To read this content please select one of the options below:
Please note you do not have access to teaching notes, maintenance management: literature review and directions.
Journal of Quality in Maintenance Engineering
ISSN : 1355-2511
Article publication date: 1 July 2006
The purpose of this paper is to review the literature on maintenance management and suggest possible gaps from the point of view of researchers and practitioners.

Design/methodology/approach
The paper systematically categorizes the published literature and then analyzes and reviews it methodically.
The paper finds that important issues in maintenance management range from various optimization models, maintenance techniques, scheduling, and information systems etc. Within each category, gaps have been identified. A new shift in maintenance paradigm is also highlighted.
Practical implications
Literature on classification of maintenance management has so far been very limited. This paper reviews a large number of papers in this field and suggests a classification in to various areas and sub areas. Subsequently, various emerging trends in the field of maintenance management are identified to help researchers specifying gaps in the literature and direct research efforts suitably.
Originality/value
The paper contains a comprehensive listing of publications on the field in question and their classification according to various attributes. The paper will be useful to researchers, maintenance professionals and others concerned with maintenance to understand the importance of maintenance management
- Maintenance
- Optimization techniques
- Production scheduling
- Performance measures
- Information systems
Garg, A. and Deshmukh, S.G. (2006), "Maintenance management: literature review and directions", Journal of Quality in Maintenance Engineering , Vol. 12 No. 3, pp. 205-238. https://doi.org/10.1108/13552510610685075
Emerald Group Publishing Limited
Copyright © 2006, Emerald Group Publishing Limited
Related articles
We’re listening — tell us what you think, something didn’t work….
Report bugs here
All feedback is valuable
Please share your general feedback
Join us on our journey
Platform update page.
Visit emeraldpublishing.com/platformupdate to discover the latest news and updates
Questions & More Information
Answers to the most commonly asked questions here
A Research for Computerized Maintenance Management System and Predictive Maintenance Investments in Turkish Industry
- Conference paper
- First Online: 29 May 2021
- Cite this conference paper
- Arafat Salih Aydıner ORCID: orcid.org/0000-0002-1133-5995 12 &
- Burak Kubilay ORCID: orcid.org/0000-0001-9467-0678 12
Part of the book series: Lecture Notes in Networks and Systems ((LNNS,volume 239))
Included in the following conference series:
- European, Asian, Middle Eastern, North African Conference on Management & Information Systems
1526 Accesses
The enterprises which are used in industries that capital-intensive investments take place such as aviation, maritime, manufacturing, and energy, become more complex and their total cost of ownership has risen gradually in parallel with the technological developments. To use these expensive technological instruments properly, organizations use systems that enable a much better maintenance efficiency like computerized maintenance management and predictive maintenance systems. Especially with Industry 4.0, predictive maintenance’s ability for data analytics on certain equipment has become a very popular topic in literature. However, this popularity has some missing essential points which are directly connected with system and cost efficiency theories. It is assessed that making investments for these systems without a holistic approach could cause a potential risk and could lead organizations to catastrophic financial losses. Turkey as a developing country with its organizations in a turbulent financial environment should be very sensitive about properly designed and implemented maintenance information systems investment projects which are directly connected to their total efficiency. This research aims at providing a descriptive overview of the maintenance information technology investments in Turkish companies and creating a path for future research.
This is a preview of subscription content, log in via an institution to check access.
Access this chapter
- Available as PDF
- Read on any device
- Instant download
- Own it forever
- Available as EPUB and PDF
- Compact, lightweight edition
- Dispatched in 3 to 5 business days
- Free shipping worldwide - see info
Tax calculation will be finalised at checkout
Purchases are for personal use only
Institutional subscriptions
Labib, A.W.: World-class maintenance using a computerized maintenance management system. J. Qual. Main. Eng. 4 (1), 66–75 (1998)
Article Google Scholar
Laura, S.: Computerized maintenance management systems: a study of system design and use. Prod. Inven. Manage. J. Second Q. 38 (2), 11–15 (1997)
Google Scholar
Pwc & Mainnovation. Predictive maintenance 4.0: predict the unpredictable. Report, June 1–32 (2017)
Labib, A.W.: A decision analysis model for maintenance policy selection using a CMMS. J. Qual. Main. Eng. 10 (3), 191–202 (2004)
Dhall, R., Solanki, V.: An IoT based predictive connected car maintenance approach. Int. J. Interact. Multimed. Artif. Intell. 4 (3), 16–22 (2017)
Olalere, I.O., Dewa, M.: Early fault detection of elevators using remote condition monitoring through IoT technology. S. Afr. J. Indus. Eng. 29 (4), 17–32 (2018)
Kızrak, M.A., Bolat, B.: Predictive maintenance of aircraft motor health with long-short term memory method. J. Inf. Tech. 12 (2), 103–109 (2019)
Lopes, I., Senra, P., Vilarinho, S., Sá, V., Teixeira, C., Lopes, J., Alves, A., Oliveira, J.A., Figueiredo, M.: Requirements specification of a computerized maintenance management system – a case study. Procedia CIRP 52 , 268–273 (2016)
Ahuja, P.S.: Handbook of maintenance management and engineering. chapter 17, pp. 417–459 (2009)
Abbas, M., Mahmood, S.: An overview of maintenance management strategies for the corroded steel structures in extreme marine environments. Mar. Struct. 71 , 1–23 (2020)
Majeed Ali, A.A.: Application of computerized maintenance management system in industry. In: Proceedings of the 37 th International Conference on Computers and Industrial Engineering, pp. 984–995 (2007)
Swanson, L.: An information-processing model of maintenance management. Int. J. Prod. Econ. 83 , 45–64 (2003)
Velmuguran, R.S., Dhingra, T.: Maintenance strategy selection and its impact in maintenance function. Int. J. Oper. Prod. Manage. 35 (12), 1622–1661 (2014)
Fumagalli, L., Macchi, M., Rapaccini, M.: Computerized maintenance management systems in SMEs: a survey in Italy and some remarks for the implementation condition based maintenance. In: 13 th IFAC INCOM(INCOM 2009), Moscow, Russia, June 3–5, 1615–1619 (2009)
Azahar, N.F., Othuman Mydin, M.A.: Potential of computerized maintenance management system in facilities management. Anal. Univ. Eftimie J. 21 (1), 51–59 (2014)
Accorsi, R., Gallo, A., Tufano, A., Bortolini, M., Penazzi, S., Manzini, R.: A tailored maintenance management system to control spare parts life cycle. Proc. Manuf. 38 , 92–99 (2019)
Tran Anh, D., Dabrowski, K., Skrzypek, K.: The predictive maintenance concept in maintenance department of the industry 4.0 production enterprise. Found. Manage. 10 , 283–292 (2018)
Rousopoulou, V., Nizamis, A., Vafeiadis, T., Ioannidis, D., Tzovaras, D.: Predictive maintenance for injection molding machines enabled by cognitive analytics for industry 4.0. Front. Artif. Intell. 3 , 1–12 (2020)
Jimenez, J.J.M., Schwartz, S., Vingerhoeds, R., Grabot, B., Salaün, M.: Towards multi-modal approaches to predictive maintenance: a systematic literature survey on diagnostics and prognostics. J. Manuf. Syst. 56 , 539–557 (2020)
Mathews, I., Mathews, E.H., Van Laar, J.H., Hamer, W., Kleingeld, M.: A simulation-based prediction model for coal-fired power plant condenser maintenance. Appl. Therm. Eng. 174 , 1–10 (2020)
Bottani, E., Ferretti, G., Montanari, R., Vignali, G.: An empirical study on the relationships between maintenance policies and approaches among Italian companies. J. Qual. Main. Eng. 20 (2), 135–162 (2014)
Alsyouf, I.: Maintenance practices in Swedish industries: survey results. Int. J. Prod. Econ. 121 , 212–223 (2009)
Zhou, K.Z., Li, J.J., Zhou, N., Su, C.: Market orientation, job satisfaction, product quality, and firm performance: evidence from China. Strat. Manage. J. 29 (9), 984–1000 (2008)
Aydıner, A.S., Tatoğlu, E.: A field study on information systems in business applications in Turkey. Information Technologies Journal 12 (1), 59–73 (2019)
Mani, D., Barua, A., Whinston, A.: An empirical analysis of the impact of information capabilities design on business process outsorcing performance. MIS Q. 34 , 39–62 (2010)
Chen, Y., Wang, Y., Nevo, S., Benitez-Amado, J., Kou, G.: IT capabilities and product innovation performance: the roles of corporate entrepreneurship and competitive intensity. Inf. Manage. 52 , 643–657 (2015)
Download references
Author information
Authors and affiliations.
İstanbul Medeniyet University, İstanbul, Turkey
Arafat Salih Aydıner & Burak Kubilay
You can also search for this author in PubMed Google Scholar
Corresponding author
Correspondence to Arafat Salih Aydıner .
Editor information
Editors and affiliations.
Accounting, Finance and Banking Department, Ahlia University, Manama, Bahrain
Abdalmuttaleb M.A Musleh Al-Sartawi
College of Business and Finance, Ahlia University, Manama, Bahrain
Anjum Razzaque
School of Strategy and Leadership, Coventry University, Coventry, UK
Muhammad Mustafa Kamal
Rights and permissions
Reprints and permissions
Copyright information
© 2021 The Author(s), under exclusive license to Springer Nature Switzerland AG
About this paper
Cite this paper.
Aydıner, A.S., Kubilay, B. (2021). A Research for Computerized Maintenance Management System and Predictive Maintenance Investments in Turkish Industry. In: Musleh Al-Sartawi, A.M., Razzaque, A., Kamal, M.M. (eds) Artificial Intelligence Systems and the Internet of Things in the Digital Era. EAMMIS 2021. Lecture Notes in Networks and Systems, vol 239. Springer, Cham. https://doi.org/10.1007/978-3-030-77246-8_26
Download citation
DOI : https://doi.org/10.1007/978-3-030-77246-8_26
Published : 29 May 2021
Publisher Name : Springer, Cham
Print ISBN : 978-3-030-77245-1
Online ISBN : 978-3-030-77246-8
eBook Packages : Intelligent Technologies and Robotics Intelligent Technologies and Robotics (R0)
Share this paper
Anyone you share the following link with will be able to read this content:
Sorry, a shareable link is not currently available for this article.
Provided by the Springer Nature SharedIt content-sharing initiative
- Publish with us
Policies and ethics
- Find a journal
- Track your research
Academia.edu no longer supports Internet Explorer.
To browse Academia.edu and the wider internet faster and more securely, please take a few seconds to upgrade your browser .
Enter the email address you signed up with and we'll email you a reset link.
- We're Hiring!
- Help Center
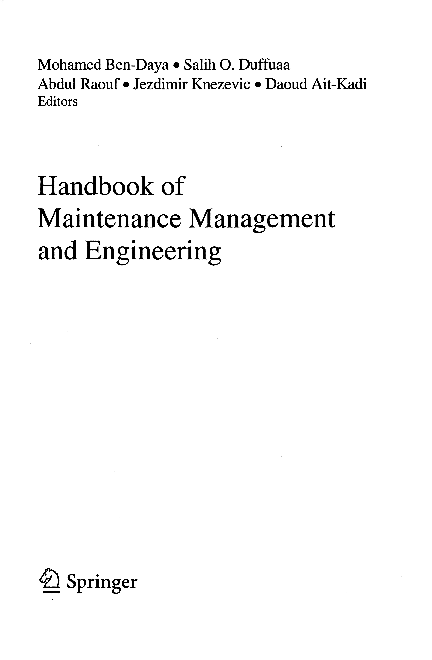
Handbook of Maintenance Management and Engineering Springer Contents

