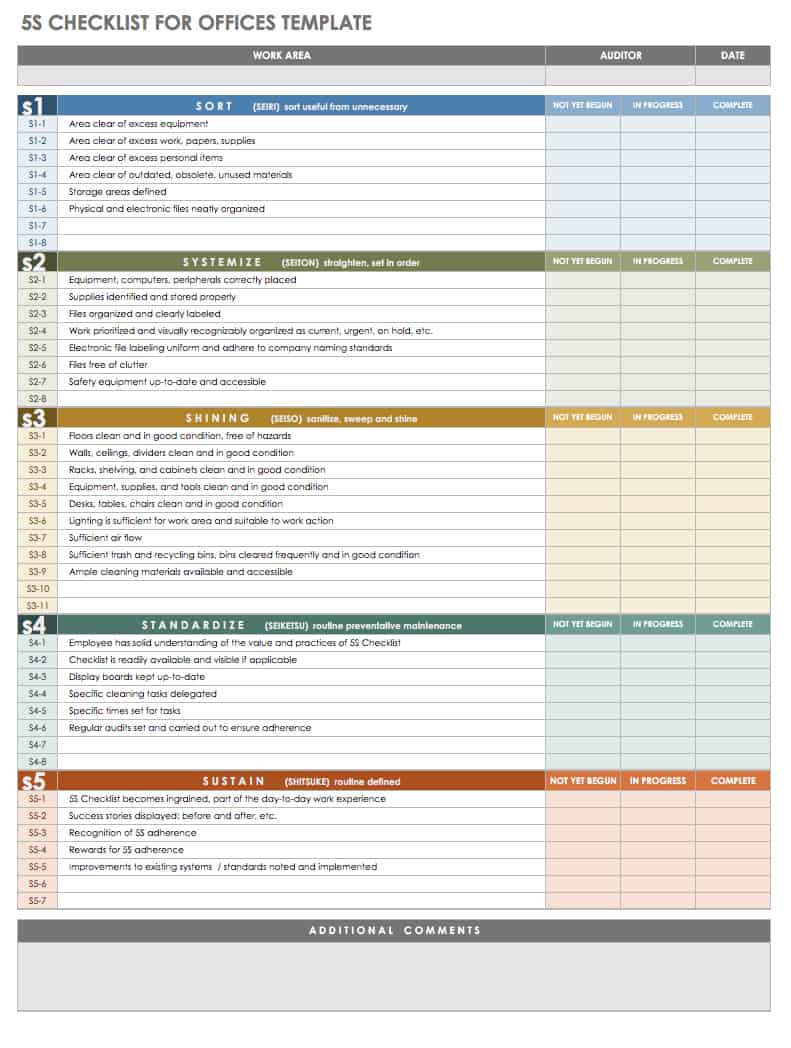
Download 5S Checklist for Offices Template
Excel | Word | PDF
Poka-yoke: A mechanism for error- or mistake-proofing. It helps human operators identify, prevent, or correct mistakes as they occur. The idea behind Poka-yoke is accounting for defects as they occur, minimizing waste that would otherwise be caused if defects proceeded down the production chain. Typically, Poka-yoke are divided among control and warning mechanisms. One example of a control Poka-yoke are electrical connectors designed so that they will only fit together the correct way. In a broader sense, Poka-yoke can be any technique that safety-proofs a process so it can’t be screwed up. Gemba Walk: The Gemba walk is an application of the principle of observing work as it occurs, where it occurs. It is a supplement to the Kaizen process, and is based on the idea that work processes are best observed, and thus best improved, in real time and in the actual work environment. Sometimes described as “management by walking around,” Gemba is more than a manager ambling around the office and overseeing work. In Lean, the purpose of Gemba is to observe, engage, and improve, and should occur where the most critical activity happens (the production line in manufacturing, the classroom in education, etc.). Your interactions are designed to engage the people and processes in Kaizen or continuous, incremental improvement. Obeya Room: The Obeya room, or “war room,” is a large physical space used during the development of a new product or process to facilitate interdepartmental thinking and communication. All individuals involved in the development process meet in the Obeya room to communicate and make decisions about a specific project. The Obeya room is typically furnished to facilitate discussion and problem solving, and speed up decision making. Visual Cues: The basic premise of Kanban is that it’s easier to understand and run processes visually than solely by words or numbers. As such, the use of Kanban-style visual cues (sticky notes, colored golf balls, visual control charts, or software tools that represent work items visually) is a proven way of simplifying and speeding up communication, as well as of facilitating understanding of a process. Documenting Metrics and Progress: Since Lean thinking is ultimately concerned with decreasing waste and improving flow (and typically seeks to do so incrementally), it’s vital to establish metrics that measure flow, and to consistently record performance on these metrics. You can assess flow, for example, using metrics such as work in progress, lead time, queue time, and throughput. It’s best to measure these metrics are using software tools, which can quickly determine and visualize performance via graphs or summary statistics.
How Lean Relates to Agile Methods
In software development, there’s a tendency to conflate the principles of Lean thinking with the methodologies of the Agile manifesto. So exactly how similar are they? Agile methodologies are a set of iterative development approaches designed specifically to meet ever-changing customer requirements in software development projects. The signature characteristic of an Agile project is its flexible scope, meaning that Agile methodologies are designed to easily accept and implement changes in requirements. Agile software development consists of a series of iterations, and Agile software development teams target incremental improvements in each iteration. There are some similarities between Agile and Lean project management. Both prioritize customer satisfaction - Agile through extensive customer feedback and iterations and Lean by identifying value through the eyes of the customer. Both also focus on incremental improvement, rather than big, one-time fixes. Lean and Agile project management are similar in other aspects, too:
- Adopting a culture of blame-free employee involvement that ensures buy-in to the Lean philosophy and contributes to efficiency for Agile methodologies
- The role for a strong facilitator or project leader to ensure the project stays on track and effectively applies the principles of Lean or Agile
- Elimination of waste or redundant work, and the replacement or re-engineering of inefficient processes
- The practice of pipelining projects to ensure ongoing project delivery
In other fundamental ways, however, Lean is quite different from Agile:
- Lean is an extensive, far-reaching business philosophy that is designed to improve the efficiency of processes while eliminating waste. It results in process improvements that last for long periods and that will benefit future projects. By contrast, Agile is simply a method to ensure that a customer’s requirements for a discrete project are met quickly and efficiently.
- Lean principles work best when applied throughout an organization, encouraging overall efficiency and improving entire systems of processes. Agile, by contrast, targets good, quick decision making within development projects, and it is not applied outside of project work.
Lean Management across Industries
The core principles of Lean thinking can benefit many industries and types of projects. Here are a few examples of Lean management in action. Lean Brings Greater Efficiency in Healthcare As Daniel T. Jones, one of the authors of The Machine that Changed the World and Lean Thinking , notes, the application of Lean management principles in healthcare can “deliver better quality (and safety) and a better patient experience (less queues and rework) while at the same time making better use of existing resources (to treat more patients) and improving the work experience of staff (less frustration and stress).” This, he says, is vital at a time when healthcare systems around the world face increasing stress. Hospitals are an extremely challenging but rewarding environment for Lean. They’re a distinctively complex set of interconnected processes, ranging from admissions to patient care to managing expensive, delicate facilities and coordinating medical supplies. Consistently cutting waste thus leads, in the long-term, to more cost- and time-efficient operations overall, and generally a more pleasant experience for patients. This white paper by the Institute for Healthcare Improvement details the success of Lean management at the Virginia Mason Medical Center in Seattle, Washington. By eliminating waste, Virginia Mason increased their program capacity and saved millions of dollars on expanded facilities that were no longer necessary. They also managed to reduce the number of full-time equivalents despite a no-layoff policy, due to improved processes that increased productivity and thus reduced the need to replace retired staff. The center also saw remarkable decreases in setup and lead times, floor space used, and distances traveled. Financial Services: Fewer Errors, Faster Processing The financial sector was, in general, slow to adopt principles of Lean management. However, the 2008 economic crisis drove home the importance of cost cutting simply so financial institutions could survive. As such, increasing numbers of financial institutions are turning to Lean management and discovering quite serious efficiency and waste problems in the process. Since financial institutions use customer service to differentiate themselves from competitors, Lean thinkings focus on value in the eyes of the customer has proved valuable. Banks have focused on cutting times for customer services. They’re also able to price products more attractively by cutting non-value-adding services. On the back end, banks see the expected improvements in efficiency and running costs, as well as decreased processing times for operations that shouldn’t take nearly as long to complete. By using Lean, banks often see 15 to 25 improvements in efficiency, Boston Consulting Group has found. One bank was able to process transactions 30 percent more efficiently while improving customer satisfaction with Lean, and a North American asset manager made product pricing 12 to 20 percent more efficient. According to McKinsey , a global investment bank reduced inaccuracies by 50 percent, and improved timeliness and productivity by 40 percent each. Retailer Gets the Hottest Trends in Shoppers’ Hands with Lean Lean principles help retailers meet the perennial challenge of inventory management. Traditionally, retail outlets have found it difficult to keep shelves stocked with items that customers want, and lose out on potential sales when they can’t do this. The solution to this challenge is a Just in Time approach similar to that used in Lean manufacturing. This means optimizing, coordinating, and scheduling transport and handling, and cutting inventory costs. At the customer-facing end, Lean management can improve the shopping experience by reducing wait times, freeing up more staff to assist customers, and ensuring that customers can find what they want. And, of course, the lower costs brought by increased efficiency may translate to more attractive pricing, which is often the bottom line for retail customers. Fast-fashion retailer Zara used Lean thinking to become one of the most lucrative retailers in the business. Among Zara’s Lean-inspired practices, JIT manufacturing allows for low inventory stocks and rapid updating of product lines, delaying commitment to particular designs until customer design preference is established, using Agile methods to quickly design fashion items according to customer preference, and the use of Kanban and One Piece Flow to quickly and accurately meet customer demand. Lean Tools Help Educators Boost Academic Achievement Adoption of Lean thinking was slow in the public education sector, but there’s now an increasing appreciation of what Lean principles can bring to education.
Perhaps the most fascinating application of Lean principles in education concerns education’s core function: helping students to learn. Pedagogical debates rage over the most effective ways to do this, which means that a systematic, Lean-inspired approach to identifying less effective pedagogical techniques — and recognizing the more effective ones — can help standardize the best teaching practices. Lean thinking could help close disparities in education and benefit students everywhere. The Lean Enterprise Institute reports on the success of Lean thinking in improving academic achievement at public schools in Columbus, Ohio. Using Lean tools such as process mapping and value stream mapping, the schools boosted academic achievement by reducing the time between testing and reviewing test materials to ensure that students learned and reinforced concepts more effectively. School principals adopted a more standardized approach to recording and sharing classroom observations, spotting macro trends in the process. Application of the 5S workspace organization system helped streamline processes at principals’ and secretaries’ offices. Lean Construction Helps Sick Infants Go Home Faster The Lean Construction Institute (LCI) sees Lean delivery as a way of responding to customer and supply chain dissatisfaction with the building industry. The LCI cites decreased productivity and efficiency in the construction industry as a driver towards Lean approaches, and uses its trademarked Last Planner System to reduce workflow variability so projects are more predictable and coordination is simpler. Lean construction, perhaps the signature application of Lean thinking in project management, focuses on core Lean principles of defining customer value, maximizing value while minimizing waste, adopting a “pull” approach, seeking continuous flow, and empowering project participants with information and decentralized decision-making authority. As an example of Lean construction principles in action, at the Ambulatory Surgery & Critical Care Tower at Akron Children’s Hospital in Akron, Ohio, a variety of stakeholders including builders, architects, doctors, nurses, and patients and their families participated in the design process. This enabled project owners to gauge value from the perspectives of multiple “customers.” Realistic simulations of the facilities based on these designs were repeatedly tested and then redesigned based on feedback. For example, the Akron Critical Care Tower purposely built private rooms for new mothers and their infants based on evidence that critically ill newborns become well enough to go home faster. In discussing the most effective and efficient ways to locate and design facilities, to store equipment and supplies, and to house patients while meeting target-cost goals, designers reduced baseline square footage by up to 20 percent on each floor.
Why Smartsheet Is a Useful Tool for Lean Project Management
From simple task management and project planning to complex resource and portfolio management, Smartsheet helps you improve collaboration and increase work velocity -- empowering you to get more done.
The Smartsheet platform makes it easy to plan, capture, manage, and report on work from anywhere, helping your team be more effective and get more done. Report on key metrics and get real-time visibility into work as it happens with roll-up reports, dashboards, and automated workflows built to keep your team connected and informed.
When teams have clarity into the work getting done, there’s no telling how much more they can accomplish in the same amount of time. Try Smartsheet for free, today.
Discover a better way to streamline workflows and eliminate silos for good.
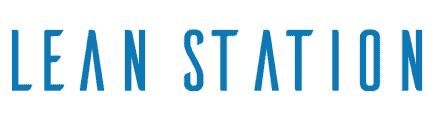
CASE STUDIES
We come recommended by the industry experts.
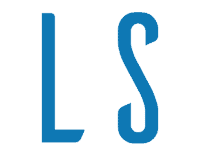
Recovering with minimum losses
A successful story of project recovery through Integrated Lean Project Delivery (ILPD) & collective team efforts.
SIMILAR CASE STUDIES
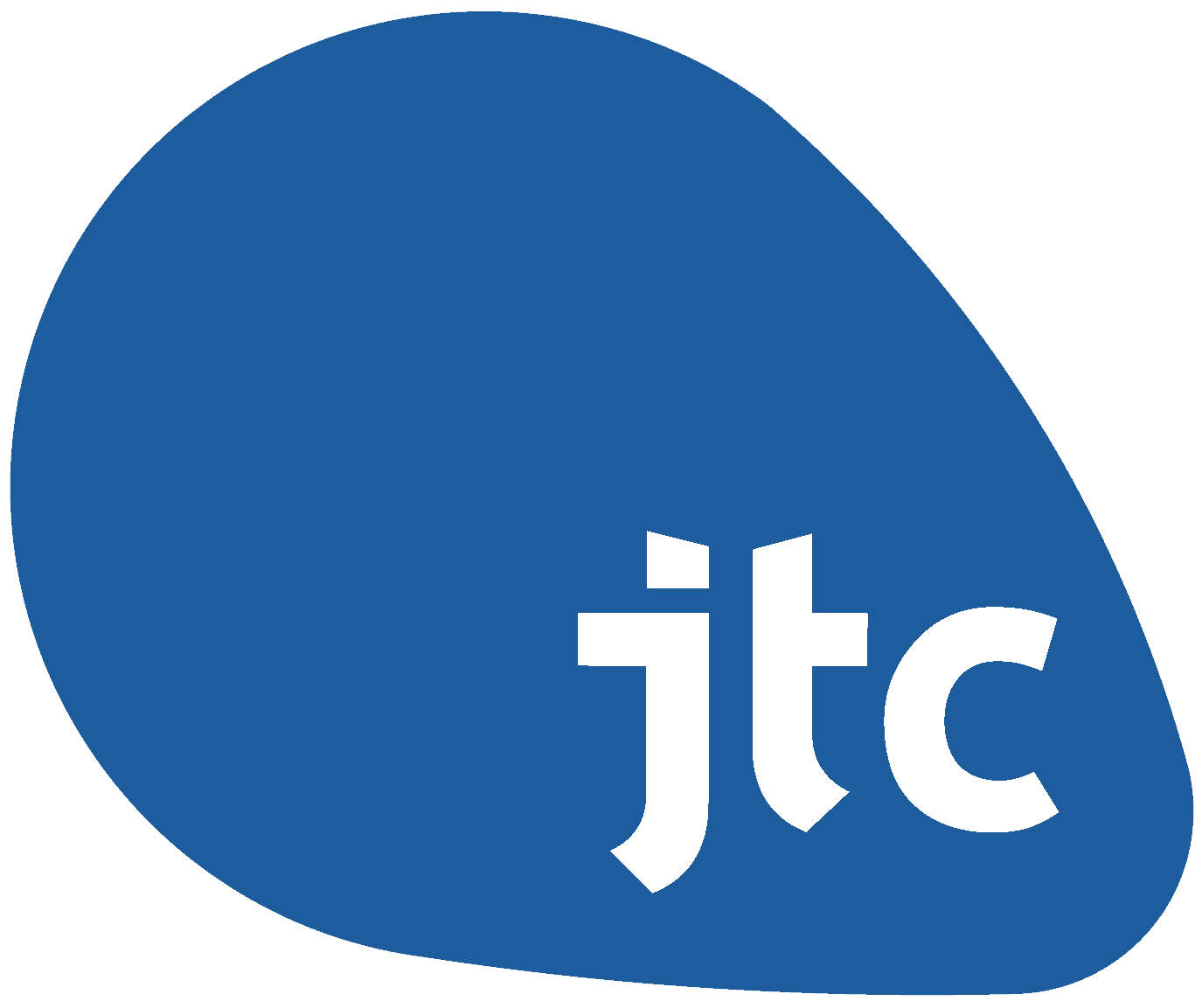
JTC CORPORATION
Achieve Lean execellence by implementing Lean PlanDo® across all your developments.