Related Papers
Usama Najeeb
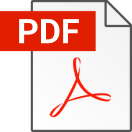
Mac - Graw Hill Publication
Mayur Mahajan
Maintenance Planning and Scheduling Handbook 2nd Edition
Journal of Quality in Maintenance Engineering
S.G. Deshmukh , Amik Garg
Pat Banjongkit
divine intervention
Purpose – The purpose of this paper is to review the literature on maintenance optimization models and associated case studies. For these optimization models critical observations are made. Design/methodology/approach – The paper systematically classifies the published literature using different techniques, and also identifies the possible gaps. Findings – The paper outlines important techniques used in various maintenance optimization models including the analytical hierarchy process, the Bayesian approach, the Galbraith information processing model and genetic algorithms. There is an emerging trend towards uses of simulation for maintenance optimization which has changed the maintenance view. Practical implications – A limited literature is available on the classification of maintenance optimization models and on its associated case studies. The paper classifies the literature on maintenance optimization models on different optimization techniques and based on emerging trends it outlines the directions for future research in the area of maintenance optimization. Originality/value – The paper provides many references and case studies on maintenance optimization models and techniques. It gives useful references for maintenance management professionals and researchers working on maintenance optimization.
Amal Witonohadi
International Journal of Software Engineering & Applications
Subhash Panja
E-maintenance
Alhussein Albarbar , Andrew Starr , Erkki Jantunen , Kenneth Holmberg
Mahros Darsin
The purpose of this paper is to review from early days until recent time the development of maintenance management methods from maintenance textbooks to give a glance view for researcher and practitioner where maintenance start until recent development and practical application of maintenance management. The methodology approach is by reviewing an early age maintenance management, maintenance management on eighties, maintenance management on nineties and recent maintenance management. Comparing and categorizing maintenance management methods along with time will increase knowledge how to choose the right maintenance for practical application. From this review it found that the paper also revealed from time to time, maintenance management adapt and improve to gain more sustainable maintenance, including the new shift of paradigm of maintenance itself. The originality and contribution of this research is that the paper contains many maintenance management methods from maintenance text...
RELATED PAPERS
pineda jozzel
European Physical Journal C
Kevin Fernández
AAPS PharmSci
Daniel Cosme Costa
Cadernos Pagu
Lindamir Salete Casagrande
Luciana Petracca
Lázaro Raymundo Reyes Gutiérrez
Jean-François Ponge
Maria do Carmo Galiazzi
Islamic Education
Semi-annual Journal of Islamic Education
Proteomics Clinical Applications
rita casadonte
Chemical Geology
Keith R Lassey
CERN European Organization for Nuclear Research - Zenodo
Dorel Noroc
International Journal of Antimicrobial Agents
Francesca Barletta
Revista Brasileira de Educação Ambiental (RevBEA)
Walison Boy
Journal of Molecular Endocrinology
Babru samal
The Pediatric Infectious Disease Journal
Vìsnik farmacìï
Victoriya Georgiyants
Forest Ecology and Management
Peichen Gong
arXiv (Cornell University)
Jeroen van Dongen
hbgjfgf hyetgwerf
Evolutionary Ecology Research
Laurent Keller
- We're Hiring!
- Help Center
- Find new research papers in:
- Health Sciences
- Earth Sciences
- Cognitive Science
- Mathematics
- Computer Science
- Academia ©2024

An official website of the United States government
The .gov means it’s official. Federal government websites often end in .gov or .mil. Before sharing sensitive information, make sure you’re on a federal government site.
The site is secure. The https:// ensures that you are connecting to the official website and that any information you provide is encrypted and transmitted securely.
- Publications
- Account settings
Preview improvements coming to the PMC website in October 2024. Learn More or Try it out now .
- Advanced Search
- Journal List
- Comput Intell Neurosci
- v.2022; 2022

Maintenance and Quality Control of Medical Equipment Based on Information Fusion Technology
Jiansheng li.
1 Shanxi Bethune Hospital, Shanxi Academy of Medical Sciences, Tongji Shanxi Hospital, Third Hospital of Shanxi Medical University, Taiyuan 030032, China
2 Tongji Hospital, Tongji Medical College, Huazhong University of Science and Technology, Wuhan 430030, China

Associated Data
The data underlying the results presented in the study are available within the article
In the medical field, to ensure the use of large medical equipment, it is necessary to carry out regular maintenance on large medical equipment. In the process of maintenance and maintenance of large-scale medical equipment, most medical personnel have not established a corresponding quality management system, neglecting daily maintenance and maintenance, resulting in many hidden dangers of medical accidents. To this end, the quality control of large medical devices should be strengthened, the control before, during, and after the event should be done well, and a comprehensive analysis of the operation methods of the equipment should be carried out to achieve reasonable maintenance of the equipment. Therefore, this paper discusses the maintenance, management, maintenance, and quality management of large medical equipment under the function of information fusion technology. This paper summarizes the problems encountered in the maintenance of medical equipment in the past and creates a medical quality control system to manage the maintenance and quality control of medical equipment. In the maintenance system of medical equipment, scientific management theories and methods are used to predict, adjust, inspect, and account for the quality of the entire production process of the equipment, and establish a complete quality monitoring and management system. To achieve optimal maintenance and economic benefits, the overall quality of medical equipment can be comprehensively improved. The data shows that the actual number of monitors for quality control testing in 2020 is 502 units, 496 units have passed the initial inspection, and 502 units have passed the maintenance, which shows that the maintenance and quality control of medical equipment based on information fusion technology is effective.
1. Introduction
The survival and development of a hospital is inseparable from medical facilities. Strengthening the repair and maintenance of medical equipment can ensure the normal operation of the hospital and reduce medical expenses. With the use of medical devices, the hospital's treatment methods have also been further improved. In practical applications, due to the automation and complexity of medical devices, maintenance must change past habits during use. Maintenance personnel must regularly check related equipment, which puts forward higher requirements for the maintenance and management of medical equipment. Therefore, this paper discusses the maintenance and repair of large medical equipment. The maintenance and management of medical equipment ensures its superiority in use. The clinical application of medical equipment is essential, and its maintenance quality directly affects the work efficiency of the hospital, as well as the survival and health of patients. Therefore, it is necessary to carry out routine maintenance on existing medical devices and analyze their scientific and institutionalized advantages in operation, thereby greatly improving the service life of medical devices.
Research into the maintenance and quality control of medical equipment has been ongoing. Zheng discussed how to optimize the quality control of medical devices and improve the implementation effect of quality control, to improve the quality of medical devices and the level of clinical diagnosis and treatment [ 1 ]. Hao discussed the use of the Medatc system for inspection and failure statistics of hysteroscopic and laparoscopic equipment [ 2 ]. Saffarpur aimed to evaluate the effectiveness of curing light equipment routinely used in Karaj Dental Clinic in 2016 [ 3 ]. Jun evaluated the current situation and the current situation of quality control in the intensive care unit (ICU) of Sichuan Provincial Hospital of Integrated Traditional Chinese and Western Medicine and Minority Hospital [ 4 ]. Jose developed a series of technical quality control (TQC) guidelines for radiotherapy equipment [ 5 ]. Liu Y reviewed the current status and future trends of clinical quality control procedures and MRI equipment regulation [ 6 ]. The data information obtained by these studies is too simple, and the data is not integrated, so the value of the data cannot be fully utilized.
Many scholars have conducted research on information fusion technology. Du used the big data association rule mining method to realize the information fusion of mathematics teaching resources [ 7 ]. Zhang explored the potential of multisource information fusion techniques to improve model calibration and prediction performance in Chinese herbal medicine extraction process [ 8 ]. Shuai designed a fusion method of radar and electro-optical information [ 9 ]. These research fields do not cover the medical field, and there is also a lack of data support, so this paper studies the maintenance and quality control of medical equipment based on information fusion technology.
This paper takes several common medical equipments in a hospital as the research object and uses the equipment qualification rate as the research index to test the qualification rate before and after equipment maintenance. The data shows that the actual number of defibrillators tested for quality control in 2018 was 19, of which 16 passed the initial inspection and 18 passed the maintenance, indicating that equipment maintenance and quality control play a significant role in medical equipment.
2. Medical Equipment Maintenance and Quality Control
Medical equipment is different from both hospital equipment and medical equipment. Hospital equipment mainly includes two major parts: medical equipment and logistics equipment. Medical equipment and medical equipment include medical equipment and medical materials, appliances, software, etc. The conceptual relationship related to medical equipment is shown in Figure 1 .

Conceptual figures related to medical devices.
Large-scale hospital equipment maintenance needs to be improved:
The poor management of the acceptance of large medical devices has seriously affected the follow-up operation of the hospital. For example, in the purchase of large medical equipment, the hospital management model has some flaws and defects [ 10 , 11 ].
In the daily procurement, the large-scale equipment of the hospital is generally carried out by contract and then allocated according to the corresponding procedures. Due to the inability to carry out centralized management, it will cause some negligence of the distribution personnel during the transportation process, resulting in insufficient overall maintenance capability of the equipment [ 12 , 13 ].
During the acceptance process, because the hospital did not conduct inspections in time, the potential risks of medical devices could not be found in time. This has a negative impact on the subsequent use and maintenance of medical devices, thereby affecting the normal use of medical devices [ 14 , 15 ]. In addition, in the management of equipment, it has not reached the corresponding standard, and there is a big deviation. In addition, due to the unsound management mechanism of large medical equipment in the hospital itself, medical staff cannot perform effective operations when using them [ 16 , 17 ].
Many medical workers do not have a good attitude towards instruments in their daily inspection and use [ 18 , 19 ]. They thought that once a medical device was damaged, it would be repaired by the financial department of the hospital, not regularly repaired, nor regularly inspected according to the regulations. This leads to overloading of many devices, which shortens the life of the device. Once a fault occurs, it is difficult to find relevant information, and it is difficult to find the personnel responsible for it, which affects the information management level of the hospital and thus affects the subsequent development of the hospital. Therefore, in the future work, to realize the comprehensive development of the hospital, the first problem to be solved is the information management [ 20 , 21 ].
The elements of medical equipment maintenance are as follows:
The essence of the maintenance of medical equipment is to prolong the service life of the instrument, ensure the integrity and utilization rate of the instrument, and reduce the probability of failure during use [ 22 ]. In the maintenance department of the hospital, according to the characteristics and structure of the equipment, a new equipment maintenance plan was designed to ensure the safety and operation of the equipment. In the traditional security measures, the following methods can be used to optimize, such as regular inspections. In the daily inspection, regular maintenance of the instrument is also an important basis for equipment maintenance. Therefore, it is the key to ensure the safe operation of equipment to effectively prevent equipment safety accidents and to carry out regular maintenance and repairs.
Regular maintenance and preventive maintenance of the machinery are carried out on a regular basis to ensure that the machine can be cleaned regularly according to the technical requirements of the machine during normal operation. Then, perform a performance test. Detect damaged parts of machinery and equipment, analyze the overall condition of lines and waterways, and centrally optimize the operation of large medical equipment to ensure that both are fully functional.
To ensure the efficient development of the hospital, the equipment of the general department must be standardized and perfected and people-centered. Pay full attention to the improvement of the quality and skills of maintenance personnel, stimulate their enthusiasm for work, let them be assertive, take the patient as the center, take the survival and development of the hospital as their own responsibility, and adhere to the interests of society. Optimize the financial responsibility of the hospital to ensure that it can obtain new competitive forces in the market competition and achieve all-round development.
The quality control of large medical devices is as follows:
- Regularly organize training
- For the current medical equipment management, we ensure that the employees can consciously carry out the maintenance of medical equipment. For example, managers have to change their minds and adapt to large-scale medical devices. According to their professional skills and business level, choose excellent managers. In addition, after new equipment is put into service, employees must be regularly evaluated and trained. Equipment such as B-ultrasound and CT need to be licensed. After that, a responsibility control system was implemented for the quality inspection of the equipment, so that the defect behavior of the equipment was effectively implemented. At the same time, punish the causes of medical device failure due to personal reasons, urge operators to operate in accordance with standards, and improve the use, quality, and management level of medical devices.
- Implement the quality management system of equipment
- Implement the equipment quality control system in the standardized management, strengthen the large-scale medical equipment on the basis, improve the process of pre-purchase, in-purchase, use, etc., establish a set of evaluation systems and systems, and supervise the quality of medical equipment. For example, consider the entire quality management as the most critical step in the purchasing process. Pay more attention to relevant personnel and improve the quality of the overall equipment. To ensure the quality of medical devices, hospitals must conduct quality control and monitoring on a regular basis. Carry out a comprehensive inspection of the maintenance, installation, and debugging of the equipment, debug when purchasing the equipment, check the consistency of the equipment, and analyze the influencing factors in use to improve the quality of the equipment. For example, during use, the operator's working methods can be standardized, regular training can be organized, and comprehensive use and records of equipment, including maintenance records and maintenance records, can be done well. Ensure the timely control of existing problems and do a good job in the information management of large medical devices. With the continuous improvement of the level of medical informatization, the hospital must carry out a comprehensive management model reform, obtain new failure rates and maintenance rates, and conduct data analysis on them. In terms of medical device management, the latest mobile software technology and RFID technology are adopted to realize the monitoring and management of medical devices and ensure that the quality of large medical devices has reliable support.
Determine the quality assurance measures that should be taken according to the risk level of the equipment. During the implementation process, the effectiveness of risk control should be dynamically evaluated, and the risk estimation and risk analysis should be adjusted repeatedly. The risk assessment model is shown in Figure 2 .

Risk assessment model.
Risks are divided into six parts: equipment attributes, physical risk, equipment characteristics, safety performance, lethal state, and frequency of use.
The equipment properties and their risk scores are shown in Table 1 .
Device properties.
Physical risk mainly refers to the adverse consequences that may be caused by abnormal operation of the equipment, which can be summarized as death, injury, errors, etc. The physical risks and their risk scores are shown in Table 2 .
Physical risk.
The equipment characteristics and their risk scores are shown in Table 3 .
Device features.
The safety performance and its risk score are shown in Table 4 .
Safety features.
The lethal state and frequency of use are shown in Table 5 .
Lethal status and frequency of use.
The meaning of PDCA cycle is to divide quality management into four stages, namely, Plan (planning), Do (execution), Check (check), and Act (processing). In the quality management activities, it is required to make plans, implement the plans, and check the effect of implementation. Then, the successful ones are included in the standard, and the unsuccessful ones are left to the next cycle to solve. The quality control method adopts the PDCA cycle management method, as shown in Figure 3 .

PDCA cycle.
The overall level and ability of medical equipment control is concentrated in the medical equipment quality control system, which plays a great role in the management and control of hospital medical equipment, and depends on it to improve the overall medical level of the hospital. Hospitals not only need to closely integrate the construction of the medical equipment quality control system with their own characteristics, and learn from the research of scholars, but also follow the following principles:
Practical principles. All indicators of the medical equipment quality control system need to collect data in the form of questionnaires and then process the questionnaire data. Therefore, the index system must be practical, can truly reflect the overall level of medical equipment, and be easy to operate.
Scientific principles. The overall framework of the paper, the research objects, and the guiding methods are the cornerstones, and the index construction of the medical equipment quality control system can be scientific, rational, and justified.
Quantitative principles. The construction of the medical equipment quality control system is to prepare for later empirical research, so each index in the system needs to be mathematically quantified, to carry out the modeling and quantitative analysis of the empirical research.
In general, the life cycle of the designed equipment is determined by the quality of the medical equipment. Therefore, this paper first chooses the life cycle theory and the total quality management theory to select the indicators. Then, combine the previous research to classify the indicators, and finally determine the overall system indicators of medical equipment quality control combined with the risk management theory.
The existing problems in the quality control of hospital medical equipment are:
Insufficient quality inspection personnel. A common phenomenon in hospitals now is the lack of professionals. Many medical engineering technicians and some other medical personnel take into account the measurement and quality control work, which originally required professionals to be responsible. Because of the limited number of engineering and technical personnel and the large number of medical facilities, these technicians are usually only responsible for the management and maintenance of the facilities. This has led to problems such as overdue use and missed inspections in many facilities. Not only that, but some facilities have lost quality control.
Acceptance testing is not standardized enough. Hospitals only rely on personal feelings and experience to test whether newly purchased medical facilities are qualified. When the facility is checked and accepted, it is still the traditional way to check whether the outer packaging of the facility is in good condition, whether the relevant accessories are sufficient, and whether it can be powered on normally. This kind of verification to judge whether a facility is qualified or not based on simple external performance is seriously insufficient. There is no scientific and accurate reference index and verification basis for this method. In this way, the purchased equipment is often unqualified, and it is easy to make mistakes and dangers in clinical use.
The purpose of the construction of the medical equipment quality control system is to ensure that the stability, safety, and accuracy of the parameters of the equipment can be guaranteed. The specific work mainly includes the following three parts: The first is to ensure the formation of the organizational management system. Form a situation in which special personnel are responsible and leaders pay attention. And increase the supervision and management of the entire process, methods, and other links. Second, building a quality control process system can ensure that quality management is implemented in the entire life cycle of the equipment, and it can be continuously improved and improved in actual use. The third is the construction of the security system. Strengthen the allocation of special tools and professional testing personnel, to form a guarantee for the good operation of the quality control system.
The medical equipment quality control system is shown in Figure 4 .