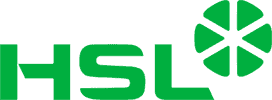
HSL CONSTRUCTOR PTE LTD
Achieve smooth and on-time delivery of all your projects by choosing Lean PlanDo as your all-in-one project management tool.
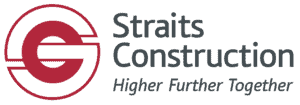
STRAITS CONSTRUCTION
Remain relevant while the construction industry is rapidly changing by utilizing Lean PlanDo in your projects to constantly refine your capabilities and while achieving digitization in all your processes.
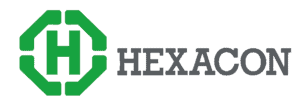
HEXACON CONSTRUCTION PTE LTD
Practice collaborative planning and commitment by adopting Lean PlanDo as a management philosophy to drive the forward planning mindset all the way from the top to the bottom across your team.
Piloting Lean PlanDo
Adopt a Lean mindset and scale up to a Lean enterprise by kickstarting a pilot.

Toh Hong Seong General Manager P-One (S)Ptd Ltd
"Lean PlanDo was easy to use and useful to track project issues ahead of time. It helped in tracking and reporting project progress and in improvement.”
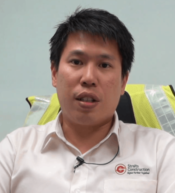
Han Sen Goh Project Manager Straits Construction
"Lean PlanDo helps in planning better by identifying the constraints and crucial dates. Plans are more reliable and helps in reacting to challenges proactively."
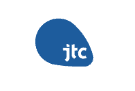
Wanna know more about what we do ?
(267) 808-6227
Case Study: Lean Project Management
This case study focuses on the effectiveness of using lean project management to evaluate, define, implement and sustain consistent operational efficiency. A small, innovative manufacturing company was struggling with a lack of clear communication for the two shifts of their production. In most cases, the company made changes on the first shift that were not being followed by the second shift. The changes and instructions on how best to implement them were not known by the second shift personnel due to this lack of communication and inclusion of the second shift in the decision making process.
Prosit was brought in to address this problem and help the company develop a standard process for any future changes. The evaluation process uncovered several issues that needed attention. One example was only the first shift had a dedicated forklift driver assigned. The second shift operators, not having that dedicated resource, had to stop production and get the forklift themselves to move material to where it was needed. That inefficiency caused the company production and cost issues.
To solve the problems, multiple lean project management sessions were run for small groups of first shift personnel over a period of two days. The goal was to get their input on what changes could be made and create a definitive “wish list” of improvements. With that model in place, the exact same thing was done for the second shift personnel. Prosit managed both shifts; gathering the input, defining scope and documenting gaps. In the end, most of the issues stemmed from the lack of personnel on the second shift compared to the first shift.
Improvements implemented for both shifts included the new communication protocol for identifying and executing on improvements, a new protocol for shift changes and an active hiring process to staff up the second shift and establish more consistency and efficiency in the daily production cycle. Morale improved also in the second shift since they now felt fully included and listened to within the company. The management team were pleased with the recommended improvements and Prosit’s ability and willingness to integrate, improve and standardize the two shifts.
Please contact us for assistance with lean project management or any other lean service. We can help your company succeed!
EJ Lydon has extensive experience in Operations and Manufacturing management. He now passionately provides Advanced Process and Strategic consulting services to small to medium sized companies, focusing on Lean Manufacturing methodologies with roots in the Toyota Production System.
Privacy Policy | Sitemap
What Is Lean Project Management: The Complete Guide
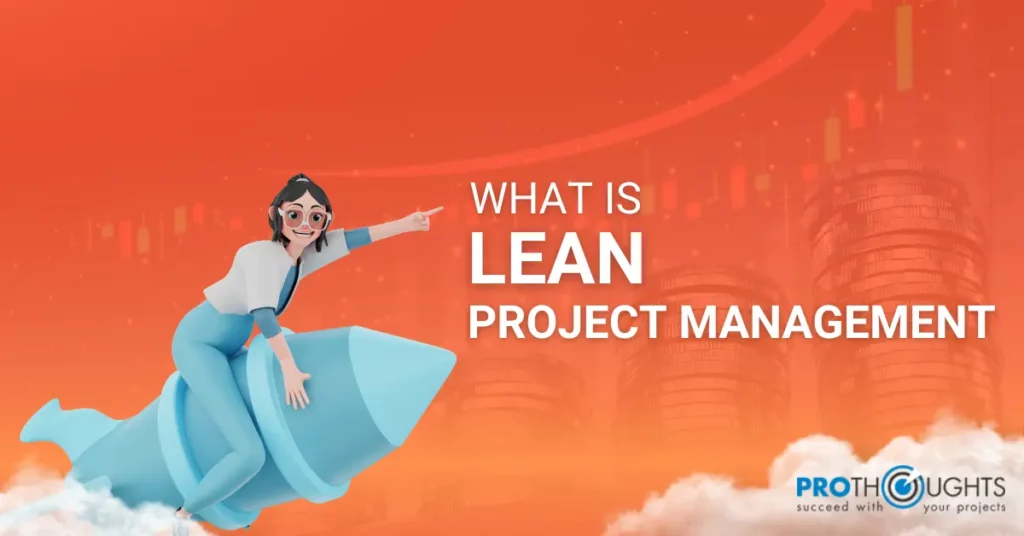
Everything demands speed and maximized efficiency today. Organizations strive to optimize their operations and maximize efficiency in this rapidly evolving business environment. Moreover, there is also a rising need to cut costs and produce deliverables of the finest quality while doing so. Lean has emerged as a robust methodology that enables teams to streamline their processes, eliminate waste, and deliver exceptional results. In this blog, we will delve into the concept of lean project management, explore its fundamental principles and benefits, and provide insights into how it can revolutionize project execution.
What Is Lean Project Management?
Lean project management definition:.
Lean Project Management is an approach to project management that emphasizes efficiency, waste reduction, and continuous improvement. It is based on the principles of Lean thinking, which originated in the manufacturing industry and has since been applied to various fields, including project management.
Lean Project Management Meaning:
In Lean Project Management, the main goal is to give value to the people you’re doing the project for (like your customers or users) while using as few resources as possible and eliminating unnecessary tasks. You also want to make sure you’re doing things the smartest and most efficient way. It’s all about finding ways to make your project flow smoothly without any delays or problems. You want to make sure that each step of the project is done when it’s actually needed so you don’t waste time or effort on things that aren’t necessary at that moment.
Lean Project Management also encourages you to keep learning and improving as you work on the project. You want to keep finding better ways to do things and avoid making the same mistakes over and over again. It’s all about getting better and better at managing projects. By using Lean Project Management, you can make your projects more efficient, work better with your team, and make your customers happier. It helps you save time, resources, and effort while still delivering great results.
What are the Five Principles Of Lean Project Management?
There are five key principles of Lean. These five lean project management principles collectively provide a framework for Lean thinking and guide organizations to achieve operational excellence, enhance customer value, and drive continuous improvement throughout their processes and operations. Here’s an explanation of each principle:
Identify Value:
The first principle of Lean is to focus on creating value from the customer’s perspective. Value is defined as any action or process that directly contributes to meeting customer needs and requirements. The goal is to understand what the customer truly values and align all activities and resources to deliver that value. Organizations can streamline their processes and improve efficiency by eliminating activities that do not add value.
Map The Value Stream:
The value stream represents the entire end-to-end sequence of activities and processes required to deliver a product or service to the customer. It includes all the steps, both value-adding, and non-value-adding, from the initial request or order to the final delivery. Analyzing the value stream helps identify waste, bottlenecks, and opportunities for improvement. The focus is on optimizing the flow of value through the value stream.
Create Flow:
The flow principle aims to create a smooth and continuous flow of work through the value stream. It involves removing any barriers, delays, or interruptions that hinder the flow of value. By minimizing wait times, reducing batch sizes, and optimizing process sequencing, organizations can achieve a more efficient and responsive workflow. The goal is to eliminate waste and achieve a seamless flow from one activity to the next, enabling a steady and balanced pace of work.
Establish Pull:
The pull principle is based on the concept of demand-driven production or work initiation. Rather than pushing work based on a predetermined schedule or forecast, the pull approach involves initiating work only when there is a specific demand or request from the downstream process or customer. This helps prevent overproduction, excess inventory, and unnecessary work. Work is pulled through the value stream based on actual demand, ensuring that resources are utilized effectively and efficiently.
Seek Perfection:
The principle of perfection emphasizes the continuous pursuit of improvement and excellence. It recognizes that there is always room for improvement and encourages organizations to strive for perfection in their processes and products. This involves creating a culture of continuous learning, problem-solving, and innovation. By continuously seeking to eliminate waste, optimize processes, and exceed customer expectations, organizations can achieve higher levels of performance and competitiveness.
When To Use Lean Project Management?
Lean Project Management can be beneficial in various scenarios and contexts. Here are some situations where it is often advantageous to use Lean Project Management:
- Complex Projects: Lean Project Management can be particularly useful for managing complex projects with multiple interdependent tasks and stakeholders. It helps streamline processes, reduce waste, and enhance collaboration, making it easier to handle complexity and improve project outcomes.
- Projects with Limited Resources: When resources such as time, budget, or manpower are limited, Lean Project Management can help optimize their usage. Focusing on value and waste reduction ensures that resources are allocated effectively to deliver maximum value to the customer.
- Iterative Projects Combined With Agile: Lean Project Management shares similarities with Agile methodologies and can be combined effectively with Agile practices. It helps promote iterative development, adaptive planning, and rapid feedback cycles, making it suitable for software development and other iterative projects.
- Process Improvement Projects : When the primary focus of a project is to improve existing processes or workflows, Lean Project Management is highly applicable. Its principles and tools can help identify inefficiencies, eliminate waste, and optimize processes to achieve improved results.
- Customer-Centric Projects: Lean Project Management is valuable when the project’s success hinges on delivering maximum value to the customer or end-user. Focusing on understanding customer needs and improving flow, it ensures that customer requirements are met efficiently and effectively.
- Projects with Changing Requirements: If you anticipate that project requirements may change or evolve during the course of the project, Lean Project Management’s flexibility and adaptive nature make it a suitable approach. Its emphasis on continuous learning, adaptation, and value delivery allows for greater responsiveness to changing circumstances.
How To Implement Lean Project Management?
Implementing Lean Practices In Project Management involves several steps to ensure their successful adoption within an organization. Here’s a general outline of the implementation process:
Educate and Train:
Start by educating project managers and team members about Lean principles, concepts, and methodologies. Provide training sessions, workshops, or resources to familiarize them with Lean Project Management principles, tools, and techniques.
Identify a Pilot Project:
Select a small-scale project as a pilot to implement Lean Project Management. This allows you to test and refine Lean practices in a controlled environment before scaling up to larger projects. Choose a project that can benefit from Lean principles and has the support of stakeholders.
Map the Value Stream:
Analyze the project’s value stream to identify the flow of activities and processes involved in delivering value to the customer. Map out the current state, highlighting waste and areas for improvement. This helps visualize the project’s workflow and facilitates targeted improvements.
Eliminate Waste:
Identify and eliminate waste within the project’s processes. Apply Lean tools such as Value Stream Mapping , 5S (Sort, Set in Order, Shine, Standardize, Sustain), and Kaizen (continuous improvement) to identify and eliminate non-value-added activities, reduce waiting time, minimize overproduction, and optimize resource utilization.
Implement Visual Management:
Utilize visual management techniques to make project progress, status, and potential issues easily visible to the team. Implement tools such as Kanban boards, task boards, or visual dashboards to track work, identify bottlenecks, and facilitate communication and collaboration.
Foster Collaboration and Continuous Improvement:
Encourage collaboration and a culture of continuous improvement among team members. Promote open communication, sharing of ideas, and problem-solving. Implement regular review meetings or retrospectives to reflect on project performance, gather feedback, and identify areas for improvement.
Adopt Pull-Based Systems:
Implement pull-based systems, such as Just-In-Time (JIT) scheduling , where work is initiated based on actual demand or customer orders. This helps prevent overproduction, minimize excess inventory or work in progress, and improve resource efficiency.
Standardize Processes :
Establish standardized processes and best practices to ensure consistency and reliability. Define clear procedures, guidelines, and standard work instructions to enable efficient and repeatable project execution. Standardization facilitates knowledge transfer, simplifies training, and reduces variability.
Measure and Monitor Performance:
Define key performance indicators (KPIs) to measure project performance, such as cycle time, lead time, on-time delivery, and customer satisfaction. Regularly monitor and analyze these metrics to track progress, identify improvement opportunities, and make data-driven decisions.
Scale and Continuously Improve:
Once the pilot project has demonstrated positive results, expand the implementation of Lean Project Management principles to larger projects and across the organization. Encourage knowledge sharing, continuous learning, and ongoing refinement of Lean practices to ensure continuous improvement and sustained benefits.
Lean Project Management Case Study
We looked at how to implement lean in project management. But, let’s understand it better with a case study. The following lean project management example illustrates the application of Lean Project Management principles in a software development context:
Suppose, Company XYZ is a software development company specializing in building custom applications for clients. They decide to implement Lean Project Management principles to improve their project efficiency, reduce waste, and enhance customer value. Then, the case study will look something like we’ve explained below if they follow our mentioned implementation steps.
Initial Steps:
First, the company will provide training to project managers and development teams on Lean principles and tools. They will learn about value stream mapping, waste identification, pull systems, and visual management techniques. Next, Company XYZ will select a small-scale software development project as the pilot for Lean implementation. The project will involve creating a web-based application for a client.
Planning Steps:
The team will then map out the value stream of the project, identifying each step from gathering requirements to final deployment. They will identify areas of waste, such as excessive handovers and delays in receiving client feedback. After this, the team will focus on eliminating waste using Lean tools. They will reduce handoffs by involving the client directly in requirements gathering and design discussions. They will also work on minimizing waiting time by implementing daily stand-up meetings and continuous communication channels.
Next, the team will implement a Kanban board to visualize the project workflow. They will divide tasks into columns such as “To Do,” “In Progress,” and “Completed.” This will allow team members to see the status of tasks at a glance, identify bottlenecks, and collaborate effectively. While doing this, the team will also foster a culture of collaboration and continuous improvement. They must hold regular retrospectives to reflect on project performance, identify process bottlenecks, and propose improvements. They must also encourage open communication and shared responsibility for problem-solving.
Implementation Steps:
Further, the team will implement a pull-based system by using user stories as the unit of work. They will only pull in new user stories when the team will have the capacity to work on them. This will prevent overloading and ensure that work is initiated based on actual demand. The team will also establish standardized processes and coding practices to improve consistency and efficiency. Further, they will produce templates for requirements documentation, coding conventions, and testing procedures. Standardization methods will help streamline development activities and reduce variability.
To measure project performance, key performance indicators (KPIs) will be established. The team will have to track metrics such as cycle time, lead time, defect rates, and client satisfaction. Moreover, regularly reviewing these metrics will help identify areas for improvement and thereby make data-driven decisions. After the successful implementation of Lean Project Management principles in the pilot project, the company can then expand its use to other software development projects. They can also encourage knowledge sharing and hold regular knowledge transfer sessions to ensure continuous improvement and organizational learning.
As a result of implementing Lean Project Management, Company XYZ will thus experience reduced project lead times, improved client satisfaction, and increased efficiency. Moreover, the team will also be able to manage project complexities better, minimize waste, and deliver value to their clients in a more efficient and timely manner.
Agile Vs Lean Project Management
Agile Project Management and Lean Project Management are two distinct approaches that share similar goals but have different emphases. Here’s a comparison between Agile and Lean Project Management:

Pros And Cons Of Lean Project Management
We looked at all the ways lean works in project management and the practices that allow it’s implementation. It is only fair that we let you in on the advantages and disadvantages of lean project management before you decide to implement it in your projects.
Benefits Of Lean Project Management:
- Waste Reduction: Lean Project Management focuses on identifying and eliminating waste, resulting in increased efficiency and reduced costs.
- Customer Value: By prioritizing customer value, lean ensures that resources are allocated to activities that directly contribute to meeting customer needs. Thus, it prioritizes the consumer’s needs by efficiently planning out the resource front.
- Continuous Improvement: Lean encourages a culture of continuous improvement, enabling teams to identify and address inefficiencies and bottlenecks throughout the project lifecycle.
- Streamlined Processes: Lean Project Management helps streamline processes, reducing complexity and enhancing workflow by eliminating non-value-added activities.
- Faster Delivery: While reducing waste and focusing on value-adding activities, Lean Project Management facilitates faster project delivery and time-to-market.
- Improved Collaboration: Lean emphasizes cross-functional collaboration and communication, fostering a more cohesive and productive team environment.
- Adaptability: Lean allows for flexibility and adaptation to changing project requirements, enabling teams to respond quickly to customer feedback and evolving market conditions.
Cons of Lean Project Management:
- Steep Learning Curve: Implementing Lean Project Management may require a significant learning curve for project managers and team members who are new to Lean principles and practices.
- Resistance to Change: Organizations and team members resistant to change may find it challenging to embrace not only the cultural differences but also the process changes associated with Lean Project Management.
- Initial Investment: Implementing Lean may require an initial investment of time, resources, and training to educate and align team members with Lean principles.
- Lack of Detailed Planning: Lean’s focus on adaptability and flexibility may result in less detailed upfront planning, which can, thus, be challenging for projects with complex dependencies or strict regulatory requirements.
- Overemphasis on Efficiency: While Lean focuses on efficiency, there is a risk of prioritizing efficiency at the expense of creativity and innovation, potentially overlooking opportunities for breakthrough ideas.
- Limited Documentation: Lean Project Management may prioritize real-time collaboration and visual management over comprehensive documentation, which could pose challenges for projects requiring stringent documentation.
- Potential for Overlooking Non-Value-Added Activities: In the pursuit of waste reduction, there is a risk of overlooking activities that may not directly add value but are necessary for compliance, risk management, or long-term sustainability.
Why Go For Lean Project Management?
After weighing the pros and cons of lean project management, we will proceed to emphasize how lean methods in project management can help you achieve project success.
Increased Efficiency: By focusing on waste reduction and process optimization, lean helps teams operate more efficiently. This leads to improved productivity, shorter project cycles, and reduced costs.
Enhanced Quality: By actively seeking customer input and emphasizing value creation, lean ensures that project outcomes meet or exceed expectations. Further, rigorous quality control processes minimize errors and rework, resulting in higher-quality deliverables.
Flexibility and Adaptability: The iterative nature of lean enables teams to respond swiftly to changing project requirements. It promotes a mindset of adaptability, which thereby enables teams to not only pivot, but also make course corrections, and deliver successful outcomes even in dynamic environments.
Increased Customer Satisfaction: Next, Lean focuses on understanding and delivering customer value. Organizations can enhance customer satisfaction and build stronger relationships by aligning project efforts with customer needs and continuously seeking feedback.
Continuous Learning and Innovation: The culture of continuous improvement embedded in lean project management encourages teams to learn from past experiences and innovate. Further, the lessons learned are incorporated into future projects, leading to ongoing innovation and growth.
How Is Lean Associated With Disciplined Agile?
Lean principles are a part of the Disciplined Agile (DA) framework. Disciplined Agile incorporates a wide range of methodologies and practices, such as Scrum, Kanban, and also including lean, to provide organizations with a flexible and tailored approach to project management. Within the Disciplined Agile framework, lean principles and practices can be combined with other methodologies to create a customized approach that suits the unique needs of each project and achieve project success. The DA framework acknowledges the value of lean principles, which focus on eliminating waste, optimizing processes, and delivering customer value. Therefore, its practices are considered a part of the Disciplined Agile toolkit , allowing organizations to select and apply lean principles appropriate for their projects and contexts.
The DA Journey
The disciplined agile (DA) journey starts with the fundamentals in the DASM (Disciplined Agile Scrum Master) course. Learners then delve deeper into disciplined agile concepts and the application of lean in the DASSM (Disciplined Agile Senior Scrum Master) certification . Next, come the Disciplined Agile Coach (DAC) certification and the Disciplined Agile Value Stream Consultant (DAVSC) . As mentioned above, the value stream aspect of lean is covered in detail in the DAVSC certification. At ProThoughts, we clear all your doubts about lean and disciplined agile in our DA certification training programs. Want to make your projects go lean? Then ProThoughts is the way!
Summarizing this comprehensive guide, lean project management aims to eliminate waste, improve efficiency, and deliver value to customers through the application of lean principles in projects. Moreover, by focusing on value, optimizing workflows, and fostering continuous improvement, organizations can achieve tremendous project success and create a culture of excellence. Lean has a broad set of advantages that you could bring while also roping agile perks, using the lean-agile project management approach. Want to get started? Book a consultation session with ProThoughts today!
Previous Post
What is program manager, how does disciplined agile improve your way of working (wow), quick enquiry.
- Project Management
- PMP Certification
- PgMP Certification
- Disciplined Agile
Follow Us on:
Download dassm brochure, upcoming dassm batches, upcoming davsc batches, upcoming dac batches.
- Corporate Training
- Online Mock Tests
- e – Learning
- Refer & Earn
- Become a Guest Speaker
- About Rita Mulcahy
- Game-based Learning Approach
- Announcements
- Contact us page
- Our Experts
Free Resources
- PMP Eligibility Calculator
- PgMP Certification Eligibility
- DA Eligibility Calculator
- SAFe Eligiblity Calculator
Stay Connected
We accept

PMP is a registered mark of the Project Management Institute, Inc. CAPM is a registered mark of the Project Management Institute, Inc. PMI-ACP is a registered mark of the Project Management Institute.
The PMI Registered Education Provider logo is a registered mark of the Project Management Institute, Inc. PMBOK is a registered mark of the Project Management Institute, Inc. ProThoughts Solution is an ATP of the Project Management Institute with Global ATP ID 4032.
Note: ProThoughts reserves the right to cancel or reschedule events in case of insufficient registrations, or if presenters cannot attend due to unforeseen circumstances. You are therefore advised to consult a ProThoughts Consultant prior to making any travel arrangements for a workshop. For more details, please refer Cancellation & Refund Policy.
Terms & Conditions Privacy Policy Rescheduling policy
© 2024 Prothoughts. All rights reserved
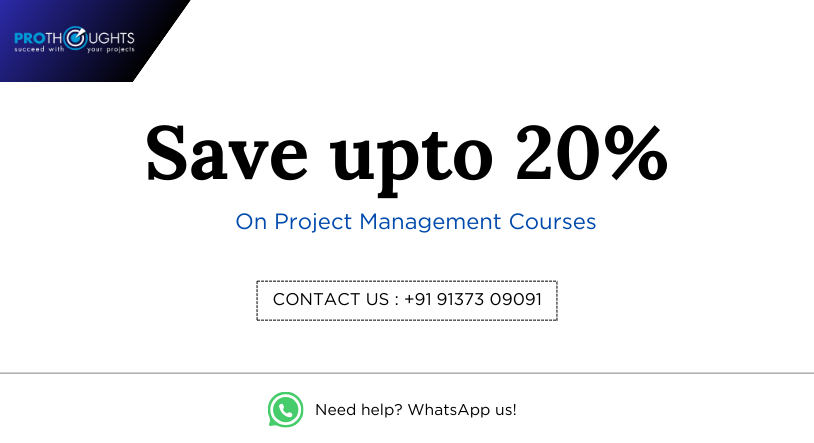
FILL THE DETAILS
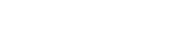
- Case Studies
- Lean Agile PM Academy
- Knowledge Center
CEO Inquisitive, provocative and results oriented, David is willing to dig into problems until their true essence is understood and the solution is executed. We love that at Playbook!
Posts containing:
Lean Agile Project Management Case Study
Recently, we had the fortunate opportunity to talk to our second Playbook customer about the successful completion of their large and complex project. In this particular implementation, the company achieved 60% reduction in cycle time as well as a 50% reduction in cost. Besides the obvious wins, three additional items made this result interesting:
- First, it wasn’t an R&D project–it was an enterprise IT project;
- Second, the scope was at least twice as big as the previous one; and
- Third, we achieved this result before Playbook software was developed.
In other words, we implemented the Playbook method using spreadsheets, sticky notes (lots of them!), Sharpies, large foam boards, copy machines and web cams!
What we discovered was the methods work for any project with a lot of complexity and uncertainty, and not just R&D for manufacturing.
Here’s the story behind that effort and some of the project highlights…
I met Patrick Shannon at the 2009 PTC/USER World Event where I was giving a presentation titled “Lean NPD & PLM: A Perfect Marriage, or a Perfect Storm?”
At the time, Patrick Shannon was the CIO at a large aerospace and defense company and was about to launch a project to upgrade their PLM system. A few years prior, they had completed a similar project and weren’t happy with how long it had taken. The new project was twice the scope–twice as much data, twice as many users, and twice as much functionality. As such, Patrick knew there was a good chance the new project would take twice as long, and that was not acceptable.
Since I was talking about Lean Project Management and PLM in the same presentation, Patrick contacted us to ask if the Playbook method would work on an Enterprise IT System upgrade.
After a bit of Q&A, we saw no reason why not, so we accepted the challenge.
Understanding the Current State
Back then we always started an engagement with a diagnostic phase. This phase involved creating a Current Reality Tree (CRT) and a Value Steam Map (VSM).
The CRT is a very robust version of a root cause assessment. The very popular “Five Whys” will get you to a root cause, but in complex environments it’s very likely there are multiple root causes. So you have to find all of them and the CRT has the effect of asking “Five Why Else’s.” In other words, rather than digging straight down, it also looks laterally for issues. The CRT is then used to identify all of the necessary solutions and connect them to the issues they will resolve.
We followed the CRT exercise with a Value Stream Mapping session to highlight the overall process, the wait times, repeat loops, etc. This work is beneficial to establishing a high-level project plan.
And both methods are great for generating buy-in to the subsequent solution. Patrick still had notes (and a great memory!) of the engagement and reminded us that we completed the diagnosis and initial methods training within four days.

Playbook Lean Agile Method
Other important foundational pieces that we put in place were:
- Project Economic Modeling
- Project Risk Management Process
- Decentralized Planning
- Manual Visual Project Boards
- Daily Standup meetings
- Rolling Wave Planning
These are all key parts of the Playbook Method.
Fixing the Airplane While Flying
This entire process was completed over a six-week period, which may sound long, but all of the coaching work was done on the actual project so there was very little downtime during the training. And most of the resources were assigned to other projects and were only available part-time, so we were literally fixing the airplane while it was flying.
Unprecedented Results
As I mentioned, the results were unprecedented. Even though the scope of this project was at least double (data, users, functionality, etc.), we finished it in 60% less time—literally 12 months faster than the previous smaller project. And because of the unexpectedly short duration, the company saved over $400K on their project budget.
Results like this don’t go unnoticed and their team won their company’s Silver Level Chairman’s Award.
From Patrick’s perspective, “The Playbook method is a game changer. Even though it was built specifically for product development, the methods are so practical and robust that they work in any type of complex project. In fact, Playbook becomes increasingly valuable as projects become larger, more complex, with more people—especially remote resources—and longer schedules.”
Project Management Issues are Consistent Across Complex IT and Complex R&D Projects
To demonstrate why this worked so well even though this was an enterprise PLM system upgrade and not an R&D project, these were some of the root causes we discovered. Notice how much they sound like the same issues faced by hardware product development teams...
- Planning is not thorough
- Cross-functional communication is lacking
- Resources have other commitments
- Schedule isn’t visible
- Schedule is out of date
- Priorities are not clear
As you can see, Playbook is both a methodology and a visual management tool that supports a fit-for-purpose approach to product development, but it also works for any project that has a lot of complexity and uncertainty.
If you would like to find out if these methods will work on your non-R&D project, feel free to schedule a free 30-Minute strategy session with me, David Paulson, President, Playbook .
Subscribe to the blog
Popular topics.
- Lean project management (118)
- Lean product development (117)
- Agile project management (53)
- Lean and agile product development (52)
- Hardware development (45)
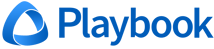
Address PO Box 18027 Boulder, CO 80308 303-323-4296 [email protected]
Lean Project Management Lean Product Development Agile Development
- Features and Benefits
- [email protected]
- 303-323-4296 x 99
- Privacy Policy
- Worldwide standard certification
- Accredited Training Organizations
- LSS Training content
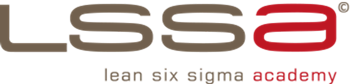
Lean Six Sigma Case Studies
Welcome to the Lean Six Sigma Academy’s Case Studies section! Here, you will find a collection of real-world examples of how companies have successfully implemented the Lean Six Sigma methodology to improve their business operations. Each case study includes an overview of the business challenge that was faced, the approach that was taken, the results that were achieved and feedback from the client on their experience. These case studies showcase the wide range of industries and organizations that have benefited from Lean Six Sigma, and serve as inspiration and guidance for those looking to implement the methodology in their own business.
OE Partners
Orrcon Steel
The toyota production system.

An official website of the Department of Health and Human Services

Browse Topics
Priority populations.
- Children/Adolescents
- Racial/Ethnic Minorities
- Rural/Inner-City Residents
- Special Healthcare Needs
- Clinicians & Providers
- Data & Measures
- Digital Healthcare Research
- Education & Training
- Hospitals & Health Systems
- Prevention & Chronic Care
- Quality & Patient Safety
Publications & Products
- AHRQ Publishing and Communications Guidelines
- Search Publications
Research Findings & Reports
- Evidence-based Practice Center (EPC) Reports
- Fact Sheets
- Grantee Final Reports: Patient Safety
- Making Healthcare Safer Report
- National Healthcare Quality and Disparities Reports
- Technology Assessment Program
- AHRQ Research Studies
National Healthcare Quality and Disparities Report
Latest available findings on quality of and access to health care
- Data Infographics
- Data Visualizations
- Data Innovations
- All-Payer Claims Database
- Healthcare Cost and Utilization Project (HCUP)
- Medical Expenditure Panel Survey (MEPS)
- AHRQ Quality Indicator Tools for Data Analytics
- State Snapshots
- United States Health Information Knowledgebase (USHIK)
- Data Sources Available from AHRQ
Funding & Grants
Notice of funding opportunities, research policies.
- Notice of Funding Opportunity Guidance
- AHRQ Grants Policy Notices
- AHRQ Informed Consent & Authorization Toolkit for Minimal Risk Research
- HHS Grants Policy Statement
- Federal Regulations & Authorities
- Federal Register Notices
- AHRQ Public Access Policy
- Protection of Human Subjects
Funding Priorities
- Special Emphasis Notices
- Staff Contacts
Training & Education Funding
Grant application, review & award process.
- Grant Application Basics
- Application Forms
- Application Deadlines & Important Dates
- AHRQ Tips for Grant Applicants
- Grant Mechanisms & Descriptions
- Application Receipt & Review
- Study Sections for Scientific Peer Review
- Award Process
Post-Award Grant Management
- AHRQ Grantee Profiles
- Getting Recognition for Your AHRQ-Funded Study
- Grants by State
- No-Cost Extensions (NCEs)
AHRQ Grants by State
Searchable database of AHRQ Grants
AHRQ Projects funded by the Patient-Centered Outcomes Research Trust Fund.
- Press Releases
- AHRQ Social Media
- Impact Case Studies
- AHRQ News Now
- AHRQ Research Summit on Diagnostic Safety
- AHRQ Research Summit on Learning Health Systems
- National Advisory Council Meetings
- AHRQ Research Conferences
- AHRQ's 35th Anniversary
- Mission and Budget
- AHRQ's Core Competencies
- National Advisory Council
- Careers at AHRQ
- Maps and Directions
- Other AHRQ Web Sites
- Other HHS Agencies
- Testimonials
Organization & Contacts
- Centers and Offices
- Organization Chart
- Key Contacts

- Advanced Methods in Delivery System Research
- Delivery System Research Initiative
- Initiatives
- System Redesign Responses to Challenges in Safety-Net System
- Improving Care Delivery Through Lean: Implementation Case Studies
Table of Contents
- Introduction to the Case Studies
- Case 1. Lakeview Healthcare
- Case 2. Central Hospital
- Case 3. Grand Hospital Center
- Case 4. Suntown Hospital
- Case 5. Heights Hospital
- Case 6. Horizon Hospital—Lakeview Healthcare
Contract Report
This report presents an introduction to the application of Lean principles in health care settings to improve quality of care, increase efficiency, lower costs, and provide better patient outcomes. Lean is an organizational redesign approach focused on elimination of waste, which is defined as any activity that consumes resources (e.g., staff, time, money, space) without adding value to those being served by the process. In addition to background information and the results of a literature review, the report presents six case studies from five organizations that implemented Lean principles in different types of health care settings. Recommendations are provided for similar organizations wishing to implement Lean in their facilities.