Medical device quality control system.
The so-called quality inspection and control before the application of equipment is not only necessary to determine the comprehensiveness of its safety performance before the purchase of medical equipment, but also to sign an effective safety contract to ensure the quality level of the entire purchased medical equipment. At the same time, this is also the original step of equipment quality assurance.
Project demonstration quality control. In each department of the hospital, as long as there is a need for some high-risk medical equipment or equipment, professional project approval for the required equipment, as well as a wealth of data demonstration, must be carried out. At the same time, according to the relevant research data, we set up a special project report and establish a file. The main items that should be included are: all information and details related to the required medical equipment, and all feasibility assumptions related to the required equipment, as well as feasibility studies. At the same time, according to the risk and value of the required medical equipment, the setting and the reason for the need should be justified.
Plan approval for quality control. In the gradual development stage of science and technology, the detection and control of the safety factors of medical equipment and equipment in major hospitals is the primary prerequisite for medical development. At the same time, it is also an important basic prerequisite for adapting to the development of science and technology. Therefore, for the safety guarantee of medical equipment, it is necessary to carry out the planned quality inspection and control for approval. In terms of medical equipment, risks in the process of its use should be avoided, and procedures and projects that require technical content should be encouraged and supported, and attention should be given to action. For some more important and high-risk medical devices, it is necessary to conduct in-depth investigation and research by multi-level leaders and departments, as well as relevant high-level technical personnel. After obtaining the plan approval, it can be effectively implemented and used, to effectively control the quality and safety of plan approval.
Manufacturer selection quality control. For the purchase and investment of medical equipment required by the hospital, it is necessary to go through very strict procedures and steps to check and test the quality of the required products and equipment. Among them, first of all, it is necessary to confirm the relevant certificates of the purchased medical equipment manufacturers, for example, similar certificates such as the equipment registry and the manufacturer's authorization letter, must be strictly checked and tested. Secondly, it is to carry out careful measurement and evaluation of relevant health aspects. At the same time, health testing is also the most basic control and testing for the medical quality of medical manufacturers. Then, for the selection of medical equipment manufacturers and suppliers, the selection of medical equipment manufacturers should be determined according to the basic conditions of the manufacturers, such as safety and quality issues, and hygiene and technical aspects. Secondly, according to the various departments in the hospital, the equipment required, and the data displayed in the database, all manufacturers should be screened, to effectively complete the quality screening of medical equipment.
Business negotiation quality control. Regarding the selection of the medical equipment required by the hospital, at the stage of negotiation, the hospital's bidding form and the determination of the selection method should be used to negotiate the selection of medical equipment to achieve its quality control. To better ensure the safety, quality, and level of medical equipment, it is necessary to carry out strict and formal negotiation procedures and steps, that is, relevant personnel from many departments of the hospital should be integrated into the negotiation process.
Contract quality control. At present, the operation and development of many enterprises are inseparable from the establishment of contracts, and the same is true for hospitals. Therefore, in the purchase and setting of the required medical equipment, an effective, fair, and just contract should be established in accordance with the corresponding laws and regulations to carry out quality supervision and risk control. During the establishment of the contract, not only the approval of the relevant departments, but also more professional lawyers and personnel must be recruited to set the procurement standards. As well as the writing of the contract, from the establishment of the contract, as well as the approval and testing of the relevant hospital leaders and departments, the quality assurance and risk detection and control of the purchased necessary medical equipment.
Installation acceptance quality control. After purchasing, reviewing, negotiating, and signing the contract for the relevant medical equipment required by the hospital, the preordering activities of the medical equipment required by the hospital department and department are completed. The next step is the installation and acceptance of the overall equipment and the setting of the process. In the process of this step, the most critical and main problem is that the entire installation, configuration, and inspection need to be evaluated and tested to ensure the most basic safety and hygiene.
During the whole acceptance process, the supplier of medical devices should negotiate with the relevant departments and management personnel in the hospital to verify. For the purchased medical equipment, according to the testing of relevant national standards and the evaluation, standards of the military, quality control, and evaluation are carried out to fundamentally complete the evaluation of the quality and level of the equipment required by the hospital in terms of installation and acceptance. On the other hand, in this step, the risk detection of medical equipment, as well as the control of quality and level. It is also for the hospital to be able to cause safety problems and quality risks in the process of using the equipment in the future, resulting in some important medical failures and accidents.
The hospital selects and purchases the required medical equipment in a timely manner so that it can be used in the hospital. Then, in the whole process of using medical equipment, medical staff and various departments should use and operate them in strict accordance with the settings and standards of medical equipment. However, in the process of use, relevant personnel and department personnel should also carry out irregular and irregular quality inspection and inspection according to the purpose of the device. In this way, it can not only carry out quality control and risk prevention, but also find and solve problems in time.
In the hospital, regarding the use of medical equipment, it is necessary to carry out the clinical implementation and application of its equipment according to relevant regulations and reasonable suggestions, and to ensure safety issues and control the quality and level. With the development of the medical industry, major hospitals and related health departments, as well as managers of medical associations, have increased their awareness and attention to the safety of medical devices. It has also formulated relevant regulations and systems for the clinical implementation of medical equipment and equipment, the control of risk factors, and the prevention of quality. Faced with various problems and deficiencies in the process of clinical trials, diversified management methods and systems should be used to prevent and control risks.
In hospitals, many medical staff need to strengthen standardized actions and operating procedures for the use of related clinical equipment and product operations to improve the hospital's clinical implementation technology and efficiency for new medical equipment. Based on this, the hospital should provide the most basic and standardized training for the relevant medical staff in the hospital and the users of equipment at all levels. It is necessary to train not only the methods and procedures of the newly added equipment, but also the nursing methods of the relevant personnel, so as to fundamentally guarantee and control their quality.
One is equipment installation and acceptance training. The relevant new equipment users should be in the installation and acceptance stage of the new equipment, as well as the important control and debugging stage. To understand and learn the operation method of the equipment is not only very helpful for subsequent clinical experiments; at the same time, it can also learn a lot of equipment maintenance and repair knowledge, which is convenient for the protection of new equipment and reduces the safety risk of the equipment. The second is annual equipment use training. The hospital should conduct annual training on the operation and use of equipment for all doctors and related medical staff who can access and use the new equipment. At the same time, the hospital should also integrate the newly added clinical equipment, its use and operation, and the functions and skills of the relevant equipment into the assessment content according to the annual assessment of all medical staff. This can not only strengthen the medical staff's understanding and awareness of high-risk equipment, but also promote the hospital's quality control and management of these equipments. The third is to formulate operating procedures. Hospitals have complete procedures and procedures for the use and operation of medical equipment, which must be effectively implemented and managed. In addition to posting on the wall the use and control procedures of medical devices, the hospital also requires medical staff to carry out the steps of cleaning and testing high-risk devices one at a time, thereby reducing the quality risk of medical devices.
According to the legal systems and rules and regulations related to the hygienic use of medical devices and clinical operation issues proposed by the relevant medical departments and health management and assessment departments, that is, the strategy of the “Measures for the Management of Instruments and Equipment in Medical and Health Institutions” to fundamentally restrict and manage the relevant hospital medical staff and the implementation and operation of clinical equipment to improve the quality supervision and risk prevention and management of the overall equipment.
One is to insist on working with licenses. Hospitals should carry out strict handling and assessment of hospital medical staff who contact and use high-risk medical devices. After completing the prescribed standard tasks and passing, the clinical implementation and operation of medical devices can be carried out. Even for larger volumes such as ultrasonic medical equipment and DSA, it is necessary to pass the training and assessment of relevant physician certificates, and only after obtaining a formal employment certificate can the equipment be applied and controlled to ensure the quality management and risk supervision of medical equipment. The second is to establish a system of persons responsible for the use of medical equipment. The management personnel of the relevant departments of the hospital, as well as the medical equipment supervisors, shall register the persons responsible for the use and manipulation of the hospital medical equipment, form files and books, and register and manage their implementation and manipulation to ensure the quality control of the equipment.
In the clinical trial of the hospital, the regular maintenance and testing of medical equipment is a key step in its clinical implementation and application, and it is also the most important factor affecting the risk of medical equipment use. First, we do preventive maintenance for all staff. For the control and application of hospital medical equipment, not only the maintenance and management of managers is required, but also various departments and departments are required to carry out effective prevention and maintenance. It can be divided into departments or levels, and all staff participate in the maintenance, consideration, and testing of medical and health equipment, fundamentally improve the quality management and control of medical equipment, and avoid the emergence of high-risk risks. Second, emergency maintenance quality control. As a medical device commonly used in hospitals, risks and failures will occur from time to time. Therefore, the hospital should, according to this situation, formulate an all-day duty model and plan for the relevant maintenance department of the hospital, and let the maintenance workers work 24-hour shift mode to wait for the maintenance of the hospital's medical equipment at any time. When receiving a request for declaration of equipment maintenance, the medical equipment must be repaired in the shortest possible time to avoid more serious equipment failures. Fundamentally, the quality of medical equipment can be effectively controlled to prevent the occurrence of more serious risks. Finally, quality control after maintenance. To fully ensure the safety of equipment quality, a series of strict inspections and correlation tests must be carried out after handling equipment failures. All personnel related to the equipment should attach great importance to safety issues. After repairing the equipment that has been in the category of mandatory measurement and testing, and strictly inspecting the quality of all aspects of the medical equipment in time, only the equipment that has passed the overall quality can be officially used.
Scrap standard quality control. Under the specific service period stipulated by the relevant system, if the medical equipment still cannot be used normally or is lower than the normal quality standard after being repaired by the professional department, or equipment whose repair cost is too expensive or even exceeds the specified repair cost the standard can be applied for normal scrapping. However, the problems caused by real equipment are often intertwined and complex, and specific details such as the probability of equipment use, the objective environment of use, and maintenance will also have a great impact on the service life of the equipment. Instruments and equipment that have reached their end of life are widely available in practical work. However, because the relevant staff can properly operate and maintain the equipment, even if the equipment has exceeded the specified period of use, it still has a high operating quality. However, at the same time, many departments actively concealed the scrapping of equipment under the constraints of different factors.
Quality control of end-of-life equipment disposal. Relevant approval procedures are the directions that must be adhered to in the process of disposal of scrapped equipment. At the same time, the lasting use of relevant parts should be maintained as much as possible under the guidance of the idea of thrift first. The funds obtained after the scrapping process should be recorded in detail and reported to the financial department in the name of the funds for repairing and purchasing the provident fund.
This paper is based on the information fusion technology to realize the research on the maintenance and quality control of medical equipment. Measuring the information data δε (ϱ)(ϱ=1,2, ..., γ ) obtained at time ϱ and positioning it on the number axis, the absolute distance between the information data δε (ϱ) and δζ (ϱ) is set as:
The distance between δε (ϱ) and all information data is
The average distance between all informative data is
The set of all valid information data falling in the neighborhood is set as ι , if ϵ (ϱ) satisfies the following conditions:
Then, this set is called the optimized fuzzy set.
The fusion degree of δε (ϱ) and δζ (ϱ) is
Data fusion degree matrix:
The consistency fusion degree of sensor δε at time ϱ is
The distribution equilibrium is
The weight factor is
Normalized to get:
The fusion result is
Weighted evidence indicates the predictive power of the independent variable relative to the dependent variable. Weighted evidence:
Taking the weighted evidence as a reference and the global credibility of the evidence as the basis for measuring the weight coefficient of this piece of evidence, the weight coefficients of other evidence can be expressed as:
The basic confidence function is assigned as:
3. Maintenance Test
By establishing a quality control system for medical equipment, the stability and reliability of medical equipment have been improved year by year. This paper makes a statistical analysis of the data of hospital measurement and quality control in a hospital, and the analysis results are as follows.
The quality control test results of the sphygmomanometer and the weight scale in 2018, 2020, and 2022 are shown in Figure 5(a) and Figure 5(b) , respectively.

Quality control test results of sphygmomanometer and scale. (a) shows that the initial inspection pass rate of the sphygmomanometer in 2018 was 86.21%, and the pass rate after maintenance was 98.05%. The pass rate of initial inspection in 2020 is 84.86%, the pass rate after maintenance is 88.10%, the pass rate of preliminary inspection in 2022 is 95.25%, and the pass rate after repair is 97.68%. (b) shows that the first pass rate of the quality control test of the scale in 2018 was 76.52%, and the pass rate after maintenance was 96.26%. The pass rate of initial inspection in 2020 is 88.25%, the pass rate after maintenance is 95.70%, and the pass rate of preliminary inspection in 2022 is 95.21%, and the pass rate after repair is 100%. The qualified rate of the sphygmomanometer and the weight scale has been significantly improved after maintenance. It can be seen that the hospital equipment has been effectively improved after the practice of the medical equipment quality control system.
The quality control test results of the electrocardiograph and B-ultrasound in 2018, 2020, and 2022 are shown in Figures 6(a) and 6(b) , respectively.

Quality control test results of electrocardiograph and B-ultrasound. (a) shows that the initial inspection pass rate of the ECG machine in 2018 was 100%, and the pass rate after maintenance was 100%. The pass rate of the initial inspection in 2020 is 93.18%, the pass rate after maintenance is 100%, and the pass rate of the initial inspection in 2022 is 100%, and the pass rate after maintenance is 100%. (b) shows that the initial inspection pass rate of B-ultrasound quality control inspection in 2018 was 85.56%, and the pass rate after maintenance was 92.22%. The pass rate of initial inspection in 2020 is 93.63%, the pass rate after maintenance is 100%, and the pass rate of preliminary inspection in 2022 is 89.80%, and the pass rate after repair is 100%.
The quality control test results of the ventilator and anesthesia machine in 2018, 2020, and 2022 are shown in Figures 7(a) and 7(b) , respectively.

Quality control test results of ventilator and anesthesia machine. (a) shows that the initial inspection pass rate of the ventilator in 2018 was 42.64%, and the pass rate after maintenance was 89.52%. The pass rate of the initial inspection in 2020 is 100%, the pass rate after maintenance is 100%, and the pass rate of the initial inspection in 2022 is 100%, and the pass rate after maintenance is 100%. (b) shows that the initial inspection pass rate of the quality control inspection of the anesthesia machine in 2018 was 34.60%, and the pass rate after maintenance was 84.60%. The pass rate of initial inspection in 2020 is 70.32%, the pass rate after maintenance is 100%, and the pass rate of preliminary inspection in 2022 is 87.78%, and the pass rate after repair is 100%.
The quality control test results of the monitor and defibrillator in 2018, 2020, and 2022 are shown in Figures 8(a) and 8(b) , respectively.

Quality control test results for monitors and defibrillators. (a) shows that the actual number of monitors in the quality control test in 2018 was 122, of which 100 passed the initial inspection and 116 passed the maintenance. (b) The actual number of defibrillators in the quality control inspection in 2022 is 26, of which 23 have passed the initial inspection and 25 have passed the maintenance. To sum up, no matter what kind of medical equipment, it is fully maintained after repair and quality control, thus prolonging the service life of the equipment.
4. Conclusion
The quality management of medical devices is an important part of hospital management, and it is also an inevitable trend of hospital scientific and technological progress. By establishing the quality management system of medical equipment, combining it with the thought of management, and applying it to clinical management. Quantitatively and qualitatively analyze the reliability, maintainability, and security of the instrument, so that the quality of the medical device can meet the predetermined or potential demand. And combine quantitative and qualitative requirements into technical indicators, to give full play to the value of medical equipment. In addition, this paper analyzes the problems existing in the maintenance and quality control of existing medical equipment and gives three suggestions before, during, and after the maintenance to optimize the maintenance process. At the same time, the PDCA cycle method is used to control the quality of medical equipment. The medical equipment maintenance and quality control system is immature and cannot be applied to major medical systems. Therefore, it is necessary to improve the system to the extent that it can be widely used.
Data Availability
Conflicts of interest.
The authors declare that they have no conflicts of interest.
A new future of work: The race to deploy AI and raise skills in Europe and beyond
At a glance.
Amid tightening labor markets and a slowdown in productivity growth, Europe and the United States face shifts in labor demand, spurred by AI and automation. Our updated modeling of the future of work finds that demand for workers in STEM-related, healthcare, and other high-skill professions would rise, while demand for occupations such as office workers, production workers, and customer service representatives would decline. By 2030, in a midpoint adoption scenario, up to 30 percent of current hours worked could be automated, accelerated by generative AI (gen AI). Efforts to achieve net-zero emissions, an aging workforce, and growth in e-commerce, as well as infrastructure and technology spending and overall economic growth, could also shift employment demand.
By 2030, Europe could require up to 12 million occupational transitions, double the prepandemic pace. In the United States, required transitions could reach almost 12 million, in line with the prepandemic norm. Both regions navigated even higher levels of labor market shifts at the height of the COVID-19 period, suggesting that they can handle this scale of future job transitions. The pace of occupational change is broadly similar among countries in Europe, although the specific mix reflects their economic variations.
Businesses will need a major skills upgrade. Demand for technological and social and emotional skills could rise as demand for physical and manual and higher cognitive skills stabilizes. Surveyed executives in Europe and the United States expressed a need not only for advanced IT and data analytics but also for critical thinking, creativity, and teaching and training—skills they report as currently being in short supply. Companies plan to focus on retraining workers, more than hiring or subcontracting, to meet skill needs.
Workers with lower wages face challenges of redeployment as demand reweights toward occupations with higher wages in both Europe and the United States. Occupations with lower wages are likely to see reductions in demand, and workers will need to acquire new skills to transition to better-paying work. If that doesn’t happen, there is a risk of a more polarized labor market, with more higher-wage jobs than workers and too many workers for existing lower-wage jobs.
Choices made today could revive productivity growth while creating better societal outcomes. Embracing the path of accelerated technology adoption with proactive worker redeployment could help Europe achieve an annual productivity growth rate of up to 3 percent through 2030. However, slow adoption would limit that to 0.3 percent, closer to today’s level of productivity growth in Western Europe. Slow worker redeployment would leave millions unable to participate productively in the future of work.