Prepared by:
American Institutes for Research Kristin L. Carman, PhD Kathy Paez, RN, PhD Jennifer Stephens, MPH Lauren Smeeding Steven Garfinkel, PhD Callan Blough
Urban Institute Kelly Devers, PhD
Mayo Clinic Michelle Hoover, Med Tony Spaulding, MS David Mapes
Introduction Project Background Rationale and Purpose Conceptual Framework Purpose of Case Studies Methods Definition of the Sample Data Collection Activities Data Analysis Limitations References Case 1. Lakeview Healthcare Organizational Background Description of the Health Care System Description of the Health Care Organization Other Environmental Context Lean and Quality Improvement at the Organization History of Quality and Efficiency Improvement Efforts at the Organization Initiation of Lean at the Organization Alignment of Lean and Quality Improvement Efforts Process for Implementing Lean Lean Project Selection Process Planning Implementation of Lean Lean Training Lean Project Implementation Lean Teams Monitoring, Control, and Sustainment Dissemination and Spread of Findings Lean Projects Studied Cross-Cutting Project Department-Specific Projects Projects Started But Not Fully Implemented Outcomes of Lean Intermediate Outcomes Ultimate Outcomes Business or Strategic Case Factors that Influenced the Success of Lean Implementation Organizing the Lean Initiative Implementing the Kaizen Initiative Staff Engagement Education and Training Communication About Lean Lean Team Composition and Size Routinization of Lean Processes Conclusions Recommendations for Similar Organizations Implementing Lean
Case 2. Central Hospital Organizational Background Description of the Health System Description of the Health Care Organization Leadership Staffing Other Environmental Context Lean and Quality Improvement at the Organization History of Quality and Efficiency Improvement Efforts at the Organization Initiation of Lean at the Organization Alignment of Lean and Quality Improvement Efforts Process for Implementing Lean Lean Project Selection Process Planning Implementation of Lean Process for Lean Projects Monitoring, Control, and Sustainment Dissemination and Spread of Findings Lean Projects Studied Improvement of "Door-to-Balloon" Process Management of Surgical Procedure Cards Outcomes of Lean Intermediate Outcomes Ultimate Outcomes Factors that Influenced Success of Lean Implementation Organizing the Lean Initiative Implementing the Lean Initiative Conclusions Recommendations for Similar Organizations Implementing Lean
Case 3. Grand Hospital Center Organizational Background Description of the Health Care System Description of the Health Care Organization Other Environmental Context Lean and Quality Improvement at the Organization History of Quality and Efficiency Improvement Efforts at the Organization Initiation of Lean at the Organization Alignment of Lean and Quality Improvement Efforts Process for Implementing Lean Planning Implementation of Lean Lean Project Selection Process Lean Training Process for Lean Projects Monitoring, Control, and Sustainment Dissemination and Spread of Findings Lean Projects Studied Hip and Knee Replacement Costs Cardiology Follow-up Appointment Scheduling Outcomes of Lean Intermediate Outcomes Ultimate Outcomes Factors that Influenced Success of Lean Implementation Organizing the Lean Initiative Implementing the Lean Initiative Conclusions Recommendations for Similar Organizations Implementing Lean
Case 4. Suntown Hospital Organizational Background Description of the Health Care Organization Other Environmental Context Lean and Quality Improvement at the Organization History of Quality and Efficiency Improvement Efforts at the Organization Initiation of Lean at the Organization Process for Implementing Lean Planning for Implementation of Lean Lean Project Selection Process Lean Training Process for Lean Projects Monitoring, Control, and Sustainment Dissemination and Spread of Findings Lean Projects Studied Urinary Tract Infection Prevention and Reduction Redesigning the Outpatient Medication Prescribing Process Outcomes of Lean Intermediate Outcomes Ultimate Outcomes Factors that Influenced Success of Lean Implementation Organizing the Lean Initiative Implementing the Lean Initiative Conclusions Recommendations for Similar Organizations Moving Forward
Case 5. Heights Hospital Organizational Background Description of the Health System Description of the Health Care Organization Other Environmental Context Lean and Quality Improvement at the Organization History of Quality and Efficiency Improvement Efforts at the Organization Initiation of Lean at the Organization Alignment of Lean and Quality Improvement Efforts Process for Implementing Lean Planning for Implementation of Lean Lean Value Stream and Project Selection Process Lean Training Other Training Process for Lean Projects Monitoring, Control, and Sustainment Dissemination and Spread of Findings Lean Projects Studied Emergency Department Value Stream Projects (Retrospective) Pediatric Continuity of Care Project (Prospective) Outcomes of Lean Intermediate Outcomes Ultimate Outcomes Factors that Influenced Success of Lean Implementation Organizing the Lean Initiative Implementing the Lean Initiative Conclusions Recommendations for Similar Organizations Implementing Lean
Case 6. Horizon Hospital—Lakeview Healthcare Organizational Background Description of the Health System: Lakeview Healthcare Description of Horizon Hospital Other Environmental Context Lean and Quality Improvement at the Organization History of Quality and Efficiency Improvement Efforts at the Organization Initiation of Lean at the Organization Alignment of Lean and Quality Improvement Efforts Process for Implementing Lean Lean Project Selection Process Planning Implementation of Lean Lean Training Lean Project Implementation Lean Teams Monitoring, Control, and Sustainment Dissemination and Spread of Findings Lean Hospital Project Horizon Hospital Outcomes of Lean Intermediate Outcomes Ultimate Outcomes Factors that Influenced Success of Lean Implementation Organizing the Lean Initiative Implementing the Lean Initiative Conclusions Recommendations for Similar Organizations Using Principles to Design and Hospital
This report was prepared for the Agency for Healthcare Research and Quality by the American Institutes for Research (Contract No. HHSA290200600019). It is in the public domain and may be used and reprinted without permission. Citation as to source is appreciated.
Publication: 13(15)-0056
PDF version (PDF, 3 MB)
Internet Citation: Improving Care Delivery Through Lean: Implementation Case Studies. Content last reviewed November 2014. Agency for Healthcare Research and Quality, Rockville, MD. https://www.ahrq.gov/practiceimprovement/systemdesign/leancasestudies/index.html

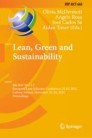
European Lean Educator Conference
ELEC 2022: Lean, Green and Sustainability pp 72–81 Cite as
A Lean Approach for Reducing Downtimes in Healthcare: A Case Study
- Stefano Frecassetti ORCID: orcid.org/0000-0002-9649-314X 19 ,
- Matteo Ferrazzi ORCID: orcid.org/0000-0001-9035-0773 19 &
- Alberto Portioli-Staudacher ORCID: orcid.org/0000-0002-9807-1215 19
- Conference paper
- First Online: 12 February 2023
408 Accesses
Part of the book series: IFIP Advances in Information and Communication Technology ((IFIPAICT,volume 668))
Lean Management is considered one of the most successful management paradigms for enhancing operational performance in the manufacturing environment. However, it has been applied throughout the years to several sectors and organisational areas, such as service, healthcare, and office departments. After the Covid-19 outbreak, increasing attention has been given to potential performance improvements in healthcare organisations by leveraging Lean. This paper intends to add further knowledge to this field by presenting a case study in a hospital. In this paper, a pilot project is presented carried out in a healthcare organisation. Lean methods were used to improve the operating room performance, particularly by reducing the operating room changeover time. The A3 template was used to drive the project and implement a new procedure using the Single Minute Exchange of Die (SMED) method. With the implementation of the new procedure, the changeover time between two different surgeries in the operating room was significantly reduced, together with a more stable and reliable process.
- Lean thinking
This is a preview of subscription content, log in via an institution .
Buying options
- Available as PDF
- Read on any device
- Instant download
- Own it forever
- Available as EPUB and PDF
- Compact, lightweight edition
- Dispatched in 3 to 5 business days
- Free shipping worldwide - see info
- Durable hardcover edition
Tax calculation will be finalised at checkout
Purchases are for personal use only
Amati, M., et al.: Reducing changeover time between surgeries through lean thinking: an action research project. Front. Med. 9 (2022). https://doi.org/10.3389/fmed.2022.822964
Bharsakade, R.S., Acharya, P., Ganapathy, L., Tiwari, M.K.: A lean approach to healthcare management using multi criteria decision making. Opsearch 58 (3), 610–635 (2021). https://doi.org/10.1007/s12597-020-00490-5
Article Google Scholar
Costa, F., Kassem, B., Staudacher, A.P.: Lean office in a manufacturing company. In: Powell, D.J., Alfnes, E., Holmemo, M.D.Q., Reke, E. (eds.) Learning in the Digital Era. IFIP Advances in Information and Communication Technology, pp. 351–356. Springer, Cham (2021). https://doi.org/10.1007/978-3-030-92934-3_36
Chapter Google Scholar
Costa, F., Kassem, B., Portioli-Staudacher, A.: Lean thinking application in the healthcare sector. In: Powell, D.J., Alfnes, E., Holmemo, M.D.Q., Reke, E. (eds.) Learning in the Digital Era. IFIP Advances in Information and Communication Technology, pp. 357–364. Springer, Cham (2021). https://doi.org/10.1007/978-3-030-92934-3_37
Curatolo, N., Lamouri, S., Huet, J.C., Rieutord, A.: A critical analysis of Lean approach structuring in hospitals. Bus. Process Manag. J. 20 (3), 433–454 (2014)
D’Andreamatteo, A., Iannia, L., Lega, F., Sargiacomo, M.: Lean in healthcare: a comprehensive review. Health Policy 119 (9), 1197–1209 (2015)
Guercini, J., et al.: Application of SMED methodology for the improvement of operations in operating theatres. The case of the Azienda Ospedaliera Universitaria Senese. Mecosan 24 (98), 83–203 (2016). https://doi.org/10.3280/mesa2016-098005
Henrique, D.B., Godinho Filho, M.: A systematic literature review of empirical research in Lean and Six Sigma in healthcare. Total Qual. Manag. Bus. Excell. 31 (3–4), 429–449 (2020)
Henrique, D.B., Filho, M.G., Marodin, G., Jabbour, A.B.L.D.S., Chiappetta Jabbour, C.J.: A framework to assess sustaining continuous improvement in lean healthcare. Int. J. Prod. Res. 59 (10), 2885–2904 (2020)
Holweg, M.: The genealogy of lean production. J. Oper. Manag. 25 (2), 420–437 (2007). https://doi.org/10.1016/j.jom.2006.04.001
Sales-Coll, M., de Castro, R., Hueto-Madrid, J.A.: Improving operating room efficiency using lean management tools. Prod. Plan. Control 1–14 (2021). https://doi.org/10.1080/09537287.2021.1998932
Matos, I.A., Alves, A.C., Tereso, A.P.: Lean principles in an operating room environment: an action research study. J. Health Manag. 18 (2), 239–2577 (2016)
Portioli-Staudacher, A.: Lean healthcare. An experience in Italy. In: Koch, T. (ed.) APMS 2006. ITIFIP, vol. 257, pp. 485–492. Springer, Boston, MA (2008). https://doi.org/10.1007/978-0-387-77249-3_50
Rosa, A., Marolla, G., Lega, F., et al.: Lean adoption in hospitals: the role of contextual factors and introduction strategy. BMC Health Serv. Res. 21 , 889 (2021). https://doi.org/10.1186/s12913-021-06885-4
Rosa, C., Silva, F.J.G., Ferreira, L.P., Campilho, R.D.S.G.: SMED methodology: the reduction of setup times for Steel Wire-Rope assembly lines in the automotive industry. Procedia Manuf. 13 , 1034–1042 (2017)
Shah, R., Ward, P.T.: Lean manufacturing: context, practice bundles, and performance. J. Oper. Manag. 21 (2), 129–149 (2003)
Sunder, M.V., Mahalingam, S., Krishna, M.S.N.: Improving patients’ satisfaction in a mobile hospital using Lean Six Sigma – a design-thinking intervention. Prod. Plan. Control 31 (6), 512–526 (2020)
Torri, M., Kundu, K., Frecassetti, S., Rossini, M.: Implementation of Lean in IT SME company: an Italian case. Int. J. Lean Six Sigma (2021)
Google Scholar
Welsh, I., Lyons, C.M.: Evidence-based care and the case for intuition and tacit knowledge in clinical assessment and decision making in mental health nursing practice: an empirical contribution to the debate. J. Psychiatr. Ment. Health Nurs. 8 (4), 299–305 (2001)
Yin, R.K.: Case Study Research and Applications: Design and Methods, 6th edn. Sage, Los Angeles (2018)
Download references
Author information
Authors and affiliations.
Politecnico di Milano, Department of Management, Economics and Industrial Engineering, Milano, Italy
Stefano Frecassetti, Matteo Ferrazzi & Alberto Portioli-Staudacher
You can also search for this author in PubMed Google Scholar
Corresponding author
Correspondence to Stefano Frecassetti .
Editor information
Editors and affiliations.
University of Galway, Galway, Ireland
Olivia McDermott
LUM University "Giuseppe Degennaro", Casamassima, Italy
Angelo Rosa
Instituto Superior de Engenharia do Porto, Porto, Portugal
José Carlos Sá
Aidan Toner
Rights and permissions
Reprints and permissions
Copyright information
© 2023 IFIP International Federation for Information Processing
About this paper
Cite this paper.
Frecassetti, S., Ferrazzi, M., Portioli-Staudacher, A. (2023). A Lean Approach for Reducing Downtimes in Healthcare: A Case Study. In: McDermott, O., Rosa, A., Sá, J.C., Toner, A. (eds) Lean, Green and Sustainability. ELEC 2022. IFIP Advances in Information and Communication Technology, vol 668. Springer, Cham. https://doi.org/10.1007/978-3-031-25741-4_8
Download citation
DOI : https://doi.org/10.1007/978-3-031-25741-4_8
Published : 12 February 2023
Publisher Name : Springer, Cham
Print ISBN : 978-3-031-25740-7
Online ISBN : 978-3-031-25741-4
eBook Packages : Computer Science Computer Science (R0)
Share this paper
Anyone you share the following link with will be able to read this content:
Sorry, a shareable link is not currently available for this article.
Provided by the Springer Nature SharedIt content-sharing initiative
- Publish with us
Policies and ethics
Societies and partnerships

- Find a journal
- Track your research
- Research article
- Open access
- Published: 28 August 2021
Lean adoption in hospitals: the role of contextual factors and introduction strategy
- Angelo Rosa 1 ,
- Giuliano Marolla ORCID: orcid.org/0000-0002-2095-8641 1 ,
- Federico Lega 2 &
- Francesco Manfredi 1
BMC Health Services Research volume 21 , Article number: 889 ( 2021 ) Cite this article
4591 Accesses
13 Citations
2 Altmetric
Metrics details
In the scientific literature, many studies describe the application of lean methodology in the hospital setting. Most of the articles focus on the results rather than on the approach adopted to introduce the lean methodology. In the absence of a clear view of the context and the introduction strategy, the first steps of the implementation process can take on an empirical, trial and error profile. Such implementation is time-consuming and resource-intensive and affects the adoption of the model at the organizational level. This research aims to outline the role contextual factors and introduction strategy play in supporting the operators introducing lean methodology in a hospital setting.
Methodology
The methodology is revealed in a case study of an important hospital in Southern Italy, where lean has been successfully introduced through a pilot project in the pathway of cancer patients. The originality of the research is seen in the detailed description of the contextual elements and the introduction strategy.
The results show significant process improvements and highlight the spontaneous dissemination of the culture of change in the organization and the streamlined adoption at the micro level.
The case study shows the importance of the lean introduction strategy and contextual factors for successful lean implementation. Furthermore, it shows how both factors influence each other, underlining the dynamism of the organizational system.
Peer Review reports
Over the last decade, healthcare has been called upon to respond to the increasing pressures arising from changes in demand – due to epidemiological changes and the demand for quality and safety – and increased costs due to the introduction of new technologies [ 1 , 2 ]. These major challenges are exacerbated by the shrinking resources available in health systems and, for most countries, by the principle of universal access to patient care. In order to meet the patients’ needs, a hospital must utilize a number of scarce resources at the right time: beds, technological equipment, staff with appropriate clinical skills, medical devices, diagnostic reports, etc. [ 1 , 2 ].
One of the most relevant issues for the management of a healthcare provider is the management of patient flows in order to purchase, make available, and use these scarce resources at the right time and in the right way, and to ensure the best possible care [ 3 , 4 , 5 ]. In this scenario, hospitals need to focus on the patient pathways in order to ensure fast, safe, and high-quality service [ 3 , 6 , 7 , 8 ]. The search for solutions to these challenges has extended beyond the boundaries of healthcare practices to study organizational methods and paradigms that have been successfully implemented in other sectors [ 3 , 5 ]. Among these, lean thinking has proven to be one of the most effective solutions for improving operational performance and process efficiency and for reducing waste [ 5 , 9 ]. Lean is a process-based methodology focused on improving processes to achieve a customer ideal state and the elimination of waste [ 10 ]. Waste is defined as the results of unnecessary or wrong tasks, actions or process steps that do not directly benefit the patient. The taxonomy of waste is: overproduction, defects, waiting, transportation, inventory, motion, extra-processing and unused talent [ 3 , 4 , 5 ]. In addition, lean addresses other key service issues such as continuous improvement and employee empowerment, whether healthcare professionals or managers [ 1 , 11 , 12 ]. Lean healthcare is defined as a strategic approach to increasing the reliability and stability of healthcare processes [ 7 , 13 , 14 ].
The first documented cases of lean applications in a hospital setting (HS) date back to the late 1990s. These aimed at improving patient care processes, interdepartmental interaction, and employee satisfaction [ 1 , 2 ]. The Virginia Mason Medical Center is one of the first and most emblematic examples of a successful migration of lean methodology from the manufacturing sector to healthcare. The hospital, based on the principles of the Toyota Production System, created the Virginia Mason Production System, a holistic management model in continuous evolution that not only had a strong impact on the quality of the services provided and on the reduction of lead time, but it also led to a decrease in operating costs [ 14 , 15 ]. Over time, many hospitals have followed in the footsteps of the Virginia Mason Medical Center [ 8 , 16 , 17 ]. The lean paradigm crossed the US border and spread to other countries such as Canada and England [ 5 , 12 ]. It was not until the early 2000 that the model was introduced in European hospitals [ 12 , 16 ].
The implementation of the lean paradigm in HS environments has increasingly attracted the attention of researchers and professionals. The interest in lean in HSs was fostered by the idea that the paradigm was particularly suitable for hospitals because its concepts are intuitive, compelling, and, therefore, easy for medical staff to use [ 18 , 19 ]. However, over time, alongside the evidence of successful implementation of lean in HSs, much of the research has shown failures in adopting the paradigm [ 5 , 20 , 21 ]. Moreover, a literature review showed that most of the cases were characterized by a partial implementation of lean methodologies and concerned single processes in the value chain or restricted technical applications [ 20 , 22 ]. Even today, few hospitals apply lean principles at a systemic level [ 23 , 24 ].
The failure of lean implementation is a hot topic. Many authors who have focused their studies on social and managerial issues have highlighted the existence of factors that either enable or hinder the implementation of lean. These factors are mostly related to the context and the implementation strategies [ 5 , 16 , 25 , 26 , 27 ]. Lean implementation is not self-evident, and the process of transforming an organization into a lean organization requires a long-term strategic vision, a commitment by management, and a culture of change in the entire organization [ 5 , 16 , 26 ]. Contextual factors influence successful implementation and introduction strategy; lean adoption, in turn, changes contextual factors. A lean transformation must be planned and managed; it is not a quick solution, but a strategic plan in constant evolution [ 5 , 28 , 29 ]. From this point of view, the introduction phase plays a fundamental role in implementation because it facilitates the dissemination of the lean principle in hospitals and enables the contextual elements that support change. Although most researchers have recognized the role of the introduction step, the impact of this phase on contextual factors has been poorly reported on in the literature [ 5 , 12 , 20 ]. Most of the articles have focused more on the benefits of this phase than on how to manage it.
In light of this, it is necessary to examine how hospitals introduce lean into their clinical pathways in order to explain the success of the lean implementation. Starting with an in-depth analysis of the contextual factors discussed in the literature, the document helps to clarify what drives success in lean implementation within the hospital. The research has therefore undertaken a critical study of the introduction of lean in the case study of the haematology ward at a university hospital in the south of Italy. The objective is to highlight: (a) the role of contextual factors for successful lean introduction and implementation in a hospital ward; (b) how the pilot project has improved the pathway of a cancer patient undergoing chemotherapy infusion; and, (c) how the success of the pilot project modified the contextual factors, facilitating the spread of lean within the organization.
The study has the merit of detailing all the lean introduction phases. The analysis period is about 2 years. The lean introduction started in May 2018 and lasted 7 months. The pilot project results refer to the follow-up period of December 2018 to May 2020, while the dissemination results refer to the period from December 2019 to May 2020.
The paper is structured as follows: In the following section, the theoretical background is provided. Section 3 describes the research methods, while Section 4 presents the results of the pilot project. Finally, Section 5 presents the conclusion, highlights some limitations of this study, and proposes some directions for further research.
Theoretical background
Most authors point out that the introduction phase is a crucial moment in lean implementation [ 10 , 12 , 16 ]. This phase reduces distrust of the method and organizational resistance to change. It shows the benefits of lean and assesses the organization’s ability to undertake continuous improvement. Many case studies report the success of lean in HSs by describing the use of lean instruments [ 8 , 30 , 31 ]. They offer the practitioners some methodological support, but not in a structured way since they do not provide a clear implementation roadmap [ 5 , 32 , 33 ]. Some authors have tried to fill this gap in the literature by offering guidelines for implementation. Augusto and Tortorella [ 33 ] suggests carrying out a feasibility study focused on the desired performance before implementing continuous improvement activities. The author suggests defining the techniques, roles, and results related to the improvement path. Curatolo et al. [ 5 ] argue that the improvement procedure has to take into account six core operational activities of business process improvement and five support activities. The six core operational activities are: selecting projects, understanding process flows, measuring process performance, process analysis, process improvement, and implementing of lean solutions. The five support activities are: monitoring, managing change, organizing a project team, establishing top management support, and understanding the environment. These studies, while offering further guidance on the process of introducing lean into a hospital, do not describe either the organizational context in which the method is being implemented or the strategies for its implementation [ 5 , 12 , 25 ]. The introduction of lean into a HS is not an easy task; there are many organizational issues to be addressed. Among these, the analysis of the context and the definition of the implementation strategy are the ones with the greatest impact on the success of the introduction [ 16 , 26 , 34 ].
The contextual elements are the special organizational characteristics that must be considered to understand how a set of interventions may play out [ 35 , 36 ]. They interact and influence the intervention and its effectiveness [ 34 , 36 ]. Two of the most cited contextual element are the drive to improve processes and the level of maturity [ 5 , 10 ]. The drive for improvement is represented by the exogenous and endogenous needs that act as triggers for the introduction of improvement methodologies [ 25 , 26 , 35 , 37 ]. The level of maturity refers to knowledge and experience in process improvement initiatives. It includes knowledge of methodologies and tools, experience gained, confidence, trust, and dissemination within the organization. Where the maturity is low, there is a risk of lean introduction failure in both the processes and the organization as a whole [ 5 , 16 , 38 ]. As long as the organization does not reach a fair level of maturity, the rate of change tends to be slow and sometimes frustrating. However, as the degree of maturity increases, lean implementation becomes a “day-to-day job” rather than a series of projects that take place at discreet moments [ 10 , 21 , 39 ]. Hasle et al. [ 39 ] highlighted that a high level of maturity allows for the implementation of principle-driven lean. Contextual elements include organizational and technological barriers such as resistance to change, lack of motivation, skepticism, and a lack of time and resources that inhibits the introduction and the implementation process [ 4 , 8 , 21 , 40 ]. The lean introduction process in HS is also complicated by the organizational context and the double line of clinical and management authority in hospitals [ 41 , 42 ].
With regard to internal contextual factors, many authors explored the readiness and sustainability factors influencing the adoption of lean. Readiness factors are those elements that improve the chances of lean implementation success; they provide the necessary skills and knowledge to enable organizational change [ 23 , 43 , 44 , 45 ]. The readiness and sustainability factors include any practices or characteristics that allow organizational transformation by reducing or nullifying potential inhibitors of success. High commitment and strong leadership of managers and physicians, continuous training, value flow orientation, and the hospital’s involvement in continuous improvement are just some of the most discussed topics [ 5 , 10 , 16 , 43 ]. Other examples include understanding employees needs, identifying the organization’s strategic objectives, project management, and teamwork [ 5 , 12 , 16 , 46 ].
From the study of the contextual elements described so far, some authors have developed models to assess the impact of context on the implementation of organizational improvement activities. Kaplan et al. [ 36 ] put forth the Model for Understanding Success in Quality (MUSIQ). The authors identified 25 key contextual factors at different organizational levels that influence the success of quality improvement efforts. They defined five domains: the microsystem, the quality improvement team, quality improvement support and capacity, organization, and the external environment. Kaplan et al. [ 36 ] suggest that an organization that disregards contextual factors is doomed to fail in implementing an improvement program; an organization that adopts a context-appropriate implementation strategy can change the outcome by triggering implementation enablers. Previous studies of lean adoption in HSs suggest that the fit between the approach taken and the circumstances will influence the chances of success [ 3 , 12 , 34 ].
There are two strategies for introducing lean in a HS, and they are characterized by the implementation level. The level of implementation refers to either micro or meso implementation. Brandao de Souza [ 16 ] defined meso-level implementation as the condition under which lean is spread throughout the organization and is implemented at the strategic level, while micro-level implementation is where lean is implemented at a single process level in discrete moments. Meso-level implementation is crucial for long-term success because a lack of integration in a lean system can lead to the achievement of local rather than global objectives and can also affect the sustainability of the paradigm [ 23 , 26 , 47 ]. However, organizations that want to implement lean at the strategic level often do not recognize the need for a long-term implementation program and introduce lean as a “big-bang initiative”. This leads in many cases to a failure to introduce the method [ 16 , 47 ]. Many researchers suggest introducing the lean approach through a pilot project run by a specially formed lean team [ 12 , 16 , 48 , 49 ]. The pilot project should be challenging, involve a process relevant to the organization, and require the use of a systemic approach. In particular, it should not be limited to the application of “pockets of good practice” or lean tools, but should include the systemic adoption of improvement programs such as the Plan-Do-Check-Act (PDCA) cycle [ 21 , 48 ]. Brandao de Souza [ 16 ] asserts that the first initiative should be tested on a relevant patient pathway. The lean team should be composed of clinical and non-clinical staff actively involved in the patient pathway. A pilot project that meets these conditions is a useful tool for increasing the maturity of the method within the organization [ 21 , 39 ]. It can increase the confidence of the team and staff in the lean approach and can promote the learning of lean methodologies and techniques [ 21 , 39 ]. Moreover, the pilot project activates the contextual elements, enabling the introduction of the model [ 10 , 12 ]. The successes of the pilot initiative must be celebrated and communicated within the organization [ 10 ]. When the first initiative leads to visible and easily quantifiable results, the method has a greater chance of spreading throughout the organization [ 10 , 12 , 16 ]. In light of these considerations, the lean implementation requires that the contextual elements and the introduction strategy be assessed at the same time. In addition, it would seem fair to assume that as contextual factors influence the introduction strategy, the results of the implementation strategy will influence the contextual factors.
In Fig. 1 , we propose an adaptation of the MUSIQ model [ 36 ] that shows the impact that the lean implementation strategy has on the contextual elements.
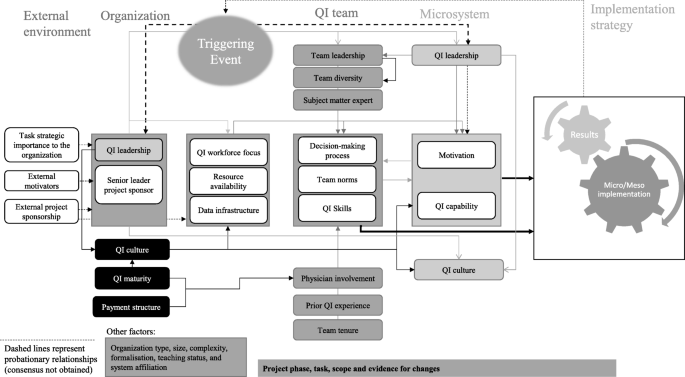
Our adaptation of the MUSIQ model
Study setting and design
This is an explanatory single-case study of the introduction of lean at a university hospital in Southern Italy. In particular, the introduction of lean in the pathway of a cancer patient undergoing infusion chemotherapy in a haematology ward will be discussed. This study was designed to evaluate how the contextual elements discussed so far have influenced the introduction of the method and how the successful pilot project has enhanced the internal context. We used the adaptation of the MUSIQ model [ 36 ] proposed in Fig. 1 to systematically trace the antecedents of the lean introduction and to explain how the success of the implementation strategy changes the contextual elements.
The work covers four periods over 2 years (Fig. 2 ). The first period concerns lean introduction and implementation strategy. The second is related to the pilot project implementation in the haematology ward. The third shows the pilot project results. The last assesses the impact of the pilot project on the dissemination of lean within the organization.
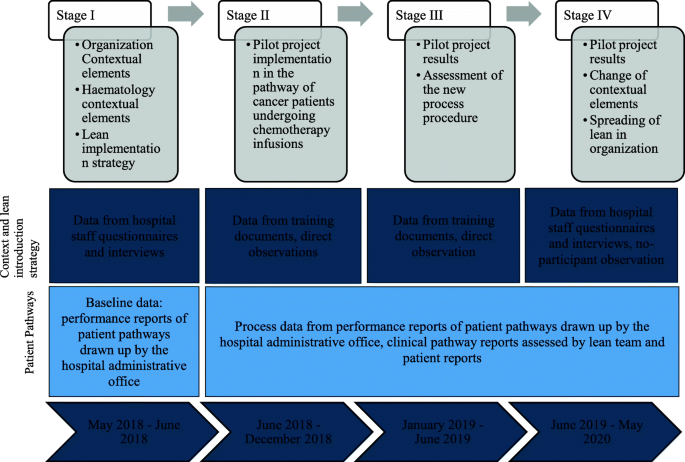
Stages of data analysis
Data collection
Different data sources and data collection methods are used with the aim of improving data validity through triangulation. The data sources are lean training documents, direct observations and nonparticipant observations, process performance reports, process data recorded by patients, and two questionnaires submitted to the hospital staff (the questionnaires assess the “pre” and “post” lean dissemination phases and the difference regards three open questions) (Fig. 2 ). The second author is the consultant who trained the lean team and coordinated the pilot project, and the first author conducted approximately 50 h of nonparticipant observations. The questionnaire was delivered to 25 medical department staff members in September 2018 and in May 2020. The first questionnaire focused on contextual factors that existed before the introduction of lean, and the second investigated changes in the contextual elements - in particular trust, maturity and lean dissemination. The semi-annual performance reports from 2017 to 2020 for the clinical pathway under examination include daily averages of the number of chemotherapies per chemo chair (MT), the patients’ length of stay (LOS), and the daily average of the percentage of patients undergoing chemotherapeutic infusion within 3 hours of hospital admission (P3). Each day, from September 2018, a document containing all the steps of the clinical pathway was given to each patient. For each activity, the patient recorded the start and end time, and a signature of the doctor or nurse was required. In the period of September 2018 – May 2020, the medical staff collected more than 1.250 reports from patients. The study also draws on 10 semi-structured interviews. The hospital CEO, the chief of the medical department, the nurse supervisor, the chief of the antiblastic chemotherapy handling units, and the chief of the clinical laboratory were interviewed in September 2018 and May 2020. The interviews focused on the contextual elements either enabling or inhibiting lean introduction or its dissemination, and ranged from 30 min to 1 hour in duration.
Data analysis
The factors described in Fig. 1 were used to systematically analyse the antecedents of the results and to understand their causal influence on the lean introduction. This data collection allows for the description of the case study. In addition, it simplifies the interpretation of the evidence that emerged through the study of the factors listed. The authors carried out a content analysis to classify the data by theme. The content analysis followed an inductive approach based on the identification of meaning units at the semantic level and the encoding of results [ 49 , 50 ]. Whenever researchers did not agree on semantic meaning, a new unit of analysis was proposed. The principle of consensus among all panel members was used to determine the interpretation, addition or deletion of elements of analysis. The discussion of the case study focuses on four themes: (a) contextual elements enabling or hindering lean introduction, (b) implementation strategy, (c) pilot project results, and (d) lean dissemination and adoption in hospital. These themes were submitted for review by the interviewees; their feedback was used to improve the accuracy of the case study description.
Case study presentation
The university hospital is a model of excellence in Italy for pre-clinical, translational, and clinical research and care activities. It is equipped with 110 beds to treat all types of oncological pathologies in adults. There are 115 researchers working there. The hospital is structured into six departments, of which three are clinical (Medical Area, Diagnosis and Imaging Therapy, Surgical Area), two are services, and one is an administrative/management department. The medical area includes four wards: medical oncology for thoracic pathology, medical oncology, haematology, medical oncology for oncology patient care. In 2015, the institute was accredited as a clinical cancer centre according to the Organization of European Cancer Institutes (OECI). Since 2015, evidence-based medicine and patient-centred care methodologies have been successfully implemented in the hospital, but no process improvement methodology has been used. In 2017, the hospital became a hub for oncological diseases, which led to an increased demand for care and services. The hospital has received national funds dedicated to hubs and has made investments in infrastructure improvements and the purchase of new innovative medical equipment.
Contextual factors enabling or hindering lean introduction
The description of the external and internal contextual factors, as revealed in the first questionnaire and the interviews, is given in Table 1 . Below is a brief description of each item.
External context and organizational elements driving lean introduction in the haematology ward
The analysis of the context revealed external and internal elements influencing the introduction of lean. Starting with the external elements, the most frequently discussed motivators that led to the search for methodologies for process improvement include the continuous increase in patient volume and the benchmark of process performance with other providers. Although the clinical results were above the national average, the increase in demand - especially in the medical area - highlighted the inability to manage the increasing flow of patients. The inability to manage the increasing number of patients also affected the performance of the process in the diagnostic area.
Internal elements driving the lean introduction were related to dissatisfaction with inefficient work practices within the medical area and the dissatisfaction of many patients who complained about long wait times and lengths of stay.
The choice of lean methodology derives from the desire to follow the example of certain Tuscan hospitals that have been using lean at a strategic level since 2015. These hospitals are considered the benchmark for continuous process improvement. One of these hospitals was already included in the 2013 OASI Report, edited by CERGAS - Bocconi, among the six Italian companies that were the first and best to successfully implement Lean Thinking in healthcare. In addition, the methodology was strongly sponsored by the clinical director and the general director of the hospital. They had participated in a 60-h regional training course on lean healthcare in the second half of 2017. During the training course, they studied case studies of excellence in lean implementation.