Demand will change for a range of occupations through 2030, including growth in STEM- and healthcare-related occupations, among others
This report focuses on labor markets in nine major economies in the European Union along with the United Kingdom, in comparison with the United States. Technology, including most recently the rise of gen AI, along with other factors, will spur changes in the pattern of labor demand through 2030. Our study, which uses an updated version of the McKinsey Global Institute future of work model, seeks to quantify the occupational transitions that will be required and the changing nature of demand for different types of jobs and skills.
Our methodology
We used methodology consistent with other McKinsey Global Institute reports on the future of work to model trends of job changes at the level of occupations, activities, and skills. For this report, we focused our analysis on the 2022–30 period.
Our model estimates net changes in employment demand by sector and occupation; we also estimate occupational transitions, or the net number of workers that need to change in each type of occupation, based on which occupations face declining demand by 2030 relative to current employment in 2022. We included ten countries in Europe: nine EU members—the Czech Republic, Denmark, France, Germany, Italy, Netherlands, Poland, Spain, and Sweden—and the United Kingdom. For the United States, we build on estimates published in our 2023 report Generative AI and the future of work in America.
We included multiple drivers in our modeling: automation potential, net-zero transition, e-commerce growth, remote work adoption, increases in income, aging populations, technology investments, and infrastructure investments.
Two scenarios are used to bookend the work-automation model: “late” and “early.” For Europe, we modeled a “faster” scenario and a “slower” one. For the faster scenario, we use the midpoint—the arithmetical average between our late and early scenarios. For the slower scenario, we use a “mid late” trajectory, an arithmetical average between a late adoption scenario and the midpoint scenario. For the United States, we use the midpoint scenario, based on our earlier research.
We also estimate the productivity effects of automation, using GDP per full-time-equivalent (FTE) employee as the measure of productivity. We assumed that workers displaced by automation rejoin the workforce at 2022 productivity levels, net of automation, and in line with the expected 2030 occupational mix.
Amid tightening labor markets and a slowdown in productivity growth, Europe and the United States face shifts in labor demand, spurred not only by AI and automation but also by other trends, including efforts to achieve net-zero emissions, an aging population, infrastructure spending, technology investments, and growth in e-commerce, among others (see sidebar, “Our methodology”).
Our analysis finds that demand for occupations such as health professionals and other STEM-related professionals would grow by 17 to 30 percent between 2022 and 2030, (Exhibit 1).
By contrast, demand for workers in food services, production work, customer services, sales, and office support—all of which declined over the 2012–22 period—would continue to decline until 2030. These jobs involve a high share of repetitive tasks, data collection, and elementary data processing—all activities that automated systems can handle efficiently.
Up to 30 percent of hours worked could be automated by 2030, boosted by gen AI, leading to millions of required occupational transitions
By 2030, our analysis finds that about 27 percent of current hours worked in Europe and 30 percent of hours worked in the United States could be automated, accelerated by gen AI. Our model suggests that roughly 20 percent of hours worked could still be automated even without gen AI, implying a significant acceleration.
These trends will play out in labor markets in the form of workers needing to change occupations. By 2030, under the faster adoption scenario we modeled, Europe could require up to 12.0 million occupational transitions, affecting 6.5 percent of current employment. That is double the prepandemic pace (Exhibit 2). Under a slower scenario we modeled for Europe, the number of occupational transitions needed would amount to 8.5 million, affecting 4.6 percent of current employment. In the United States, required transitions could reach almost 12.0 million, affecting 7.5 percent of current employment. Unlike Europe, this magnitude of transitions is broadly in line with the prepandemic norm.
Both regions navigated even higher levels of labor market shifts at the height of the COVID-19 period. While these were abrupt and painful to many, given the forced nature of the shifts, the experience suggests that both regions have the ability to handle this scale of future job transitions.

Businesses will need a major skills upgrade
The occupational transitions noted above herald substantial shifts in workforce skills in a future in which automation and AI are integrated into the workplace (Exhibit 3). Workers use multiple skills to perform a given task, but for the purposes of our quantification, we identified the predominant skill used.
Demand for technological skills could see substantial growth in Europe and in the United States (increases of 25 percent and 29 percent, respectively, in hours worked by 2030 compared to 2022) under our midpoint scenario of automation adoption (which is the faster scenario for Europe).
Demand for social and emotional skills could rise by 11 percent in Europe and by 14 percent in the United States. Underlying this increase is higher demand for roles requiring interpersonal empathy and leadership skills. These skills are crucial in healthcare and managerial roles in an evolving economy that demands greater adaptability and flexibility.
Conversely, demand for work in which basic cognitive skills predominate is expected to decline by 14 percent. Basic cognitive skills are required primarily in office support or customer service roles, which are highly susceptible to being automated by AI. Among work characterized by these basic cognitive skills experiencing significant drops in demand are basic data processing and literacy, numeracy, and communication.
Demand for work in which higher cognitive skills predominate could also decline slightly, according to our analysis. While creativity is expected to remain highly sought after, with a potential increase of 12 percent by 2030, work activities characterized by other advanced cognitive skills such as advanced literacy and writing, along with quantitative and statistical skills, could decline by 19 percent.
Demand for physical and manual skills, on the other hand, could remain roughly level with the present. These skills remain the largest share of workforce skills, representing about 30 percent of total hours worked in 2022. Growth in demand for these skills between 2022 and 2030 could come from the build-out of infrastructure and higher investment in low-emissions sectors, while declines would be in line with continued automation in production work.
Business executives report skills shortages today and expect them to worsen
A survey we conducted of C-suite executives in five countries shows that companies are already grappling with skills challenges, including a skills mismatch, particularly in technological, higher cognitive, and social and emotional skills: about one-third of the more than 1,100 respondents report a shortfall in these critical areas. At the same time, a notable number of executives say they have enough employees with basic cognitive skills and, to a lesser extent, physical and manual skills.
Within technological skills, companies in our survey reported that their most significant shortages are in advanced IT skills and programming, advanced data analysis, and mathematical skills. Among higher cognitive skills, significant shortfalls are seen in critical thinking and problem structuring and in complex information processing. About 40 percent of the executives surveyed pointed to a shortage of workers with these skills, which are needed for working alongside new technologies (Exhibit 4).

Companies see retraining as key to acquiring needed skills and adapting to the new work landscape
Surveyed executives expect significant changes to their workforce skill levels and worry about not finding the right skills by 2030. More than one in four survey respondents said that failing to capture the needed skills could directly harm financial performance and indirectly impede their efforts to leverage the value from AI.
To acquire the skills they need, companies have three main options: retraining, hiring, and contracting workers. Our survey suggests that executives are looking at all three options, with retraining the most widely reported tactic planned to address the skills mismatch: on average, out of companies that mentioned retraining as one of their tactics to address skills mismatch, executives said they would retrain 32 percent of their workforce. The scale of retraining needs varies in degree. For example, respondents in the automotive industry expect 36 percent of their workforce to be retrained, compared with 28 percent in the financial services industry. Out of those who have mentioned hiring or contracting as their tactics to address the skills mismatch, executives surveyed said they would hire an average of 23 percent of their workforce and contract an average of 18 percent.
Occupational transitions will affect high-, medium-, and low-wage workers differently
All ten European countries we examined for this report may see increasing demand for top-earning occupations. By contrast, workers in the two lowest-wage-bracket occupations could be three to five times more likely to have to change occupations compared to the top wage earners, our analysis finds. The disparity is much higher in the United States, where workers in the two lowest-wage-bracket occupations are up to 14 times more likely to face occupational shifts than the highest earners. In Europe, the middle-wage population could be twice as affected by occupational transitions as the same population in United States, representing 7.3 percent of the working population who might face occupational transitions.
Enhancing human capital at the same time as deploying the technology rapidly could boost annual productivity growth
About quantumblack, ai by mckinsey.
QuantumBlack, McKinsey’s AI arm, helps companies transform using the power of technology, technical expertise, and industry experts. With thousands of practitioners at QuantumBlack (data engineers, data scientists, product managers, designers, and software engineers) and McKinsey (industry and domain experts), we are working to solve the world’s most important AI challenges. QuantumBlack Labs is our center of technology development and client innovation, which has been driving cutting-edge advancements and developments in AI through locations across the globe.
Organizations and policy makers have choices to make; the way they approach AI and automation, along with human capital augmentation, will affect economic and societal outcomes.
We have attempted to quantify at a high level the potential effects of different stances to AI deployment on productivity in Europe. Our analysis considers two dimensions. The first is the adoption rate of AI and automation technologies. We consider the faster scenario and the late scenario for technology adoption. Faster adoption would unlock greater productivity growth potential but also, potentially, more short-term labor disruption than the late scenario.
The second dimension we consider is the level of automated worker time that is redeployed into the economy. This represents the ability to redeploy the time gained by automation and productivity gains (for example, new tasks and job creation). This could vary depending on the success of worker training programs and strategies to match demand and supply in labor markets.
We based our analysis on two potential scenarios: either all displaced workers would be able to fully rejoin the economy at a similar productivity level as in 2022 or only some 80 percent of the automated workers’ time will be redeployed into the economy.
Exhibit 5 illustrates the various outcomes in terms of annual productivity growth rate. The top-right quadrant illustrates the highest economy-wide productivity, with an annual productivity growth rate of up to 3.1 percent. It requires fast adoption of technologies as well as full redeployment of displaced workers. The top-left quadrant also demonstrates technology adoption on a fast trajectory and shows a relatively high productivity growth rate (up to 2.5 percent). However, about 6.0 percent of total hours worked (equivalent to 10.2 million people not working) would not be redeployed in the economy. Finally, the two bottom quadrants depict the failure to adopt AI and automation, leading to limited productivity gains and translating into limited labor market disruptions.

Four priorities for companies
The adoption of automation technologies will be decisive in protecting businesses’ competitive advantage in an automation and AI era. To ensure successful deployment at a company level, business leaders can embrace four priorities.
Understand the potential. Leaders need to understand the potential of these technologies, notably including how AI and gen AI can augment and automate work. This includes estimating both the total capacity that these technologies could free up and their impact on role composition and skills requirements. Understanding this allows business leaders to frame their end-to-end strategy and adoption goals with regard to these technologies.
Plan a strategic workforce shift. Once they understand the potential of automation technologies, leaders need to plan the company’s shift toward readiness for the automation and AI era. This requires sizing the workforce and skill needs, based on strategically identified use cases, to assess the potential future talent gap. From this analysis will flow details about the extent of recruitment of new talent, upskilling, or reskilling of the current workforce that is needed, as well as where to redeploy freed capacity to more value-added tasks.
Prioritize people development. To ensure that the right talent is on hand to sustain the company strategy during all transformation phases, leaders could consider strengthening their capabilities to identify, attract, and recruit future AI and gen AI leaders in a tight market. They will also likely need to accelerate the building of AI and gen AI capabilities in the workforce. Nontechnical talent will also need training to adapt to the changing skills environment. Finally, leaders could deploy an HR strategy and operating model to fit the post–gen AI workforce.
Pursue the executive-education journey on automation technologies. Leaders also need to undertake their own education journey on automation technologies to maximize their contributions to their companies during the coming transformation. This includes empowering senior managers to explore automation technologies implications and subsequently role model to others, as well as bringing all company leaders together to create a dedicated road map to drive business and employee value.
AI and the toolbox of advanced new technologies are evolving at a breathtaking pace. For companies and policy makers, these technologies are highly compelling because they promise a range of benefits, including higher productivity, which could lift growth and prosperity. Yet, as this report has sought to illustrate, making full use of the advantages on offer will also require paying attention to the critical element of human capital. In the best-case scenario, workers’ skills will develop and adapt to new technological challenges. Achieving this goal in our new technological age will be highly challenging—but the benefits will be great.
Eric Hazan is a McKinsey senior partner based in Paris; Anu Madgavkar and Michael Chui are McKinsey Global Institute partners based in New Jersey and San Francisco, respectively; Sven Smit is chair of the McKinsey Global Institute and a McKinsey senior partner based in Amsterdam; Dana Maor is a McKinsey senior partner based in Tel Aviv; Gurneet Singh Dandona is an associate partner and a senior expert based in New York; and Roland Huyghues-Despointes is a consultant based in Paris.
Explore a career with us
Related articles.

Generative AI and the future of work in America
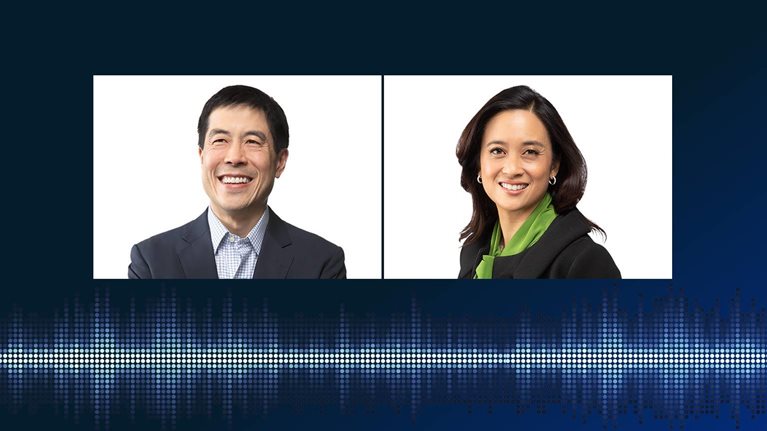
The economic potential of generative AI: The next productivity frontier
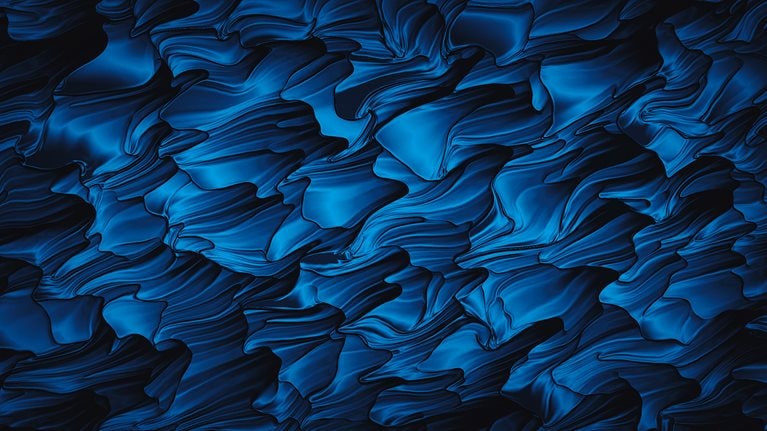
What every CEO should know about generative AI
Purdue Hospitality and Tourism Management graduate student wins best paper award for innovative technology research
Written By: Rebecca Hoffa, [email protected]
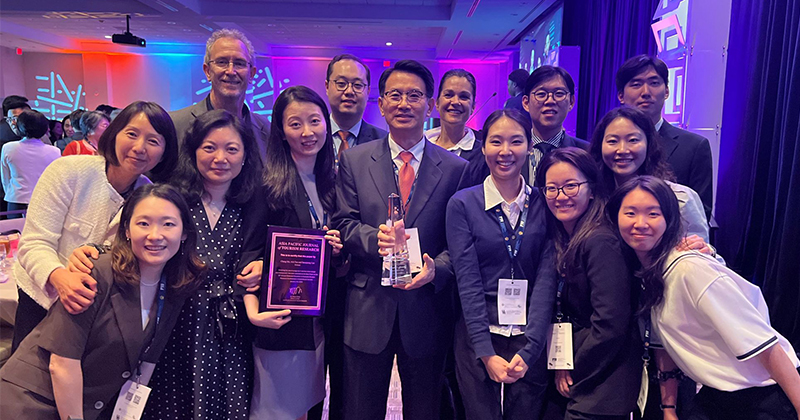
Evita Ma poses with the fellow Purdue HTM attendees at the 29th Annual Graduate Education and Graduate Student Research Conference in Hospitality and Tourism in January. (Photo provided)
As Starship robots deliver food to hungry Boilermakers across Purdue University’s West Lafayette campus, their presence is often welcomed like that of a neighborhood pet — students are often seen helping them when they get stuck or smiling and moving out of their way when they meet them on the sidewalk. When Alei (Aileen) Fan , associate professor in the White Lodging-J.W. Marriott, Jr. School of Hospitality and Tourism Management (HTM) and an expert in service innovation and experience design, helped one along its way one day, she was met with a low-tone, male voice saying, “Thank you.” This contradicted the “cute” vision Fan had in her mind of the robots being like her dog at home.
When Fan relayed the experience to her PhD student Chang (Evita) Ma , the College of Health and Human Sciences graduate student was inspired to investigate deeper how the combination of appearance and voice impacted the consumer’s overall experience in the service encounter.
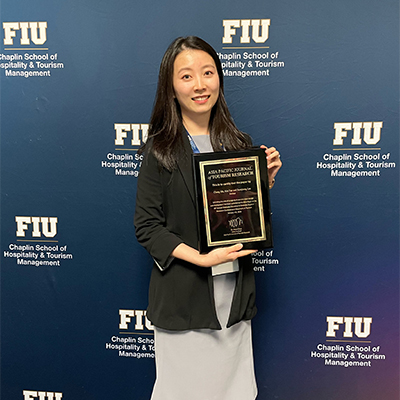
Evita Ma poses with her best paper award at the 29th Annual Graduate Education and Graduate Student Research Conference in Hospitality and Tourism. (Photo provided)
These efforts culminated in winning a best paper award at the 29th Annual Graduate Education and Graduate Student Research Conference in Hospitality and Tourism in January.
“I’m really honored,” Ma said. “As far as I know, for the past three years or so, no one from our school has gotten the award, so it was a pleasure to have that. It’s very competitive — over the 130-some presentations, I was selected as one of the four winners.”
The study looked at how people’s reactions differed when comparing matched, or congruent, voice and appearance and mismatched, or incongruent, voice and appearance. The researchers found that depending on the robot’s function, people tended to be either more or less accepting of when a robot’s voice does not match its appearance.
In a utilitarian scenario where the consumer really only desires the robot to perform a job function and doesn’t care as much about having an emotional connection, people often prefer the congruent voice and appearance because they feel the incongruent one is not well-designed or not capable of performing their desired outcome. When consumers are in a hedonic scenario where they don’t care as much about the functions the robot is performing but simply wish to have a connection or engage with the robot, the congruency doesn’t matter as much, and some of the surprising elements, such as the mismatched voice and appearance, may attract people to engage with it.
“We as human beings actually view things holistically,” Ma said. “We don’t separate the different parts.”
Considering how these distinct factors work together to shape consumer perceptions could ultimately shape the characteristics of future service robots to improve service encounters across the industry.
“It’s a timely topic,” Fan said. “Whether you like it or not, technology takes up a lot of our lives. This research provided practical guidelines for industries and companies on how to design different robots to better serve our customer.”
This study resulted as a product of Ma’s study “Decoding the Shared Pathways of Consumer Technology Experience in Hospitality and Tourism: A Meta-Analysis,” which examined the literature currently available to investigate the different types of technology and how humans interact with them. Ma ultimately noticed a gap in papers that combined elements — many simply looked at appearance or voice independently.
“Very few of the papers actually combine all the different subtle elements together; they just focus on one single perspective like appearance or voice,” Ma said. “So, I began looking at: What is the combination between those? Our initial idea was we wanted to know how the combination of design elements of service robots impacts the customer’s reactions and feelings of the service in different scenarios.”
Prior to coming to Purdue, Ma spent four years gaining industry experience at the Hospitality Financial and Technology Professionals nonprofit in Hong Kong, where she made many connections on the technology side of the industry and solidified her interest in coming to a very technology-focused university to earn her PhD.
“Purdue has such a strong background in terms of technology and engineering, so that was also one of the reasons I wanted to keep focusing on that for my research area,” Ma said. “After taking a class with Dr. Fan, I decided to join her team.”
Beyond research, Ma has fully immersed herself in the teaching and engagement areas of graduate student life as well. Ma teaches two 200-level marketing courses to undergraduate HTM students, where she’s maximized opportunities for the students to engage in experiential education. She’s also working on curriculum development with HTM faculty and has become involved in several graduate student organizations, including the Purdue Graduate Student Government, where she is a senator.
After graduating from the program, Ma plans to pursue a faculty position that allows her to combine her passion for research with her love for teaching and service.
“She’s really the star student,” Fan said. “When we evaluate a PhD student, there are three aspects: research, teaching and service. Evita is excellent in all of these.”