When, in May 2018, the hospital directorate proposed the introduction of lean methodology in the medical area, the head physicians showed strong resistance because of the resources that would need to be allocated to the implementation process. In addition, some doctors did not trust the method. This brought up some conflicts with the medical area managers. The haematology staff, represented by their head physician, were the only ones who explicitly agreed to implement the lean introduction. The department, as in most Italian hospitals, is structured as a clinical area where the physicians - in contrast to other professionals - were members of the ward organizationally. Haematology staff were strongly motivated to do research and achieve excellent process performance. They were interested in taking the opportunity to define excellent clinical pathways, as the ward was undergoing managerial and layout restructuring. In addition, the haematology staff believed that lean could further improve clinical performance and improve the patient-centred and evidence-based approach. Until mid-2017 the ward was part of oncology; afterward, it was made independent and new areas of the hospital were assigned to it. Since the ward became independent, one head physician, three doctors and four nurses have been hired. The department is equipped with the most modern medical equipment. The layout of the ward was not yet fully defined, and some rooms that could have potentially been assigned to medical, diagnostic and therapeutic activities had not been assigned to process activities. The ward shares the Antiblastic Chemotherapy Handling Unit (UMACA) and the analysis laboratory with the other four medical department wards in the hospital, so the staff needed to coordinate clinical processes so as not to create bottlenecks.
Since haematology is a strategic ward for the hospital, and in the last 2 years the demand for treatment has increased more than in other wards, the managers of the medical area have deemed it appropriate to introduce lean there. Haematology ward is considered strategic due to its high attractiveness and high immigration rates of patients from outside the region. These phenomena derive from the excellent reputation of the department in relation to the quality of care. Although the clinical pathways were characterized by excellent clinical outcomes, qualitative benchmarking activities (based on testimonials from physicians and patients) showed that the organization of the haematology patient pathway was very different compared to the benchmark (a Tuscan hospital) and that the patients’ perception of non-clinical service quality was lower. Although no investigation was carried out with respect to the ratio of equipment and personnel available per number of patients and amount of activities regarding the hospitals taken as benchmarks, the testimonials prompted management to come up with new specific, measurable, attainable, relevant and time - bound (SMART) goals (Table 2 ). The goals will be described in the next section.
Internal contextual elements enabling and hindering lean introduction in the haematology ward
At the organizational level, hospital management has strongly supported the introduction of the method. Since the haematology staff had no experience in process improvement activities, management provided the budget for an external consultant. In addition, three non-clinical personnel were allocated part-time to support the implementation of visual management systems and communication. The organizational structure of the ward has been modified to a matrix form. A team of three haematology ward physicians and two nurses was established and the ward’s head physician was elected project manager. The project manager had formal authority over the team and the personnel employed in the process to be improved; this reduced conflicts due to the double line of hierarchical authority. In this phase, the top-down decision-making approach was crucial to the successful restructuring of the organizational structure and the definition of the new organizational roles. The lean advisor supported the group for 8 months through training and project supervision. He coordinated two meetings per week and carried out Kata coaching activities. The theoretical training activity, lasting 5 week ends (in June 2018), was differentiated to accommodate technical and managerial competency needs. The team project manager and the medical area manager were trained on topics such as project management, team management, leadership, and the dissemination of lean. The members of the lean group were trained in lean techniques and tools. The key principles of lean thinking, the PDCA cycle methodology and lean assessment were taught to all participants. The most difficult barrier to overcome was the time available. The team agreed to spend 8 hours per week on training and pilot project implementation. The management of the team was facilitated by the experience gained with the implementation of the patient-centred care and evidence-based medicine. The motivation of the medical staff–microsystem element–and the focus on team management were key success factors for the involvement of team members. The culture of change introduced by patient-centred and evidence-based medicine was another enabling factor.
Implementation strategies
Pilot project definition.
Hospital managers and lean team members, who had experience in implementing patient-centred care methodologies, suggested starting a pilot project for the lean introduction. The consultant agreed. The team, with the support of the expert, analysed the clinical pathways in haematology. Six pathways emerged: a) diagnostic visits, b) biopsies, c) check-up visits, d) transfusions, e) infusion chemotherapies, and f) oral chemotherapies. Hospital managers argued that the pathway of the patient undergoing infusion chemotherapy was the most critical for patient and organization value. This process is the only one that involves several departments and requires a large amount of materials and time-consuming resources. In the first and second half of 2017 and 2018, there was a significant increase in the number of chemotherapeutic preparations. LOS, P3, and MT performance decreased during the same periods (Table 2 ). In addition, outpatient visits and the number of biopsies also increased. The medical staff stated that the increase in demand in the medical area had particularly affected the infusion therapy activities because they involved technical and instrumental resources that are shared with other departments (Table 2 ). The length of stay was analysed for patients undergoing short (LOS s ) and long-term infusion (LOS l ) chemotherapy. The first has a minimum duration of 90 min and a maximum of 180 min, and the second has a minimum duration of 181 min and a maximum of 360 min. Each patient was assigned to one of the infusion treatment classes. Process data were collected and analysed by the Department Management Control Office. The process performance data collection and reports were established in 2015 for the implementation of evidence-based medicine.
Pilot project implementation
The pilot project started in June 2018. The first month was dedicated to Gemba Walk, Methods-Time Measurement (MTM) and implementation of the 5S. In addition, the consultant trained the project manager, department managers and lean team members. There were many difficulties during the training period, especially with regard to process mapping and the concept of value, the latter being interpreted by doctors as clinical output. The non-medical staff dedicated to the project assisted the team in the drawing of the visual management material. A room in the medical department was dedicated for team meetings, and some notice boards were installed to post the materials developed during the project. The project activities were organized according to the Report A3 scheme. It followed the phases of the consolidated Deming cycle: Plan-Do-Check-Act (PDCA). Implementing the approach proposed by Deming allowed for the trial-and-error empirical method to be abandoned in favour of the “scientific” one. The PDCA allowed accurate planning of objectives and activities and their monitoring. The departmental managers and the consultant through the study of the national publications and explicit requests to colleagues in other hospitals - considered virtuous - identified the benchmark (Table 2 ). They took into account the hospital’s specific characteristics, such as the policy of not accepting haematochemical reports from outside for fragile patients. This choice is dictated by the risk management plan and affects P3 and MT performance. Time for blood sampling and haematochemical analysis is added to the cycle time; however, it eliminates many risks associated with clinical treatment.
The existing care process was mapped through Value Stream Mapping (VSM) based on the patient reports, Gemba walks, interviews, and direct observation. For instance, Fig. 3 shows the pathway of a patient undergoing short-term infusion chemotherapy. The cycle time in Fig. 3 was calculated over an observation period of 1 week and included 51 patients. In addition, the application of the Demand Map and the Spaghetti Chart were used to evaluate the ward nodes activated by the patients and the ward’s layout. These tools were useful in defining the possible sources of waste in the process. The application of these tools lasted more than 2 months and required several revisions. Once completed, the results were posted in the meeting room and were used for discussions with colleagues in the medical department. The lean team requested support from the consultant for the drafting of the VSM and for the layout analysis. In addition, the consultant was asked to simplify negotiations with staff from other departments who were reluctant to be subjected to time and method measurements. The negotiation activity required a degree of organizational effort. The facilitating elements were manifold: they enabled the involvement of staff opposed to the introduction of measuring instruments. In particular, the most effective were: the intervention of the directorate general, the delegation of hierarchical authority to the project manager and finally the endorsement of trade union committees. Moreover, during the planning phase, many difficulties emerged, including the selection of a unique and standardised measurement system, the coordination of work and meeting schedules, and the deadlines set by the project Gantt. Although the project manager was able to manage the team, he did not have enough experience in lean tools. The external consultant played a key role in managing these activities.
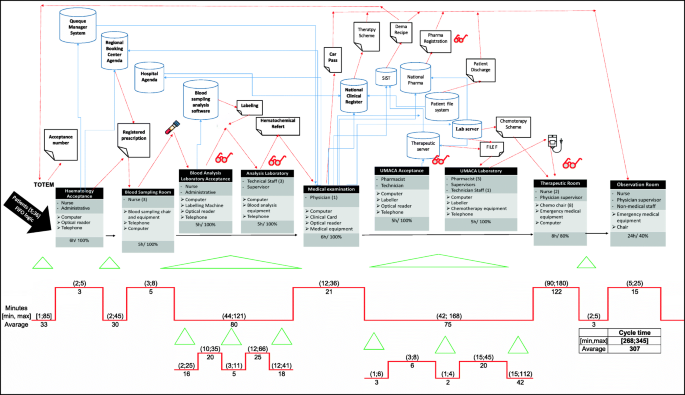
As-is process represented by VSM
At the end of the as-is analysis process, an Ishikawa diagram was used for the definition of root causes. Four root causes emerged from the meetings and interviews. They were patient flow management, coordination activities with other departments, layout, and Information Technology equipment (IT).
Patient flow management concerned the absence of priority in the management of patients based on the clinical path and the arrival of patients in the early hours of the morning. The lack of coordination with other departments led to delays in the preparation of infusion chemotherapy and blood test reports. The layout was such that the flow of doctors and nurses crossed the flow of patients, and this caused great inconvenience to the doctors and nurses. Also, the computer software was not compatible, which meant that the same data had to be recorded several times.
After some meetings and rigorous brainstorming, the lean team suggested changes to be made in the existing pathway. This was done by considering how patients could be divided into clusters so that the infusion activity could start as soon as possible without affecting other occurrences. Moreover, it is made possible to simplify the coordination between diagnostic units. The patient flow has been managed in such a way that long-term patients are given priority (first to be accepted and blood sampled), followed by patients needing biopsies, first visit, follow-up visit. Finally, short-term patients are treated in a way that limits waiting time and does not affect the activities of other departments. Theories of queues and operational research methodologies were implemented to address chemo chair saturation. A chemo chair activities plan was implemented through pull logic. In addition, the hospital engineer was involved in making sure the information systems were compatible. Whenever integrating the software was not possible, a data entry person was assigned to prevent medical staff from wasting their time on low-value activities. The ward layout has been modified to prevent patient flows from intersecting with the flows of doctors and nurses. In addition, the use of one room has been changed from a small warehouse to a blood collection room to increase the value of the activities carried out within it. The waiting rooms were moved outside the ward and, during the first 2 hours of the working day, the biopsy room was reassigned to blood collection activities to speed up the requests for therapies in UMACA. Patient intake, blood collection, and tube labelling activities have been paralleled to be performed simultaneously in the same room. The routes and modalities for the delivery of blood samples to the laboratories were revised in order to reduce the time and distance travelled by non-clinical staff. Tablet reporting systems were installed. Finally, a patient chemo chair allocation system was developed.
The resources needed for these changes were determined. The team tested and modified the changes during December 2018 and January 2019. The tests were evaluated based on the performance data, patient reports and the team’s expertise.
Pilot project results
In January 2019, it was decided to implement the new standard procedures that were tested in order to improve performance. The team met once a week for 6 months. On a monthly basis, performance was reviewed and new changes were tested. Clinical and nonclinical personnel from other wards and departments were invited to each weekly meeting to share with them the results of the pilot project, and to involve them in the lean methodology.
Every morning, the team leader investigated the impact of organizational changes in order to avoid conflicts. Organizational problems that emerged were discussed and resolved by consensus. In the follow-up phase, the consultant performed supervisory activities. Each week, the team leader performed the Kata coaching. During the first 6 months, the monitoring of activity was very frequent to prevent a return to old operating modes. Subsequently, when the staff had learned the new procedures, monitoring was reduced to once a month.
Table 2 and Fig. 4 shows the results achieved through the implementation of the pilot project. The objectives were not reached for all indicators; however, the results improved over time.
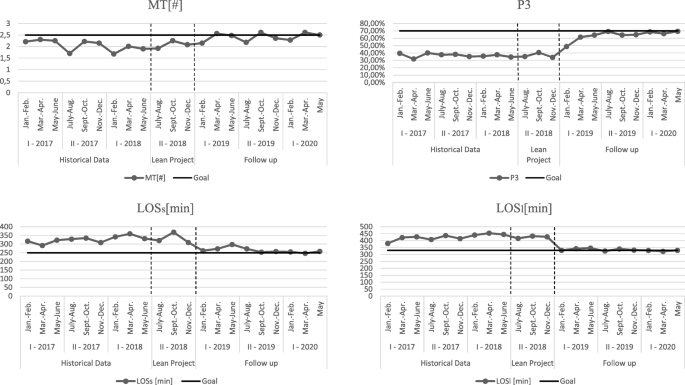
Figure 5 shows the to-be state of the same process analysed in Fig. 3 . From the cycle time analysis of each process step, the areas of waste eliminated are clear.
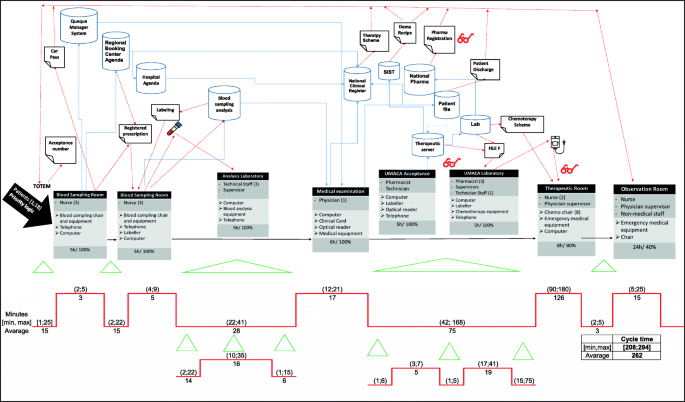
To-be process represented by VSM
The incremental improvements in process performance over time are explained by the need for staff to learn new procedures in the early period. In addition, the patients’ resistance to changing their habits also slowed down the improvement in performance. Patients have been educated over time, through an intense communication activity based on visual management systems and telephone reminders.
In addition to the results showed in Table 2 , the pilot project had a positive impact on the performance of other patient pathways in the medical department. The cycle time variability reduction and the levelling of the service demand allowed the UMACA and the analysis laboratory to better plan their activities. The new layout reduced waste due to unnecessary movement. Nurses walk 2 km less per day and doctors 1.5 km less per day. Software integration has reduced data logging time by 35 min per day for each doctor. Patients have evaluated the change positively. In particular, they have experienced a drastic reduction in wait times, and greater attention from the medical staff. Increased privacy and a precise time of service are other improvements reported by patients.
Finally, the clinical staff was satisfied with the new procedures because they reduce overloads and allowed for better planning of activities. They say that dividing patients into time slots based on clinical priority reduces stress and simplifies the coordination of activities with other departments. The success of the project was communicated internally and externally to the organization. In June 2019 the results were celebrated with a formal team award ceremony. The resulting Report A3 was posted on the bulletin boards in the hospital wards and in the reception area. By means of an internal circular sent to all medical directors, the directorate officially thanked the members of the lean team and highlighted the excellent results achieved in terms of waiting lists and process time reduction. In addition, the directorate funded the lean team’s participation to national conferences in order for the team to discuss the project. The improvement activities and results were described and summarized in an official report sent to the regional health authority and cancer patient associations (the latter were also given an evaluation form and an invitation to observe the optimised process in the field). Reporting was carried out by the hospital directorate and the project manager.