IMAGES
VIDEO
COMMENTS
Mechanical Engineering Department, Indian Institute of Technology Delhi, New Delhi, India. Abstract. Purpose - The purpose of this paper is to review the literature on maintenance management and ...
Empirical research in industrial maintenance management. There is a general lack of empirical research within the field of maintenance. When Fraser et al. (2015) reviewed the literature, they found that out of several thousand articles on the most common maintenance concepts, only 82 displayed empirical real-world evidence. In contrast, the ...
The paper is a comprehensive overview of discussed strategies, which indicates the most frequent maintenance models in the analysed papers. The number of papers regarding certain maintenance ...
The work presented in this paper is part of an ongoing project and aims to incorporate a new function in the existing computerized maintenance management (CMMS) of an automotive company to assist failure analysis and optimal periodicity definition of preventive interventions, considering costs [5].
Furthermore, this research paper will be a great impetus for future academic and industrial researchers to implement the Smart Maintenance Management function in small and medium enterprises through their research and to implement smart factories. CRediT authorship contribution statement. K. Velmurugan: Writing - original draft. S.
Abstract. The purpose of this paper is to review from early days until recent time the development of maintenance management methods from maintenance textbooks to give a glance view for researcher ...
This paper presents an extensive literature review on the field of condition-based maintenance (CBM). The paper encompasses over 4000 contributions, analysed through bibliometric indicators and meta-analysis techniques. The review adopts Factor Analysis as a dimensionality reduction, concerning the metric of the co-citations of the papers. Four main research areas have been identified, able to ...
This paper introduces a research project which aims to identify and analyse various influences on maintenance management. The research (using contemporary social sciences investigation methods) is conducted by experienced engineers, and is part of a larger project on the nature of engineering work. The paper also provides a literature overview ...
The standpoint of the paper by McComb, Kennedy, Green and Compton is that launching and supporting successful maintenance projects is an overlooked aspect of maintenance management research. So, the paper examines the effects of four important factors on project success, i.e. resource allocation, team leader authority, significant project ...
This paper focused on practitioners' descriptions of leadership based on their experiences and projected demands of leadership in maintenance. Research in maintenance management is most often dominated by technological perspectives (Kłos and Patalas-Maliszewska Citation 2018; Bodo, Bertocco, and Bianchi Citation 2020; Ashjaei and Bengtsson ...
Literature on classification of maintenance management has so far been very limited. This paper reviews a large number of papers in this field and suggests a classification in to various areas and sub areas. Subsequently, various emerging trends in the field of maintenance management are identified to help researchers specifying gaps in the ...
Academia.edu is a platform for academics to share research papers. Maintenance management models: a study of the published literature to identify empirical evidence. ... and these 13 journals represented 67 per cent of the total books/articles referenced in this paper Maintenance management models 653 Major databases Popular maintenance models ...
In this paper, the operation and maintenance management process of equipment is divided into three stages: fault prediction and warning, fault diagnosis and processing, and fault rule summary. ... Research will help to improve the efficiency and safety of equipment operation and maintenance, and have a reference significance for integrated ...
2.1 Computerized Maintenance Management Systems (CMMS). A CMMS is an asset that supports maintenance strategy based on an information system and a set of functions aimed to produce indicators by processing information to support maintenance activities [].In this context; CMMS enables maintenance management to control a wide variety of data on maintenance workforce, spare parts inventories ...
This paper introduces a research project which aims to identify and analyse various influences on maintenance management. The research (using contemporary social sciences investigation methods) is ...
Abstract: e purpose of this paper is to present the maintenance management status in Moroccan companies. e first part is based on the literature; it reviews the main maintenance models. e second part is resulted from a pilot survey about management maintenance in Moroccan companies. e study was performed by conducting a
The purpose of this research paper is to study the impact of effective maintenance management on improvement of productivity, profitability of production system and effective workplace management in an ... Maintenance management tools such as KAIZEN, TPM, 5S, 6σ, etc. might be the only adequate model that identifies the relationship between ...
From this review it found that the paper also revealed from time to time, maintenance management adapt and improve to gain more sustainable maintenance, including the new shift of paradigm of maintenance itself. The originality and contribution of this research is that the paper contains many maintenance management methods from maintenance text...
The importance of this research paper is to provide a reference guide for the company in general to know the selection criteria for the appropriate road maintenance management strategies. The study provides a significant source of secondary data for future users to get knowledge, skill, and understanding of road maintenance management strategies.
This paper is based on the information fusion technology to realize the research on the maintenance and quality control of medical equipment. Measuring the information data δε(ϱ)(ϱ=1,2, ..., γ) obtained at time ϱ and positioning it on the number axis, the absolute distance between the information data δε(ϱ) and δζ(ϱ) is set as:
This paper proposes the use of the K-means clustering algorithm to carry out early-warning interval nodes for cost deviation in the operation and maintenance phases of construction projects. In order to address the discontinuity problem of sample data while preserving the original clustering principle, the boundary mean operator is employed to ...
Based on the publications from two databases during 1998-2020, this paper presents a systematic literature review on pavement maintenance effectiveness evaluation to summarize the current trend and identify the research gap that must be addressed for a sustainable maintenance management.
The expansion of photovoltaic systems emphasizes the crucial requirement for effective operations and maintenance, drawing insights from advanced maintenance approaches evident in the wind industry. This review systematically explores the existing literature on the management of photovoltaic operation and maintenance. Through the integration of bibliometric analysis and the Preferred Reporting ...
Laundry firms currently use a manual system for the management and maintenance of critical information. The current system requires numerous paper forms, with data stores spread throughout the laundry management infrastructure. Often information is incomplete or does not follow management standards.
Design/methodology/approach - For this paper two comprehensive reviews of the literature were undertaken, first, to identify and categorise the various maintenance management models, and second ...
For the United States, we use the midpoint scenario, based on our earlier research. We also estimate the productivity effects of automation, using GDP per full-time-equivalent (FTE) employee as the measure of productivity. We assumed that workers displaced by automation rejoin the workforce at 2022 productivity levels, net of automation, and in ...
The similar involvement of both PHR2 and SPX1/3 in arbuscule maintenance offered a conundrum. Overexpression of SPX1 and SPX3 would be expected to impair PHR activity in arbuscule-containing cells, and therefore to mimic a phr2 knockout with respect to arbuscule maintenance. Since SPX1/3 overexpression instead enhanced the degradation of ...
In this paper, we present a. literature review on "maintenance effecti veness", here defined as the level to which a maintenance policy. fulfills its pre-defined objectives or optimizes ...
Overview. Our mission is to assist Pennsylvanians in leading safe, healthy, and productive lives through equitable, trauma-informed, and outcome-focused services while being an accountable steward of commonwealth resources.
These efforts culminated in winning a best paper award at the 29th Annual Graduate Education and Graduate Student Research Conference in Hospitality and Tourism in January. "I'm really honored," Ma said. "As far as I know, for the past three years or so, no one from our school has gotten the award, so it was a pleasure to have that.