Lean dissemination and adoption in the hospital
Following several meetings between the directors and the primary doctors of the medical area, it became clear that there was a willingness to implement further improvement projects in other medical wards. The feedback from the pilot project team was a strong convincing factor. Moreover, the results of the external communication of the pilot project played a critical role in increasing the desire for emulation. The regional authorities requested for the project team to co-design the diagnostic and therapeutic care pathways (PDTA) of the haematology patient pathway inside the regional network. The patient association lobbied for similar projects to be implemented in other clinical oncology pathways. The change of internal context and enabling factors were of great importance at this stage. The drive to disseminate lean was characterized by both the need to improve process performance and to the desire to emulate the success of the project pilot. In addition, increased trust in the lean method has prompted the directors to provide a peer internal training program in the medical area. In June 2019, members of the pilot project lean team were promoted to the position of lean champions. Their role was to disseminate the lean methodology in the medical area and to train colleagues. The hospital directorate set up the Lean Support Office and assigned to it the three non-clinical resources that had already supported the pilot project. The first methodology to spread throughout the medical department was 5S. According to the lean sponsors, this methodology was a prerequisite for implementing lean methodologies in all wards and for facilitating inter-process lean implementation. Visual management systems have been implemented to facilitate changes and standardization of activities and to guide the patient through the hospital. The 5S methodology and visual management, which was initially underestimated by the medical staff, has solved many problems in the working environment. Increasing the availability of tools, simplifying the transmission of documentation, reducing errors in medical records and nursing diaries, reducing the duplication of requests and medical documentation, creating flexible workplaces, less movement and transportation in the hospital, and increasing patient autonomy are just some of the improvements achieved. However, the most important result to be achieved was an improvement in workplace wellbeing. Among the most used tools for 5S implementation and visual management are: checklists, one point lessons, kaizen forms, horizontal and vertical marking, red tags, Kanban, spaghetti charts. Finally, the demand map was implemented to trace the patient flow across the departments of the medical area and the vertical swim lanes and the resources/process matrix were utilized to identify staff involved in several processes and the potential bottlenecks (in addition to the UMACA and the blood chemistry laboratory). As of August 2019 many other lean projects have launched sometimes spontaneously and sometimes at the demand of department heads or project managers (Fig. 6 ). In August 2019, three projects were undertaken in the medical oncology for thoracic pathology and the medical oncology wards. Two of them concerned the same clinical pathway addressed in the pilot project, and the last one was the harmonization of protocols for caring for an oncological patient between departments. Each project has been implemented following the PDCA cycle (using the A3 report framework) with the support of one of the lean champions, who was assigned the role of project manager. Teams of three doctors and one nurse were dedicated to each project. In the planning phase, the tools adopted in each project were: spaghetti charts, VSM, Gemba Walk, standardized data collection sheets (both for patients and physicians), control charts, 5 Why or alternatively the Fishbone Diagram, definition of SMART objectives. In the “Do” phase, the solutions adopted for the resolution of problems are derived from Just in Time and agile approaches (especially for software’s’ integrations management). The pilot project A3 report was used as a knowledge management tool and resulted to be of great value to guide the implementation of the three projects. The members of the pilot project team supported their colleagues during the implementation of the three projects. This resulted in a positive impact on the quality and timing of the data collection activities, the drafting of the VSM, the definition of the KPIs and especially the root cause analysis. Even though the negotiation was simplified by peer training, support from more experienced colleagues and project management by a doctor, organizational and structural barriers emerged. The difficulty in getting the new procedures accepted, the impossibility of optimizing the layouts and the “not always respecting” the authority of the project manager limited the performance improvement. Although not all potential solutions have been implemented, the results obtained are evidence of the success of the projects.
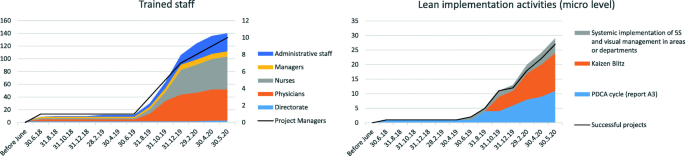
Lean projects and dissemination activities
In September 2019 the diagnostic department started 5S and visual management implementation initiatives. In October 2019 the same initiatives were undertaken in the surgical department. These initiatives were spontaneously implemented. The managers of these departments have asked the hospital director to introduce lean in their departments. Given the maturity of the method and the number of doctors trained, hospital managers did not consider it possible to undertake systemic improvement pathways in all departments. However, they have changed the organizational structures of the departments into matrix structures. Two doctors with lean experience, per department, have been assigned the role of project manager. The project managers have sponsored peer training and Kaizen blitz activities throughout the hospital departments. In the period October to December 2019 more than 60 doctors and nurses were trained in 40-h courses by their colleagues (Fig. 6 ). Three Kaizen blitz projects in the diagnostic department and two Kaizen blitz projects in the surgical area were carried out (Fig. 6 ). In addition, a PDCA cycle project was implemented in the medical area for the stocking and tracking of drugs and instruments. Moreover, the two bin Kanban systems, drug tracking tools, optimisation of the position in the storage layout and systems for the analysis of consumption time series were implemented.
In December 2019, in all the departments discussed so far, doctors were involved in continuous improvement activities, with projects structured through the use of both PDCA cycle and Kaizen blitz. The activities were undertaken spontaneously without the supervision of a manager and without any impact on daily clinical activity. The maturity of the methodology, the support of colleagues, and trust were enabling elements. However, some barriers such as infrastructural constraints and coordination of doctors and nurses and information systems have frequently affected the implementation of the method and two projects failed.
Due to the success of implementations at the micro level, managers have attempted to implement the lean methodology at the meso level. Hospital managers discussed, formalized and communicate in organization the Lean Strategic Plan. In January 2020, the Lean Support Office was transformed into a lean projects control room and renamed as the Operations Management Office. The role of this office is to define lean development policies and to supervise continuous improvement activities. The office has been placed in line with the strategic direction. Two lean project managers, two hospital managers, and three administrative officers have been assigned to it. Lean assessment, to evaluate the degree of lean maturity in organization, and Honshi Kanri, to strategically govern change activities, were implemented to the organizational level. While the lean assessment revealed an increase in both advance in the use of lean tools and the principles behind them, the governance of strategic implementation through Honshi Kanri did not seem to provide the foreseen results. Operations management office project managers did not always agree with hospital directorate on project prioritization. In addition, there often were disagreements between the Operations Management Office staff and departmental project managers about when to launch a project and how to manage it and communicate project results. Although there were many process improvement projects underway, these have not always been decided harmoniously between the Operation Management Office and the hospital departments. Moreover, many projects undertaken spontaneously by lean teams were not communicated to the Operations Management Office, which was therefore unable to govern the dissemination of the method. Medical leadership in departments seemed to dominate over managerial leadership; thus, there is great difficulty in strategically governing continuous improvement.
The marked differences in the responses to the closed questions of the questionnaires submitted provide significant evidence of how lean has spread throughout the organization (Fig. 7 ).
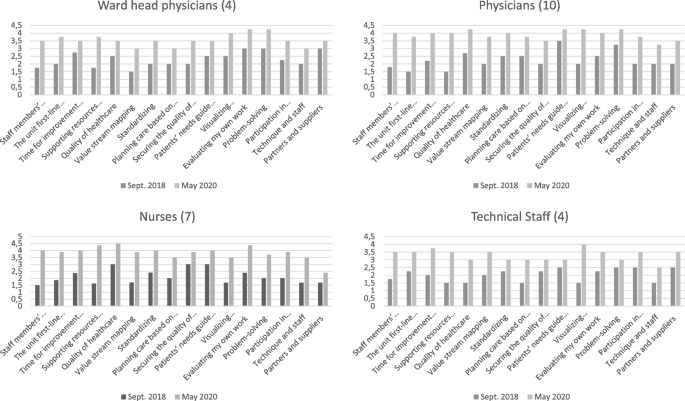
Responses to the closed questions of the questionnaire
The marked differences in the responses to the closed questions of the questionnaires presented provide significant evidence of how lean has spread throughout the organization. In particular, the results show how standardisation, self-assessment, time for improvement and peer-to-peer training have become part of everyday working practice. Furthermore, problem solving and collaborative decision-making show significant improvements. These improvements were witnessed not only by management but also by doctors, nurses and technical staff in the medical area.
After the pilot project and the initial push for implementation by management, internal contextual factors changed radically within the organization. While initially sponsorship and management involvement were necessary for lean implementation, today the methodology is independently disseminated. In particular, small improvement groups have emerged that are able to address various challenges. Process vision and patient focus have become part of the hospital culture. Doctors claim that continuous improvements simplify daily work, save time, and increase the level of service and the number of services provided. However, although these changes occurred at the micro level, the organization failed to direct change at the strategic level. Thus, harmonization of lean projects according to the strategic direction of the facility has yet to be achieved.
In accordance with the findings of many researchers [ 10 , 16 ], this case study showed how a careful, context-driven lean introduction strategy facilitated the dissemination of lean - at micro level - within the hospital. The decision to implement lean was precipitated by external factors, including the need to improve the performance of processes in the medical area and to follow the example of other successful hospitals. The in-depth training by an external specialist and the pilot project, characterized by interdepartmental activities, the need for a systemic approach based on the Deming Cycle and the constant support of the external consultant, allowed the participants to acquire the necessary skills to support - sufficiently - the lean implementation in the clinical pathways of the medical department and to train their colleagues. The results of this project have been manifold. At the process level, there was a significant reduction in the patients’ length of stay, the wait times for haematological patients, the process time variability, and an increase in the number of daily chemotherapy therapies performed. At the medical area level, a spontaneous spread of the culture of improvement has emerged. Directorate commitment, motivation of the medical department staff and management, and the presence of a consultant were the main enabling factors for the success of the pilot project. In turn, the results of the pilot project were the trigger for the spread of lean in the hospital. The pilot project itself, and the changes made to standard procedures that were inspired by the intervention, altered the contextual elements, mirroring the MUSIQ model [ 18 , 26 , 36 ]. Moreover, as trust and maturity raised, the speed of lean dissemination increased. This confirms that knowledge of the lean method tends to reduce organizational barriers and resistance [ 5 , 21 , 51 , 52 ]. Kata training and coaching were other key elements for the dissemination of the methodology. Initially, the consultant carried out the training activity, and after the pilot project, the team members became trainers and project managers; in this way, lean spread in the organization spontaneously. Moreover, as stated by many researchers [ 12 , 21 , 46 ], the matrix structure and project managers helped the staff to support and better coordinate process improvement. The many projects activated in the period July 2019–March 2020 are the measure of the diffusion itself.
However, some issues have arisen. For the new working procedures, the willingness of and the acceptance by the staff is crucial to achieving and sustaining the results of lean initiatives; where this did not occur, conflicts arose and the speed of change slowed. In addition, although in the early stages of implementation the bottom-up approach must prevail over a top-down approach to facilitate consensus and trust among physicians, nurses, and all workers, during the dissemination phase a greater equilibrium between the two decision-making approaches must be achieved. In accordance with [ 2 , 5 , 10 ], this case study demonstrates the importance of the right balance between bottom-up and top-down approaches. Medical leadership tends to dominate managerial leadership such that continuous improvement, even though it takes place in clinical processes, does not follow the strategic organizational guidelines. This leads to conflicts between managers and medical staff. Organizational, technical and infrastructural obstacles have hindered the adoption of the methodology. It is clear from what has been found that the introduction strategy was correct, but that the implementation at the strategic level has not yet taken place. The context has changed considerably from an organizational point of view, but some barriers have not been overcome. The management, which strongly sponsored and supported the introduction and implementation of lean, was subsequently unable to guide the implementation at the strategic level.
Our adaptation to the MUSIQ model is useful for interpreting the relationship between lean introduction strategies and changing contextual elements. Looking backward through this model allows us to understand the links between contextual elements, lean implementation and outcomes.
Conclusions
This study revealed that the strategy of introducing lean has improved readiness, sustainability and confidence in the method within the organization. The growing maturity of the organization has encouraged lean dissemination. However, the choice of strategy depends heavily on contextual factors. The two factors, therefore, influence each other. Although the introduction strategy may facilitate the introduction of lean, it may be less important when certain organizational, technical and infrastructural barriers remain. This is particularly relevant for systemic implementation. Contextual elements, which changed over time, influenced the success of the implementation at micro-level. At the meso-level, however, the organization has not reached the maturity for a systemic implementation of the method.
As has already been shown in the literature, the determining factors for introducing the methodology refer to external and internal pressures. The level of commitment of both the leadership and management are decisive for the success of the implementation only if the staff is motivated. Furthermore, the analysis shows that managing lean implementation at the micro and meso-levels requires different types of efforts. While the level of maturity speeds up the adoption of lean at the clinical level, it is not true that the dissemination of lean at the operational level inevitably translates into its application at the strategic level. Medical leadership, reinforced by the success of lean project implementations, could instead undermine proper implementation at the meso-level. This experience strengthens the MUSIQ model and complements it by showing the importance of the lean introduction strategy and its impact on contextual factors.
Limitations and future research
The main limitations concern the complexity of detecting and analysing all the relevant social and organizational aspects that have characterized the introduction and dissemination phases and the observation period of the dissemination phase. Moreover, the expert content analysis could introduce opportunities for misinterpretation of the data. The relationship between the contextual elements and the pilot project results were mainly assessed through participant and patient reports, document studies, and observations. The authors used data triangulation and a review of hospital staff to overcome the limits of the content analysis. Given the specificity of the hospital’s contextual factors and strategic choices, it is also clear that the case study cannot be generalized.
The sustainability aspect of lean was not considered because the observational study was conducted over a period of only 2 years. To understand this issue, the authors will investigate the socio-technical aspects of lean and how the context supports continuous improvement over time.
Availability of data and materials
The datasets used and/or analysed during the current study available from the corresponding author on reasonable request.
Abbreviations
Hospital Setting
Information Technology
Length of stay
Number of chemotherapies per chemo chair
Methods-Time Measurement
Model for Understanding Success in Quality
Organization of European Cancer Institutes
Patients undergoing chemotherapeutic infusion within three hours of hospital admission
Plan-Do-Check-Act
Antiblastic Chemotherapy Handling Unit
Value Stream Mapping
Godman B, Novakovic T, Tesic D, Oortwijn W, Martin AP, Parker M, et al. Addressing challenges for sustainable healthcare in central and Eastern Europe. Exp Rev Pharmacoecon Outcomes Res. 2016;16(6):685–7. https://doi.org/10.1586/14737167.2016.1165610 Epub 2016 Mar 30. PMID: 26966924 .
Article Google Scholar
Teisberg E, Wallace S, O’Hara S. Defining and implementing value-based health care: A strategic framework. Acad Med. 2020;95(5):682–5. https://doi.org/10.1097/ACM.0000000000003122 PMID: 31833857; PMCID: PMC7185050.
Article PubMed Google Scholar
Lum B, Png HM, Yap HL, Tan C, Sun B, Law YH. Streamlining workflows and redesigning job roles in the theatre sterile surgical unit. MJ Open Qual. 2019;8(3):e000583. https://doi.org/10.1136/bmjoq-2018-000583 .
Radnor Z, Holweg M, Waring J. Lean in healthcare: the unfilled promise? Soc Sci Med. 2012;74(3):364–71. https://doi.org/10.1016/j.socscimed.2011.02.011 .
Curatolo N, Lamouri S, Huet J, Rieutord A. A critical analysis of lean approach structuring in hospitals. Bus Process Manag J. 2014;20(3):433–54. https://doi.org/10.1108/BPMJ-04-2013-0051 .
Roemeling O, Land M, Ahaus K. Does lean cure variability in health care? Int J Oper Prod. 2017;37(9):1229–45. https://doi.org/10.1108/IJOPM-07-2015-0452 .
Chiarini A, Bracci E. Implementing lean six sigma in healthcare: issues from Italy. Public Money Manag. 2013;33(5):361–8. https://doi.org/10.1080/09540962.2013.817126 .
Parkhi SS. Lean management practices in healthcare sector: a literature review. Benchmarking. 2019;26(4):1275–89. https://doi.org/10.1108/BIJ-06-2018-0166 .
Joosten T, Bongers I, Janssen R. Application of lean thinking to health care: issues and observations. Int J Qual Health Care. 2009;21(5):341–7. https://doi.org/10.1093/intqhc/mzp036 .
Article PubMed PubMed Central Google Scholar
Womack JP, Jones DT. Lean consumption. Harv Bus Rev. 2005;83(3):58–68 148. PMID: 15768676 .
PubMed Google Scholar
Spear SJ. Fixing health care from the inside, today. Harv Bus Rev. 2005;83(9):78–91 158. PMID: 16171213 .
D’Andreamatteo A, Iannia L, Lega F, Sargiacomo M. Lean in healthcare: a comprehensive review. Health Policy. 2015;119(9):1197–209. https://doi.org/10.1016/j.healthpol.2015.02.002 .
Mazzocato P, Holden RJ, Brommels M, Aronsson H, Bäckman U, Elg M, et al. How does lean work in emergency care? A case study of a lean-inspired intervention at the Astrid Lindgren children’s hospital, Stockholm, Sweden. BMC Health Serv Res. 2012;12(28). https://doi.org/10.1186/1472-6963-12-28 .
Andersen H, Røvik KA. Lost in translation: a case-study of the travel of lean thinking in a hospital. BMC Health Serv Res. 2015;15(401). https://doi.org/10.1186/s12913-015-1081-z .
Goodridge D, Westhorp G, Rotter T, Dobson R, Bath B. Lean and leadership practices: development of an initial realist program theory. BMC Health Serv Res. 2015;15(1):362. https://doi.org/10.1186/s12913-015-1030-x .
Brandao de Souza L. Trends and approaches in lean healthcare. Leadersh Health Serv. 2009;22(2):121–39. https://doi.org/10.1108/17511870910953788 .
Ulhassan W, von Thiele SU, Thor J, Westerlund H. Interactions between lean management and the psychosocial work environment in a hospital setting - a multi-method study. BMC Health Serv Res. 2014;14(1):480. https://doi.org/10.1186/1472-6963-14-480 .
Kaplan HC, Brady PW, Dritz MC, Hooper DK, Linam WM, Froehle CM, et al. The influence of context on quality improvement success in health care: a systematic review of the literature. Milbank Q. 2010;88(4):500–59. https://doi.org/10.1111/j.1468-0009.2010.00611.x .
Nelson-Peterson DL, Leppa CJ. Creating an environment for caring using lean principles of the Virginia Mason production system. J Nurs Adm. 2007;37(6):287–94. https://doi.org/10.1097/01.NNA.0000277717.34134.a9 .
Mazzocato P, Savage C, Brommels M, Aronsson H, Thor J. Lean thinking in healthcare: a realist review of the literature. Qual Saf Health Care. 2010;19(5):376–82. https://doi.org/10.1136/qshc.2009.037986 Epub 2010 Aug 19. PMID: 20724397 .
Brandao De Souza L, Pidd M. Exploring the barriers to lean health care implementation. Public Money Manag. 2011;31(1):59–66. https://doi.org/10.1080/09540962.2011.545548 .
Kaplan GS, Patterson SH, Ching JM, Blackmore CC. Why lean doesn’t work for everyone. BMJ Qual Saf. 2014;23(12):970–3. https://doi.org/10.1136/bmjqs-2014-003248 Epub 2014 Jul 23.
Al-Balushi S, Sohal AS, Singh PJ, Al Hajri A, Al Farsi YM, Al AR. Readiness factors for lean implementation in healthcare settings--a literature review. J Health Organ Manag. 2014;28(2):135–53. https://doi.org/10.1108/JHOM-04-2013-0083 .
Article CAS PubMed Google Scholar
Henrique DB, Filho MG. A systematic literature review of empirical research in lean and six sigma in healthcare. Total Qual Manag Bus Excell. 2020;31(3–4):429–49. https://doi.org/10.1080/14783363.2018.1429259 .
Coles E, Wells M, Maxwell M, Harris FM, Anderson J, Gray NM, et al. The influence of contextual factors on healthcare quality improvement initiatives: what works, for whom and in what setting? Syst Rev. 2017;6(1):168. https://doi.org/10.1186/s13643-017-0566-8 .
Kaplan HC, Froehle CM, Cassedy A, Provost LP, Margolis PA. An exploratory analysis of the model for understanding success in quality. Health Care Manag Rev. 2013;38(4):325–38. https://doi.org/10.1097/HMR.0b013e3182689772 .
Tay HL, Singh PJ, Bhakoo V, Al-Balushi S. Contextual factors: assessing their influence on flow or resource efficiency orientations in healthcare lean projects. Oper Manag Res. 2017;10(3–4):118–36. https://doi.org/10.1007/s12063-017-0126-3 .
Hussain M, Malik M. Prioritizing lean management practices in public and private hospitals. J Health Organ Manag. 2016;30(3):457–74. https://doi.org/10.1108/JHOM-08-2014-0135 PMID: 27119397 .
Fournier PL, Jobin MH. Understanding before implementing: the context of lean in public healthcare organizations. Public Money Manag. 2017;38(1):37–44. https://doi.org/10.1080/09540962.2018.1389505 .
Chiarini A. Risk management and cost reduction of cancer drugs using lean six sigma tools. Leadersh Health Serv. 2012;25(4):318–30. https://doi.org/10.1108/17511871211268982 .
Gonzalez ME. Improving customer satisfaction of a healthcare facility: reading the customers’ needs. Benchmarking. 2019;26(3):854–70. https://doi.org/10.1108/BIJ-01-2017-0007 .
Terra JDR, Berssaneti FT. Application of lean healthcare in hospital services: a review of the literature (2007 to 2017). Prod. 2018;28(0):e20180009. https://doi.org/10.1590/0103-6513.20180009 .
Augusto BP, Tortorella GL. Literature review on lean healthcare implementation: assessment methods and practices. Int J Serv Oper Manag. 2019;32(3):285–306. https://doi.org/10.1504/IJSOM.2019.10019746 .
Fournier PL, Jobin MH. Medical commitment to lean: an inductive model development. Leadersh Health Serv. 2018;31(3):326–42. https://doi.org/10.1108/LHS-02-2018-0015 Epub 2018 Jul 3. PMID: 30016920 .
Improta G, Romano M, Di Cicco MV, Ferrero A, Borrelli A, Verdolina C, et al. Lean thinking to improve emergency department throughput at AORN Cardarelli hospital. BMC Health Serv Res. 2018;18(1):265–78. https://doi.org/10.1186/s12913-018-3654-0 .
Kaplan HC, Provost LP, Froehle CM, Margolis PA. The model for understanding success in quality (MUSIQ): building a theory of context in healthcare quality improvement. BMJ Qual Saf. 2012;21(1):13–20. https://doi.org/10.1136/bmjqs-2011-000010 .
Kringos DS, Sunol R, Wagner C, Mannion R, Michel P, Klazinga NS, et al. The influence of context on the effectiveness of hospital quality improvement strategies: a review of systematic reviews. BMC Health Serv Res. 2015;15:277. https://doi.org/10.1186/s12913-015-0906-0 PMID: 26199147; PMCID: PMC4508989.
Hasle P, Bojesen A, Jensen PL, Bramming P. Lean and the working environment: a review of the literature. Int J Oper Prod. 2012;32(7):829–49. https://doi.org/10.1108/01443571211250103 .
Hasle P, Nielsen PA, Edwards K. Application of lean manufacturing in hospitals- the need to consider maturity, complexity, and the value concept. Hum Factors Ergon Manuf. 2016;26(4):430–42. https://doi.org/10.1002/hfm.20668 .
Narayanamurthy G, Gurumurthy A, Subramanian N, Moser R. Assessing the readiness to implement lean in healthcare institutions – a case study. Int J Prod Econ. 2018;197:123–42. https://doi.org/10.1016/j.ijpe.2017.12.028 .
Bijl A, Ahaus K, Ruël G, Gemmel P, Meijboom B. Role of lean leadership in the lean maturity - second-order problem-solving relationship: a mixed methods study. BMJ Open. 2019;9(6):e026737. https://doi.org/10.1136/bmjopen-2018-026737 .
Waring JJ, Bishop S. Lean healthcare: rhetoric, ritual and resistance. Soc Sci Med. 2010;71(7):1332–40. https://doi.org/10.1016/j.socscimed.2010.06.028 .
Arumugam V, Antony J, Kumar M. Linking learning and knowledge creation to project success in six sigma projects: an empirical investigation. Int J Prod Econ. 2013;141(1):388–402. https://doi.org/10.1016/j.ijpe.2012.09.003 .
Wilson WJ, Jayamaha N, Frater G. The effect of contextual factors on quality improvement success in a lean-driven New Zealand healthcare environment. Int J Lean Six Sigma. 2018;9(2):199–220. https://doi.org/10.1108/IJLSS-03-2017-0022 .
Gonzalez-Aleu F, Van Aken EM, Cross J, Glover WJ. Continuous improvement project within kaizen: critical success factors in hospitals. TQM J. 2018;30(8):335–55. https://doi.org/10.1108/TQM-12-2017-0175 .
Stanton P, Gough R, Ballardie R, Bertram T, Bamber GJ, Sohal A. Implementing lean management/six sigma in hospitals: beyond empowerment or work intensification? Int J Hum Res Manag. 2014;25(21):2926–40. https://doi.org/10.1080/09585192.2014.963138 .
McIntosh B, Sheppy B, Cohen I. Illusion or delusion--lean management in the health sector. Int J Health Care Qual Assur. 2014;27(6):482–92. https://doi.org/10.1108/IJHCQA-03-2013-0028 .
Jimmerson C, Weber D, Sobek DK 2nd. Reducing waste and errors: piloting lean principles at Intermountain Healthcare. Jt Comm J Qual Patient Saf. 2005;31(5):249–57. https://doi.org/10.1016/s1553-7250(05)31032-4 .
Drotz E, Poksinska B. Lean in healthcare from employees' perspectives. J Health Organ Manag. 2014;28(2):177–95. https://doi.org/10.1108/JHOM-03-2013-0066 .
Morgan SJ, Pullon SRH, Macdonald LM, McKinlay EM, Gray BV. Case study observational research: a framework for conducting case study research where observation data are the focus. Qual Health Res. 2017;27(7):1060–8. https://doi.org/10.1177/1049732316649160 Epub 2016 May 22. PMID: 27217290 .
van Rossum L, Aij KH, Simons FE, van der Eng N, Ten Have WD. Lean healthcare from a change management perspective. J Health Organ Manag. 2016;30(3):475–93. https://doi.org/10.1108/JHOM-06-2014-0090 .
Savage C, Parke L, von Knorring M, Mazzocato P. Does lean muddy the quality improvement waters? A qualitative study of how a hospital management team understands lean in the context of quality improvement. BMC Health Serv Res. 2016;16(588). https://doi.org/10.1186/s12913-016-1838-z .
Download references
Acknowledgements
Not applicable.
Author information
Authors and affiliations.
Department of Management Studies, LUM University, S.S. 100 Km, 70010, Casamassima, Italy
Angelo Rosa, Giuliano Marolla & Francesco Manfredi
Center in Health Administration, and Center for Applied Health Economics and Management of IRCCS Galeazzi, University of Milan, Via Giacomo Venezian, 1, 20133, Milan, Italy
Federico Lega
You can also search for this author in PubMed Google Scholar
Contributions
All authors discussed the results and contributed to the final manuscript. GM conceived and designed the analysis, AR contributed data and analysis tools, FL and FM suggested the background reference model. The authors read and approved the final manuscript.
Corresponding author
Correspondence to Giuliano Marolla .
Ethics declarations
Ethics approval and consent to participate.
Research project sheet describing the study purpose and procedures was provided and approved by Hospital Directorate. Hospital management informed potential participants and hospital staff about the study at its launch and before the interviews and questionnaires administration. It was disclosed that participation was voluntary and that voluntary participation in the study involved consent for publication. Fully informed verbal consent to participate was obtained from all participants prior to inclusion in the study. Anonymity was guaranteed as requested by the participants. The study was submitted to and approved by the LUM University Ethics Committee.
Consent for publication
Competing interests.
The authors declare that they have no competing interests.
Additional information
Publisher’s note.
Springer Nature remains neutral with regard to jurisdictional claims in published maps and institutional affiliations.
Supplementary Information
Additional file 1., rights and permissions.
Open Access This article is licensed under a Creative Commons Attribution 4.0 International License, which permits use, sharing, adaptation, distribution and reproduction in any medium or format, as long as you give appropriate credit to the original author(s) and the source, provide a link to the Creative Commons licence, and indicate if changes were made. The images or other third party material in this article are included in the article's Creative Commons licence, unless indicated otherwise in a credit line to the material. If material is not included in the article's Creative Commons licence and your intended use is not permitted by statutory regulation or exceeds the permitted use, you will need to obtain permission directly from the copyright holder. To view a copy of this licence, visit http://creativecommons.org/licenses/by/4.0/ . The Creative Commons Public Domain Dedication waiver ( http://creativecommons.org/publicdomain/zero/1.0/ ) applies to the data made available in this article, unless otherwise stated in a credit line to the data.
Reprints and permissions
About this article
Cite this article.
Rosa, A., Marolla, G., Lega, F. et al. Lean adoption in hospitals: the role of contextual factors and introduction strategy. BMC Health Serv Res 21 , 889 (2021). https://doi.org/10.1186/s12913-021-06885-4
Download citation
Received : 30 October 2020
Accepted : 09 August 2021
Published : 28 August 2021
DOI : https://doi.org/10.1186/s12913-021-06885-4
Share this article
Anyone you share the following link with will be able to read this content:
Sorry, a shareable link is not currently available for this article.
Provided by the Springer Nature SharedIt content-sharing initiative
- Lean implementation
- Contextual factors
- Introduction strategy
BMC Health Services Research
ISSN: 1472-6963
- General enquiries: [email protected]

IMAGES
VIDEO
COMMENTS
The following case studies of lean management principles in action show you how a variety of real businesses solved real business problems under diverse conditions. ... Lean Design and Construction Project an Extension of Lean Commitment at Akron Children's Hospital. Input from nurses, doctors, therapists, technicians, and patient parents ...
Increasing First Run Parts From 60% to 90% With Lean Six Sigma. Reducing Bent/Scratched/Damaged (BSD) Scrap for Building Envelopes. Reducing Lead Time in Customer Replacement Part Orders by 41%. Reducing Learning Curve Rampu0003 for Temp Employees by 2 Weeks. Reducing Purchase Order Lead Time by 33% Using Lean Six Sigma.
The Definitive Guide to Lean Project Management. Lean is an often-used adjective in business these days, but there's some confusion over its exact definition. In essence, the goal of Lean is to maximize value while minimizing waste. In other words, creating more value for the customer with fewer resources.
ConMed is a global medical technology company that specializes in the development and sale of surgical and patient monitoring products and services. Lean case studies on how to reduce product development time by up to 75%. Learn from medical device companies, grid solutions, manufacturing, aeronautics engineering, industrial manufacturing ...
This case study is one of three highlighting successes identified as part of the Operational Excellence in Government Project . The purpose of the case studies is to elevate and document the successes, and in doing so to provide a greater amount of detail than is typically available about such efforts . The case studies explain the
Therefore, this study goes beyond demonstrating how the process management approach and the Lean system overlap or differ (Maldonado et al., 2020), and shows that Lean practices and values influence and help improve the effectiveness of processes.
The application of the Six Sigma methodology blended and supported by the application of various Lean tools is demonstrated in a case study of a kindergarten. Multiple tools, such as: the fishbone diagram; A3 reporting; '5 Why's'; process mapping; waste analysis; and 5S amongst others led to a reorganisation of the preparation room.
CASE STUDIES We come recommended by the industry experts Recovering with minimum losses A successful story of project recovery through Integrated Lean Project Delivery (ILPD) & collective team efforts. Read Case Study SIMILAR CASE STUDIES JTC CORPORATION Achieve Lean execellence by implementing Lean PlanDo® across all your developments. Read Case Study HSL CONSTRUCTOR PTE LTD […]
This case study focuses on the effectiveness of using lean project management to evaluate, define, implement and sustain consistent operational efficiency. A small, innovative manufacturing company was struggling with a lack of clear communication for the two shifts of their production. In most cases, the company made changes on the first shift ...
Discover the details of lean project management in this comprehensive blog. Explore step-by-step implementation, pros and cons, and more! ... But, let's understand it better with a case study. The following lean project management example illustrates the application of Lean Project Management principles in a software development context:
A Lean Project Management toolbox might very well be the answer. Numerous surveys and studies have documented that nearly half of all projects are behind schedule and/or over budget. While the Lean Project Management toolbox is highly valuable, it is not a magic wand. ... as defined in each case by the customer." (Womack & Jones, 1996, p. 353 ...
Lean Agile Project Management Case Study. David Paulson - 05/28/20 02:30 PM. Recently, we had the fortunate opportunity to talk to our second Playbook customer about the successful completion of their large and complex project. In this particular implementation, the company achieved 60% reduction in cycle time as well as a 50% reduction in cost.
Lean Six Sigma Case Studies. Welcome to the Lean Six Sigma Academy's Case Studies section! Here, you will find a collection of real-world examples of how companies have successfully implemented the Lean Six Sigma methodology to improve their business operations. Each case study includes an overview of the business challenge that was faced ...
In the case study, a Lean Management approach was pursued through the re-engineering of the production flow and the implementation of a pull-based system. Results from the case study show that it was a successful choice: efficiency KPIs, Works in Process, Cycle Time, etc. were dramatically improved.
Leicht, R. M., Messner, J. I., and Asadian, E. (2022). A case study in lean construction: Baker Concrete. Case Study No. 03, Architectural Engineering, The Pennsylvania State University, Univ. Park, PA. 4 Case Study Process In late September 2021, the case study was undertaken through a two-day visit to Baker Concrete
Bringing together individuals unfamiliar with the organization's culture for a Lean project proved very challenging and did not occur during the timeframe of this case study. Physicians are also a difficult group to engage according to many staff, including several executives, a management engineer, and a couple of frontline staff.
Abstract. This chapter presents three Lean Six Sigma (LSS) case studies to explain the application of LSS project management in Banking firms. By studying LSS project cases from three banks, this chapter presents lessons learned and implications. It concludes that the extent of applicability of LSS in Banking depends on the interest, rigor and ...
This report presents an introduction to the application of Lean principles in health care settings to improve quality of care, increase efficiency, lower costs, and provide better patient outcomes. Lean is an organizational redesign approach focused on elimination of waste, which is defined as any activity that consumes resources (e.g., staff, time, money, space) without adding value to those ...
Lastly, this paper will enrich the existing literature dealing with the topics of Lean Management in the Healthcare sector, bringing a successful case study in which the implementation of the Lean techniques is addressed through the use of the A3 methodology. This paper also has some limitations that need to be remarked on and explained here.
In a case study, [26] implement the Lean Project Delivery System (LPDS) using 3D and 4D CAD. They provide a brief guideline on applying the Virtual Building Technologies effectively during the lean design phase of LPDS. ... For this project, no BIM management tools or lean techniques had been used. To test the hypothesis, the researchers ...
Case Study - Lean Project Management in a Multi-project Environment Proceedings IGLC31, 26 June - 2 July 2023, Lille, France 1246 Figure 1: A visualization of the method and structure of this paper (Dresch et al. 2015; Hamerski et al. 2019). As the figure shows, the first step in DSR is to identify the problem and break it down into its
Background In the scientific literature, many studies describe the application of lean methodology in the hospital setting. Most of the articles focus on the results rather than on the approach adopted to introduce the lean methodology. In the absence of a clear view of the context and the introduction strategy, the first steps of the implementation process can take on an empirical, trial and ...